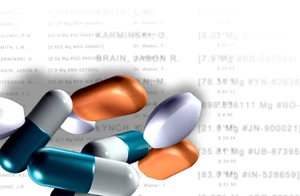
Machine vision can be used in a wide variety of manufacturing operations where accuracy and reliability are important for repetitive inspection tasks. Common tasks include: verifying date codes on food packaging, inspecting automotive parts for proper assembly, performing robotic guidance for pick and place operations, verifying the colors of pills used for pharmaceuticals, reading bar codes on parts and verifying the presence of logos on products.
When determining the need for a machine vision system, there are many important factors to consider. These systems contain a wide array of components that can directly affect the system's performance. To take full advantage of powerful vision systems, it's important to learn the basics about what makes up the system, how it is implemented and the importance of proper planning. Because the uses of machine vision are so diverse, specific components can vary from system to system.
COMPONENTS USUALLY FALL INTO THE FOLLOWING GENERAL CATEGORIES:
- Cameras and optics, which consists of one or more cameras and lensing, take pictures of the part being inspected.
- Lighting is used to illuminate the part, so that the best possible image can be acquired by the camera.
- Part sensor sends a trigger signal when it senses that a part is in close proximity and also tells the machining vision system when a part is in the correct position for an image to be acquired.
- Frame grabber, usually in the form of a plug-in board that is installed in the PC, interfaces the camera to the host computer by taking the image data provided by the camera and converting it into information for use by the host PC.
- PC platform, the key element of a machine vision system, is often industrial- grade or ruggedized in order to withstand vibration, dust and heat.
- Inspection software is used for creating and executing programs, processing incoming image data and making PASS/ FAIL decisions.
- Digital I/O and network connection makes up the interfacing through which the machine vision system communicates with outside systems and databases.
Careful planning and attention to detail will help ensure that inspection systems meet application needs. The following is a checklist of issues to consider: Know your goals. Decide what you want to accomplish during the inspection task. Know your speed requirements. Many machine vision software packages incorporate a clock/timer so that each step of the inspection operation can be closely monitored. Choose your hardware wisely. A machine vision system is only as strong as its individual components.
WHEN CHOOSING COMPONENTS INVOLVED IN THE IMAGE PATH, KEEP THE FOLLOWING IN MIND:
- Camera selection is directly tied to the application requirements and typically involves three main criteria, monochrome or color acquisition, part/object motion and image resolution. Cameras should be high quality and rugged enough to withstand vibration, dirt and heat present in an industrial environment.
- When poor optics or lighting are used, even the best machine vision system will not perform as well as a less capable system with good optics and adequate lighting.
- Using the wrong frame grabber can result in errors being introduced into the image data.
- Knowing what the system can and cannot see will help to avoid false failures or other inspection errors.
- The selection of software will determine the length of time required to generate and debug inspection programs, what inspection operation can be performed and how well those operations can be performed.
- Communicating and tracking of the data is conveyed via the digital I/O board, which is connected to the manufacturing line's PLC (programmable logic controller).
- When selecting components for a machine vision system, consider future production requirements and changes. Planning ahead will not only save time, but it will also help reduce the overall cost of the system.
Remember, a machine vision system is only as good as its weakest component and only as accurate as the information it receives. Spending the time and the effort to carefully select and set up the right components will result in a trouble- free and resilient visual inspection system.
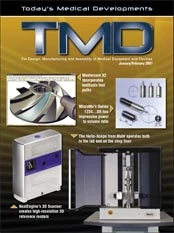
Explore the January February 2007 Issue
Check out more from this issue and find your next story to read.
Latest from Today's Medical Developments
- The role of robotics in precision medical device manufacturing
- Swiss Steel Group’s UGIMA-X machinable stainless-steel sets
- #51 - Manufacturing Matters - The Impact of M&A in MedTech 2024
- Visual Components: 25 years of simulation and programming software innovation
- Zimmer Biomet announces definitive agreement to Acquire Paragon 28
- Discover an innovative technology for EMI/ESD/TVS suppression
- Teleflex to acquire BIOTRONIK’s Vascular Intervention business
- Innovation at Global Industrie 2025