
MAJOR ADVANCES IN CARDIAC SURGICAL PROCEDURES CONTINUE TO MAKE HEADLINES AS NEW, LESS INVASIVE PRODUCTS ARE DEVELOPED TO PRODUCE MORE EFFECTIVE PATIENT OUTCOMES. ONE SUCH DEVICE ADDRESSES THE CHALLENGES OF SURGICALLY PLACING A SUTURELESS, SCREW-IN LEAD ON THE HEART'S EPICARDIAL SURFACE.
Designed by Enpath Medical, Inc., Plymouth, MN, the FasTac Flex steerable lead implant tool uses less invasive mini-thoracotomy and thoracoscopic approaches. The device works in conjunction with Enpath sutureless epicardial leads and provides the surgeon with remote distal deflection capabilities, remote lead rotation for insertion of the helix into the heart's myocardium and remote lead release, along with regrasping capabilities.
Molded by Minnesota Rubber and QMR Plastics for Enpath Medical, this product is a prime example of a growing trend in the medical device industry – partnering with a qualified and experienced supplier to completely manufacture newly designed products. Not only has the outsourcing arrangement proved effective for Enpath Medical, it has facilitated a timely introduction of the FasTac to the medical community.
"The innovative, steerable design was very challenging," says Peter Horwich, Enpath's marketing manager. "Working from our original design concept, Minnesota Rubber and QMR Plastics quickly responded to our needs and delivered production quantities in less than nine months. With 32 components in the final assembly, this was a remarkable achievement."
"With the manufacturing support we are receiving from Minnesota Rubber and QMR Plastics on the FasTac Flex project, we are now able to focus on developing and marketing these products," states Horwich.
Possessing the required medical device manufacturing certifications, Minnesota Rubber and QMR Plastics brought more than 60 years of rubber and plastics Medical found the supplier's medical molding experience to the table. Enpath silicone overmolding capabilities, along with a successful history in developing innovative sealing devices of particular interest. Integrating these into successful product assemblies is very important in medical device manufacturing. Another important factor is the proximity of the Minnesota Rubber and QMR Plastics operations, including their mold design center, to Enpath Medical. Horwich said the outsourcing of the FasTac Flex to the company provided a depth of experience and knowledge needed for the successful development of such a complex product.

Component molding for the FasTac Flex is done in QMR's class 100,000 molding facilities on Toyo PLCS9 presses equipped with Yushin robots.
WORKING PROTOTYPES AND PROCESS DESIGN ACCOMPLISHED IN LESS THAN 60 DAYS
The FasTac Flex consists of a handle assembly, including a release lever, rotation collar and rotatable wheel that deflects the collet at the distal tip of the shaft from 0° to 75°. The rotation collar is used to rotate the lead for fixation, and the release lever opens the collet for release or regrasping of the lead. The shaft of the tool incorporates lead management grooves that hold the lead body. In all, there's a total of 32 components which integrate into a single, functioning assembly without welding, fasteners, screws or nuts.
Minnesota Rubber and QMR Plastics transformed Enpath Medical's product concept into a manufacturable product that achieved functionality targets with the first operating prototype delivered in about 60 days. "Response time was very important to us on this project," reports Horwich.
Using SolidWorks 3D CAD software, we took Enpath Medical's concept and transformed it into a manufacturable product in less than two months," reports Larry Klimek, QMR design engineer. "We did all of the detail work to achieve functionality of the product. We designed the internal components, the snap-fit design and material formulation specification. We took their CAD designed style and shaped and refined it so that all of the internal components fit and operated properly. This was challenging in keeping with a compact, ergonomic design that was comfortable to handle and easy to operate. The design had to instill confidence in the user."

Without using fasteners, screws, nuts or welding, the 32 components integrate accurately into a completed assembly, which is done manually in just minutes.
NEW AUTOMATED EQUIPMENT IN CLASS 100,000 MOLDING ENVIRONMENT
Three major components were designed in mating halves that snap together: the handle assembly, the rotation collar and the rotatable wheel. Because this type of project demands component level accuracy, SolidWorks software is especially useful in ensuring that these sub-assemblies meet the design specifications. Using the eDrawings design communication tool, for example, enabled sharing sketches and models of these components as they were developed, so that functional and aesthetic aspects could be discussed between designers at Enpath Medical, Minnesota Rubber and QMR Plastics. Recipients could zoom in, rotate and otherwise manipulate a solid model on screen as if they were holding it in their hands.
"We were able to really reduce our design cycles," states Klimek, "and create an open communications pipeline between Enpath Medical, our toolmakers, moldmakers and design team, cutting weeks off the development time."
MATERIAL SELECTION PROVIDES FUNCTIONAL, AESTHETIC AND STERILIZATION BENEFITS

Clean room, quality inspection and validation technicians at Enpath Medical provide assembly, inspection and packaging of the FasTac Flex product prior to shipment. Enpath Medical team members celebrating the successful product launch are: Cynthia Morton, Hraren M. Menke, Saviene Phairny, Janet nelson, Neuj V-Vie, Janet Critxx, Christopher Alnel, Grer Lee, Chive Lee, Lahlee Mona.
Klimek notes that FasTac Flex, like most medical devices, had material restrictions and functional requirements that limited material choices. All plastic materials used in the FastTac Flex, for example, had to withstand ETO sterilization and be part of Enpath Medical's biocompatability database, since the device is inserted into the chest cavity.
A polycarbonate resin formulation was used for all of the molded components. To provide "touch/feel" control of the rotation collar, rotatable wheel and the release switch, a sanoprene elastomer formulation was overmolded on those components. Custom colorization of all components completed the desired aesthetics and overall "look."
"Having Minnesota Rubber and QMR Plastics handle the entire component manufacturing process made sense the further we got into product design, mold design/build and manufacturing process," reports Horwich. "They had all the credentials backed up with the newest capabilities. That, plus good communication, was important to the success of this project, but the overriding factors were their capabilities and responsiveness."
SUCCESSFUL PRODUCT LAUNCH
"With complementary manufacturing facilities augmenting our assembly, quality testing and packaging operations, Empath Medical has all of the needed resources to bring the FasTac Flex into a full scale product launch," says Horwich. "We have the trained personnel to handle the volume generated by the FasTac Flex and also our next generation of products soon to follow."
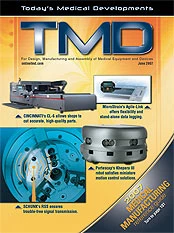
Explore the June 2007 Issue
Check out more from this issue and find your next story to read.
Latest from Today's Medical Developments
- HERMES AWARD 2025 – Jury nominates three tech innovations
- Vision Engineering’s EVO Cam HALO
- How to Reduce First Article Inspection Creation Time by 70% to 90% with DISCUS Software
- FANUC America launches new robot tutorial website for all
- Murata Machinery USA’s MT1065EX twin-spindle, CNC turning center
- #40 - Lunch & Learn with Fagor Automation
- Kistler offers service for piezoelectric force sensors and measuring chains
- Creaform’s Pro version of Scan-to-CAD Application Module