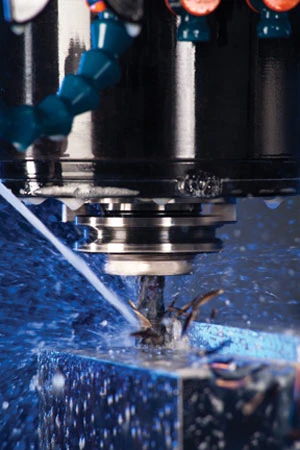
Machining a chunk of high-strength material into a sophisticated surgical instrument is no simple task.
The demands are understandably high - minute part dimensions, critical tolerances measured in microns and ultra-fine finishes. But the materials, spectacular for their respective end uses, are typically wicked nasty to machine.
With demands like those, you want to optimize the performance of every element in the process. Assuming you have the precise machine set-up and the right coolant for the job, it all comes down to the tool.
Since the 1970s, tool coatings and application methods have made huge improvements in machinability. But what role does tool coating play in maintaining tight tolerances and fine finishes for medical-grade machining?
"The coating is not everything," says Tim Elfreich, sales manager for IMCO Carbide Tool in Perrysburg, OH. "But it affects everything." That, he says, he learned from IMCO's years of R&D work in cutting tool materials and designs. A manufacturer of premium carbide endmills, IMCO maintains significant investments in research. From heat generation to chip removal to the effectiveness of the cutting edge and tool life, Elfreich says, the right coating makes a significant difference in productivity and profitability.
TOUGHEST COATING
Machining in difficult materials became far less difficult with the development of the titanium-aluminum-nitride (TiAlN) family of ceramic coatings. But coating suppliers soon found that increasing the amount of aluminum in the formula made the coating even more heat resistant, resulting in AlTiN. At high temperatures, common with high-speed machining, the added aluminum content bonds with available oxygen to form an aluminum oxide outer layer, increasing the coating's hardness and stability. At 4,500HV, AlTiN is 73% harder than TiAlN (2,600HV), 3x to 4x harder than a cobalt-bonded carbide substrate, and 5x harder than highspeed steel tools.
Some manufacturers, including IMCO, take coating development even further. The company develops its own unique combinations using multiple coating formulas and substrates.
"With inserts there are a lot of coating options," Elfreich explains. "That is a lot of guesswork when working in tough materials. How do you know which coating is best for this substrate and geometry? At IMCO, we make solid carbide rotary tools. Our research takes the guesswork out of coatings.
We test every viable combination and identify the one that consistently performs the best." Elfreich points to research conducted for its high-performance POW-R-FEED/M90 product.
PROVING GROUND
"We designed POW-R-FEED because we wanted a tool to achieve a high metal removal rate even with heavy tool engagement in tough materials. High metal removal is key with titanium. Take too little material with each chip and the material tends to workharden," Elfreich says. "Machining in those materials creates an incredible amount of heat. But, titanium cannot dissipate all that heat, it holds it there. That can cause thermal cracking and tool failure. So, if the tool is optimized, you turn to the coating for a solution." The best way to dissipate heat, he says, is to deflect it back into the chip and remove it. IMCO's goal was to develop a coating/substrate combination to meet that dual challenge. "Even in its alloy forms, titanium retains some of its ‘gummy' characteristics," Elfreich explains. "So we wanted a special coating in the AlTiN family that would add lubricity to provide high heat resistance and help evacuate the chip. The coating is essential in removing the chip." If chips remain in the cutting zone, the high temperatures alone can result in chipping and deformation. That heat and titanium's tendency to react with tool metals weld the chips to the cutting edges, causing cratering, flank wear and chipping.
60% LONGER TOOL LIFE
"In one test running in 6Al-4V titanium with all other parameters the same, we pitted the POW-R-FEED/M90 against a competitor's tool with a different coating. The POW-R-FEED/ M90 ran 60% longer, simply due to the AlTiN-X coating," Elfreich says.
IMCO also tested POW-R-FEED in 17-4PH stainless steel, 304 stainless steel and 4340 steel, as well as in 6Al- 4V titanium before it was launched. Some of its durability comes from the way the coating is applied. The PVD process applies AlTiN-X in a film thin enough to allow for multiple layers, providing far greater protection for the tool substrate than a single layer.
By the same token, if you want the tool to stand up to the battering of milling in difficult materials, Elfreich says, you have to start with a substrate that can withstand it.
"The tool has to have optimal features in the first place, before any coating is applied."
THE SUBSTRATE
With carbide tools, studies show that the smaller the grain, the tougher the tool. Elfreich says IMCO's research bears this out. "The small grain structure of the substrate material, combined with the amount of cobalt binder in the composition, gives the tool 20% higher transverse rupture strength.
"Think about it. The tool is spinning at 2,000 times a minute, pounding into this material. And in milling, the cutting edge does not always stay in the cut as it does during turning.
The substrate has to be incredibly tough to take that kind of shock."
"Additionally, you cannot get a fine finish with an irregular cutting edge. No coating can improve that. The coating is just a few microns thick. It will not smooth the surface; it will only copy that surface, like applying paint to a wall" he says.
"You have to start with the right grinding techniques to impart the smooth cutting edges and relief angles." To illustrate, Elfreich cites the IMCO grinding process.
"Our choice of diamond wheels and speeds and feeds used in our grinding process optimize the smoothness of the cutting edge and, in turn, the smoothness of the workpiece finish.
You have to have a precision-ground cutting tool to get a smooth finish. And the smoother the finish, the less time and money you spend with additional finishing operations."
HARMONICS
No coating can take the place of a well-designed tool.
"Flute design, flute spacing, cutting edge radius all affect how the material interacts with the tool during machining," Elfreich says. "Also of impact is the use of a corner radius to help extend tool life when roughing. A corner radius makes the corner stronger." Additionally, people typically use serrated carbide or cobalt roughing endmills for higher metal removal rates.
Although they achieve good chip control, serrations on roughers leave very poor finishes, requiring a second endmill with a solid cutting edge for medical-grade finishes.
"Robust design can reduce or eliminate that need," Elfreich says. "With POW-R-FEED we developed a design without serrations that achieves the high MRR of a rougher. So you get a good finish even during the roughing passes." Additionally is IMCO's research on the effectiveness of unequally spaced cutting edges to alter harmonics when milling in difficult materials.
The 5-flute POW-R-FEED (in addition to the 4-flute for roughing) provides an extra cutting edge for an even better finish.
The added flute also helps extend tool life, especially when machining very difficult materials like nickel-based alloys.
"When you are not using tools with unequally spaced cutting edges, IMCO has found that a helix higher than 30° achieves a higher shear plane for more efficient machining," he states.
This is the case with IMCO's enDuro cutting tools.
"It is all in the design. If you are machining deeper pockets or slots in more austenitic types of stainless steel, a three-flute design maximizes chip evacuation. On the other hand, the five-flute tool yields a better finish than three flutes or four. So you pay only for the performance you need.
"Whichever design you choose, like the medical component you are machining, the cutting tool will perform only as well as it is made. The underlying tool is critical. The coating is just one part of the tool's overall design," Elfreich concludes.
IMCO Carbide Tool Inc.
Perrysburg, OH
imcousa.com

Explore the August 2009 Issue
Check out more from this issue and find your next story to read.
Latest from Today's Medical Developments
- German robotics and automation in a downturn
- Blueshift’s AeroZero
- November USMTO grow from October
- Platinum Tooling’s custom and special tooling
- Top 5 global robotics trends 2025
- Accumold’s micro molding innovations
- Methods Machine Tools, Multiaxis, announce AI solution investment
- MGS to showcase global expansion and healthcare CDMO expertise