
The MAXOS multi-axis optical CMM from NVision has its own proprietary patented non-contact probe. It is a point of white light that allows the collection of individual points at a rate of 70 per second. Like a touch probe CMM, it collects individual points, but unlike a conventional CMM it continues on its path at high speed without pausing.
According to the company, the difference between the patented MAXOS sensor and others is that it can scan freshly machined surfaces, highly polished surfaces and even mirrors without any need for them to be sprayed with a coating. Prior to this development, the need for spraying has been the Achilles heel of every optical scanner when challenged with scanning highly polished surfaces, like medical device parts and components. "The MAXOS provides a significantly faster way to measure high-value, precision medical components in an automatic production environment," says Steve Kersen, President of NVision. "Our customers in North America now have access to a medical engineering technology that until recently was only available in Europe and Asia."
The MAXOS employs the conventional three axes of a CMM with two additional axes on its sensor along with two optional turntables, resulting in up to seven axes total. All of these axes can be controlled to ensure smooth and fast movement around all of the points to be measured, even on difficult-to-measure horizontal geometry.
Because the MAXOS measures with a single white light point, the entire cause of inaccuracy and approximation inherent in 3D measurement with a ball probe is eliminated. Consequently, the MAXOS has an exceptionally high accuracy of +/- 2µm on matte surfaces and +/- 10µm on polished metal. It can achieve a point spacing resolution of 0.2µm without pausing. Additionally, since it has no ball probe and measures a single point at a time, it is not limited by ball-offset geometry and can inspect radii of less than 0.2mm.
The MAXOS will create its own alignment for the measurement of a medical part based on an alignment file, after which it will typically measure cross sections and features against predetermined geometry. Consistent with a production environment, MAXOS will provide a complete inspection report at the end of its measuring routine without delay, enabling instant feedback for process control.
According to Giles Gaskell, Director of Business Development at NVision, "Customers typically see productivity improvements well in excess of 400% when compared with the fastest touch probe CMM."
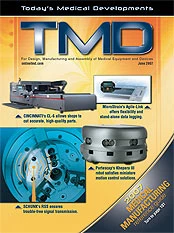
Explore the June 2007 Issue
Check out more from this issue and find your next story to read.
Latest from Today's Medical Developments
- HERMES AWARD 2025 – Jury nominates three tech innovations
- Vision Engineering’s EVO Cam HALO
- How to Reduce First Article Inspection Creation Time by 70% to 90% with DISCUS Software
- FANUC America launches new robot tutorial website for all
- Murata Machinery USA’s MT1065EX twin-spindle, CNC turning center
- #40 - Lunch & Learn with Fagor Automation
- Kistler offers service for piezoelectric force sensors and measuring chains
- Creaform’s Pro version of Scan-to-CAD Application Module