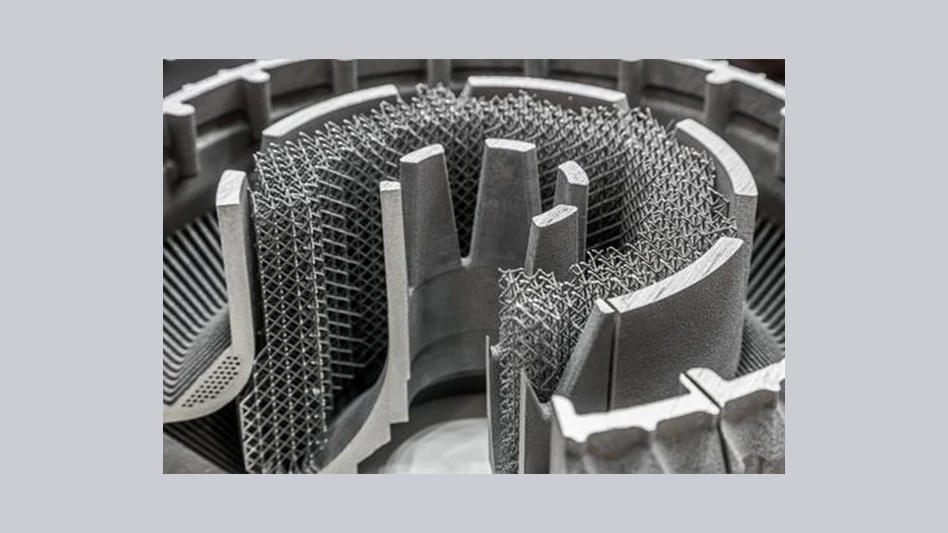
NIST
The U.S. Department of Commerce’s National Institute of Standards and Technology (NIST) has awarded $3.7 million in grants to help address current and future barriers to widespread adoption of metals-based additive manufacturing (AM) through measurement science research.
“The U.S. can take a leading role in developing the measurements and international standards that will help accelerate adoption of these important 3D-printing technologies,” said Under Secretary of Commerce for Standards and Technology and NIST Director Laurie E. Locascio. “To compete globally, we need to invest in programs such as this that bring together our best minds in industry, academia and government to solve important technical challenges.”
AM typically creates parts and components by building them layer by layer, based on a 3D computer model. Most metals-based additive processes form parts by melting or sintering material in powder form.
“Additive manufacturing offers advantages such as reduced material waste, lower energy intensity, reduced time-to-market, and just-in-time production that could bolster supply chains in the U.S.,” said Locascio. “Accelerating the adoption of new measurement methods and standards will help to advance U.S. competitiveness in this important industry.”
Through its own research and with these grants, NIST is addressing barriers to adoption of AM, including measurement science to support equivalence-based qualification and model-based qualification, the characterization of AM materials, and standards to support consistent data exchange/characterizing new advances in AM production systems.
The following organizations will receive NIST Metals-Based Additive Manufacturing Grants Program funding to be spent over two years:
The Research Foundation for the State University of New York (Albany, New York) – $957,706
The goal for this project is to demonstrate an enhanced nondestructive evaluation (NDE) technique that can determine key material properties such as oxide thicknesses, splatter particle percentage, grain size, and defect detection.
Colorado School of Mines (Golden, Colorado) – $956,888
This project will examine new optical metrologies to enable real-time process feedback and control to achieve process-based qualification and certification of metallic parts made by AM.
Auburn University (Auburn, Alabama) – $949,075
The goal of this project is to establish a data-driven framework with computer vision and machine learning for the nondestructive qualification of AM materials and parts for applications that can’t afford failures due to fatigue.
General Electric, GE Research (Niskayuna, New York) – $873,999
GE Research teamed up with GE Additive and the University of Texas at El Paso (UTEP) to establish the Intelligent Stitch Integration for Testing and Evaluation (I-SITE) program to extend existing standardized methods and build correlations between sensor response, material behavior, and mechanical properties.
Latest from Today's Medical Developments
- PhD student helps develop medical device for children with congenital heart defects
- Happy New Year
- Best of 2024: #1 Article – 2024 Forecast
- Best of 2024: #1 News – 6 trends impact medtech in 2024
- Best of 2024: #2 Article – Cybersecurity in medical devices
- Best of 2024: #2 News – Miniaturized, implantable multi-sensors device to monitor vessels health
- Best of 2024: #3 Article – Intech Athens deploys ZOLLER tool management system to control tooling inventory
- Best of 2024: #3 News – Avation Medical raises $22 million+