
3D printing technique using liquid inks and common furnaces is less expensive, faster, and more uniform, says Northwestern University engineering researchers.
Time- and cost-intensive, current 3D printing uses a focused laser or electron beam moving across a bed of metal powder to define an object’s architecture in a single layer, fusing particles together. New powder is placed on the previous layer, and the steps repeat. Any unfused powder is removed, preventing the creation of certain architectures and limiting the types of metals and alloys that can be used.
The new method bypasses the powder bed and energy beam and uncouples the two-step printing and fusing process. An ink made of metal or mixed metal powders, solvents, and an elastomer binder, prints densely packed powder structures using a syringe-extrusion process, dispensing ink through a nozzle at room temperature.
Ramille Shah, an assistant professor of materials science and engineering in the McCormick School of Engineering and of surgery in the Feinberg School of Medicine, explains that the extruded material instantaneously solidifies and fuses with previously extruded material, enabling immediate handling. With collaborator David Dunand, the James N. and Margie M. Krebs professor of materials science and engineering, the team fused the powders by sintering.
The researchers’ 3D inks and process open doors for more sophisticated and uniform architectures that are faster to create and easier to scale up. After the object is printed and before it is heat densified, the structure – a green body – is flexible due to the elastic polymer binder containing unbonded metallic powders.
Medical implants, batteries, solid-oxide fuel cells, and mechanical parts for larger structures could benefit from customized, printed metals.
“We used a biomedical polymer that is commonly used in clinical products, such as sutures,” Shah explains. “When we use it as a binder, it makes green bodies that are very robust despite the fact that they still comprise a majority of powder with very little binder. They’re foldable, bendable, and can be hundreds of layers thick without crumbling.”
Heating the completed green bodies in a furnace where all parts of the structure densify simultaneously leads to more uniform structures that sinter without warping or cracking.
Instead of one laser slowly working its way across a large powder bed, Shah and Dunand’s method can use multiple extrusion nozzles at once, with the potential to 3D print full sheets meters wide that can be folded into large structures.
The process can be used to print metal oxides, such as iron oxide (rust), which can then be reduced into metal. Rust powder is lighter, more stable, less expensive, and safer to handle than pure iron powders. Shah and Dunand’s team discovered they could first 3D print structures with rust and other metallic oxides and then use hydrogen to turn the green bodies into metal before sintering in the furnace.
“It might seem like we are needlessly complicating things by adding a third reduction step where we turn rust into iron,” Dunand says. “But this opens up possibilities for using very cheap oxide powders rather than corresponding expensive metal powders. It’s hard to find something cheaper than rust.”
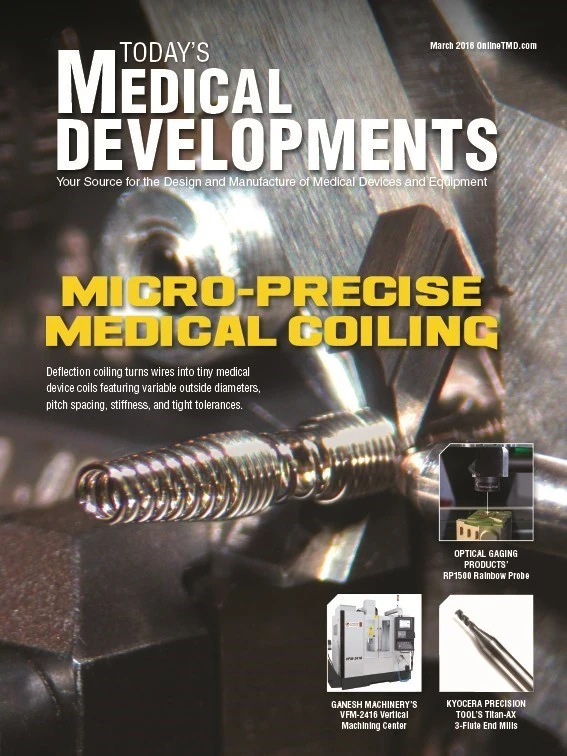
Explore the March 2016 Issue
Check out more from this issue and find your next story to read.
Latest from Today's Medical Developments
- MedTech Innovator welcomes five new industry partners
- First Article Inspection for quality control
- The manufacturing resurgence is here – are you ready?
- Workholding solutions for your business
- ZOLLER events will showcase the company’s cutting-edge innovations
- THINBIT’s MINI GROOVE ‘N TURN Acme threading inserts
- CMMC Roll Out: When Do I Need to Comply? webinar
- Metabolic research uses Siemens gas analyzers to deliver results with 99.9999% resolutions