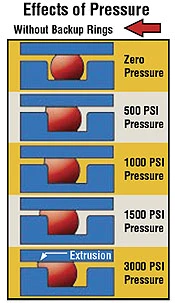
A basic manufacturing component that has to be right or an entire project can be ruined.
By Christopher M. Chiodo, Apple Rubber Products, Inc.
Elastomer seals are unlike any other materials that design engineers confront. Metal or plastic parts, for instance, are probably failing if visibly distorted. But, an O-ring must be deformed to function properly. In fact, an O-ring that is not squeezed and stretched in its application is the wrong O-ring. Here are some considerations to take into account when designing with seals and O-rings.
The definition of an O-Ring
An O-ring is a doughnut-shaped object, or torus. The opposite sides of an O-ring are squeezed between the walls of the cavity or “gland” into which the O-ring is installed. The resulting zero clearance within the gland provides an effective seal, blocking the flow of liquids or gases through the gland's internal passage. An O-ring is defined by its dimensions (based on inside [hole] diameter and cross section), durometer (Shore A hardness), and material composition.
Why an O-Ring Works
As the illustration shows, a properly designed sealing system incorporates some degree of initial O-ring compression. At atmospheric pressure, only the resiliency of the compressed O-ring provides the seal. However, as system pressure activates the seal, the O-ring is forced to the low pressure side of the gland.
Designed to deform, the O-ring “flows” to fill the diametrical clearance and blocks any further leakage. The following illustration shows a progressive application of pressure and the effect it has on the seal. Pressure, as well as many other considerations, determines the effectiveness of a seal.
Pressure Considerations
Sealing Pressure - Sealing pressure is the force exerted by compression of the seal between the mating surfaces forming the gland itself and external forces (i.e. the fluid being sealed) transmitted through the seal. A physical barrier is formed when the force from compressing the seal and pressure applied by the fluid being sealed causes the seal to fill all leak paths.
Low Pressure Sealing - In a low pressure sealing application, system pressure does not cause a noticeable increase in the seal's sealing force. Because of this, all sealing force must come from the ability of the seal to deform and create a barrier by compression of the seal. Surface finish on both the seal and gland are critical to an effective seal.
High Pressure Sealing - In a high pressure sealing application, system pressure causes a noticeable increase in the seal's sealing force to fill all leak paths. Because this pressure activates the seal, the compression of the seal and surface roughness are not as important as in low pressure sealing.
Dimensional Considerations
Inside Diameter - To provide an effective seal, the O-ring's inside diameter (I.D.) must be smaller than the piston groove diameter, so that the O-ring is slightly stretched, fitting snugly in the groove. This stretch should be between 1%-5% with 2% as the ideal in most applications. A stretch greater than 5% is not recommended. The resulting stress on the O-ring will cause accelerated aging and cross section reduction.
Cross Section - When calculating the cross section (C.S.) of an O-ring, you need to consider the size of the gland to be filled as well as the amount of squeeze needed to create a good seal. Virtually every gland has a slight gap between the two mating surfaces, termed “diametrical clearance.”
Material Considerations
For optimum sealing performance, correct O-ring selection is the direct result of a number of design considerations. These considerations include: size, squeeze, stretch, chemical compatibility, and the ability to resist pressure, temperature, and friction.
Often there are a number of materials that are appropriate for a particular application. Consideration should be given to the full range of environmental and cost factors. Your final selection will usually be a compromise in the sense that you have to balance all of these considerations
The selection of elastomeric material is contingent upon a number of design factors such as: dynamic or static application; chemical compatibility; the O-ring's ability to resist pressure, heat, cold and friction, and consideration of material availability and cost. (In addition to design factors, of course, one must also consider the nature of the installation, the use of the product and the kind and degree of maintenance that may reasonably be expected.)
As an example, silicone is a popular choice of designers and engineers for a wide variety of medical applications. Silicone has a wide temperature range (-94°F to 400°F) with excellent long-term temperature resistance and low temperature flexibility. It offers hydrophobic properties, is biocompatible and inert, and has a neutral odor and taste. In addition, FDA, ISO 10993 or USP Class 6 grades are available.
With such a multiplicity of design factors to consider, it is possible for several O-ring materials to meet, or nearly meet, your specified application requirements. In the case where several O-ring materials meet your requirements, cost and availability may be the deciding factor.
In the case where several materials nearly meet your application requirements, a compromise material selection may have to be made. In such cases, due to the complexity of interacting forces, it is highly recommended that your O-Ring material selection be rigorously tested in the actual application. Performance assumptions must then be checked so that you are certain that all variables have been carefully considered. TMD
If you require assistance for a sealing application, Apple Rubber's Web site has an Engineering Assistance Request form, which can be filled out and e-mailed to the company for more detailed analysis. Visit www.applerubber.com.
Christopher M. Chiodo is a project engineer at Apple Rubber Products, Inc., Lancaster, N.Y. Contact him by phone at 716/684-7649, by fax at 716/685-5509; or e-mail: chrisc@applerubber.com
Explore the July 2005 Issue
Check out more from this issue and find your next story to read.
Latest from Today's Medical Developments
- HERMES AWARD 2025 – Jury nominates three tech innovations
- Vision Engineering’s EVO Cam HALO
- How to Reduce First Article Inspection Creation Time by 70% to 90% with DISCUS Software
- FANUC America launches new robot tutorial website for all
- Murata Machinery USA’s MT1065EX twin-spindle, CNC turning center
- #40 - Lunch & Learn with Fagor Automation
- Kistler offers service for piezoelectric force sensors and measuring chains
- Creaform’s Pro version of Scan-to-CAD Application Module