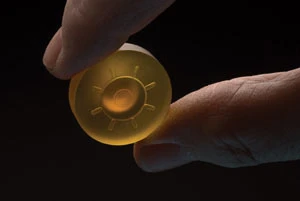
Ah, well no. Just because the two are often machined on the same types of machines – VMCs or HMCs – doesn't mean the processes are the same. As a matter of fact, the similarity pretty much starts and ends with the machines, which had better be the best if you're even going to think about machining plastics.
Applied Engineering Plastics Inc. (AEP) has made it their business to machine high-performance plastics/polymers. The company may be young (just two years), but the three partners have been in plastics for almost 20 years, each. "We founded AEP two years ago concentrating on an underserved niche market: the need for precision machined, high-performance plastic components," says Chris Klope, president.
"There are two distinct overlapping issues: one, the need for high-performance plastics/polymers that are designed specifically to replace metals in critical applications; and two, developing ways to successfully machine these plastics to tolerances that have traditionally proven very difficult to hold."
Plastics physically move much more with temperature change than do their metal counterparts. So, machining these materials, achieving the necessary surface finishes, and holding precision tolerances require certain speed and feed parameters, particular tool geometries and workholding scenarios, and experience machining high-performance plastics.
Plastics for Medical
"We've produced instruments for the ear, nose and throat industry, and our clients charge a good price for their equipment," says Klope. "One of the complaints from doctors was the anodization on aluminum instruments wearing off, leaving them looking cheap. At $165 per hour, the last thing they want is shoddy looking equipment.
"In this case, we went with a plastic that's lighter than aluminum, so the doctor incurs less fatigue, the color is integral to the material – and can't wear off. The plastic is just as durable as aluminum. You can cut threads in it, you can put a fine surface finish on it, plus, it's cost effective."
AEP also machines plastic that goes into surgical instruments, as well – handles, positioning pieces and fixtures. These materials not only perform as well or better than stainless steel, they are lighter, and they're also "radiolucent," which means an X-ray can see through them – this helps the doctor to position the components when they're in the middle of surgery. Stainless steel will shadow out anything that's behind it. Radiolucent plastics will allow the X-ray to penetrate it, and doctors can actually see what's beneath the fixture or the jig.
"Then we machine a part out of acrylic where the finish-machined part requires a polished finish," Klope says. "We're the only people in the country that I know of that can do this job. The part comes off the Bridgeport polished. Most people would have to achieve that in a secondary operation. We found a way to do it with tool geometry, which allowed us to produce the part on the Bridgeport, complete."
Best Machine(s) for the Job
When Klope and his team started the search for just the right machine for their unique needs, Rich Pohrer of Zimmerman-McDonald Machinery, Inc., suggested they look at the Hardinge Group and its array of equipment. Klope and partners took a look – a very close look – and liked what they saw.
"Based on the capabilities of Bridgeport's range of VMCs and HMCs, the Bridgeport XR 760 VMC – followed eight months later by a Bridgeport XR 700 HMC – were very attractive machines for the money and offered the work envelopes we needed. Further, once we got the Bridgeports in house, their rigidity, stability, reliability and ease-of-use enabled us to generate critical surface finishes and hold tolerances that are all but impossible, but are absolutely required on the plastic components that we produce."
The Bridgeport XR 760 high-performance VMC is compact in design (85" x 118") with a high-performance 12,000rpm Weiss spindle, automatic grease replenishing system, 30-tool bi-directional, random access ATC, through-spindle coolant delivery, and Fanuc 18i MB control. Repeatability, 0.000 16" and positioning, 0.0004". A 25hp belt-driven motor powers the spindle; rapids are 1,692ipm (X and Y), 1,417ipm (Z).

The spindle design on the Bridgeport XR 700 highperformance HMC incorporates five bearings – four contact bearings on the front, one roller bearing on the rear.
The Bridgeport XR 700 high-performance HMC features a 19.7" x 31.5" pallet size, 60-tool bi-directional ATC, and a 12,000rpm spindle powered by a 25hp GE Fanuc belt-driven motor. Positioning, 0.000 60", and repeatability, 0.000 30". X, Y, and Z axes of 27.56", 19.69" and 22".
"We've machined parts as small as the head of a wooden match," Klope says. "At the other end of the scale, we have a CNC router that allows us to machine nested components from sheets of 5ft x 10ft plastic. The thing you have to keep in mind about plastics is their lightweight enables us to machine large and small components with basically the same types of equipment. The keys to our success are rigidity and high spindle speeds, both of which the Bridgeports deliver."
However, this is not to suggest that Klope doesn't keep his eye on cycle time. "Having a finished part every cycle is a big issue around here," he says. "And that's where the fourth axis interface plays an important role." Currently, he says, they're running medical device handles that require machining on all sides. They use the fourth axis to reduce setup, so that an operator is not turning the part continuously in a vise. Instead, he just rotates the part with the fourth axis, loads it once, and gets a finished part out in a single cycle.
AEP is also using the fourth axis on the Bridgeport XR 700 HMC to allow them to do angles, as well as side holes and more.
The twin pallets with tombstone fixtures on the Bridgeport XR 700 HMC serve as a great example of cycle time reduction. The number of parts per fixture depends on a number of things, for example the size of the component. On large jobs, Klope says, they can get two finished parts per cycle. Other jobs, they'll get eight finished parts per cycle. It just depends on the size of the part and how they fixture the parts on the tombstones. Often they'll run a job that is 2in2, and the next day a job that's 18in2. So, the range run on the XR 700 HMC is really wide, but they use the tombstones to maximum efficiency. "Often we run multiple jobs on a single fixture," Klope says. "We'll load up two sides of the fixture with one part, and the other two sides with a different part. Then, we'll move to the free pallet, and begin loading that fixture."
The feature that has really made a difference for AEP is the massive 40-taper Weiss spindle that has a unique grease replenishment system along with a dualcontact (BIG PLUS) flange fit system. "The Bridgeport people have come up with a different type of spindle nose that actually has face and taper contact with the toolholder," Klope says. "This gives us a much more rigid machine; we get almost no vibration. This spindle nose design virtually removes all machining lines without our having to go to balanced toolholders, and we can run at much higher speeds. We can take a 1.5" depth of cut with a 1" endmill with full tool engagement."
Cool Running
Klope says they use a water-soluble coolant. Another Bridgeport feature that is very important to them is the 300psi through-spindle coolant, which helps maintain size and surface finish. If you introduce heat into a plastic, you'll cause it to grow and expand out of tolerance. It's very important to cool the tool and to keep it from building up heat. Tool geometry has a significant impact on cycle time and finish quality.
"Also, the self-lubricating feature on both our Bridgeport spindles is really worth it," says Klope. "Most spindles, even those that are permanently lubed and sealed, when you push them at 12,000rpm for extended duty times, the lubrication begins to break down due to rising spindle heat. The grease then spins off the bearings, and before you know it, you've got bearing seizure and spindle failure. With the Bridgeport selflubricating option, the spindle gets lubed every 70 hours – automatically and without operator intervention."
Cautionary Fixtures
Workholding, Klope admits, is a very difficult challenge in machining plastics. Magnetic workholding doesn't work, for obvious reasons. Also, applying too much pressure on vise jaws will deform the product. Let's say you're drilling or milling a hole, and there's too much vise pressure, the hole will invariably be egg-shaped.
"Workholding is based on experience," Klope says. "I know this is not very helpful, but at this stage, workholding of plastic is best guided by experience. A lot is just knowing what works and what doesn't. Many times we build our own fixtures and machine special jaws from special materials. This way we encapsulate parts without distorting their shape. The other thing we do is maintain consistent vise pressure, whether it's on a VMC or HMC. Once we find the pressure that holds the product in position without distortion, we'll set a gauge, record the pressure, and consistently use that vise pressure for that particular job.
"That said, it's not entirely unusual for us to use a conventional vise," continues Klope, "but what we'll do is create custom jaws to hold the product."
Klope notes that on some of the higher performance materials they're able to hold ±0.001", which for plastics is considered tight. But take a material like Teflon – a great material, a very low coefficient of friction, heat resistant, FDA compliant – and machine a poker chip out of Teflon to ±0.003", then hold it in your hand, the heat from your hand will cause the chip to grow out of tolerance. So the trick is knowing the coefficient of linear thermal expansion of materials, and then knowing what material would be best in which application."
Chips
The final challenge is what do you do with plastic chips? This is a challenge that the Hardinge Group and AEP have embraced together, and they're still working on better solutions. "With some plastics you get a very stringy chip that is almost impossible to break," Klope says. "How do you evacuate that from the machine? How do you keep it from wrapping around and getting in the spindle? How do keep it from wrapping around the tool and melting, and introducing heat into the machining surface?"
The other challenge with plastic chips is they float, so traditional chip evacuation methods, like conveyors or augers, are not nearly as effective as they are with metals. With plastics, chip evacuation is tricky when today's machine tools are not manufactured with machining of non-metals in mind.
Parts, Other Than Medical
A short list might include plastic gears and sprockets. For custom packaging equipment, there are star wheels, worm gears, bushings, bearings and wear pads.
AEP's customers' equipment is unique to particular industries, like medical, semi-conductor and physical testing. Some of these customers make machines that test agricultural products, paint samples, food products, and AEP machines special components from FDA-compliant materials to be used in those applications. These materials are inert and won't cross-contaminate the product or the sample, and they need to be custom machined just for those machines.
"Machining plastics, as opposed to metals, is rife with challenge," concludes Klope. "I think every potential plastic has its own baggage of machining challenges. That's why you need a superior machine – extremely stable, rigid, powerful, and a great team standing behind it. And that's what Bridgeport gives us."
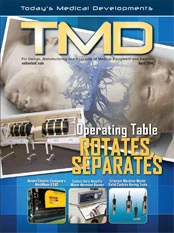
Explore the April 2008 Issue
Check out more from this issue and find your next story to read.
Latest from Today's Medical Developments
- 10 challenges facing the manufacturing industry in 2025
- Optimizing production of high-precision components through collaboration
- An inside look at the defense maritime industrial base
- Why manufacturing, intralogistics companies need to embrace the cloud
- February 2025 US cutting tool orders total $198.6 million
- The Smoothest Surfaces For Your Toughest Materials
- Extraordinary Starts Where Limits End | Okuma
- DISCOVER MORE WITH Mazak Northeast event