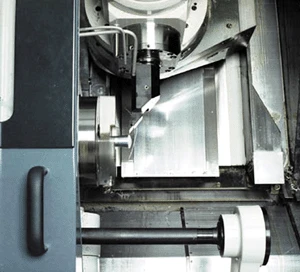
Today, the surgical replacement of a hip or knee joint is a common, though complex, procedure. It begins with the manufacturing of machined implants, made possible by means of new machine tool technologies and materials compatible with the human body. Using advanced multi-tasking machine tools, implants are machined to the close tolerances required for the intricate movement inside the flesh-and-bone machine that is the human leg.
Considered to be one of the innovative leaders in the manufacturing of hip and knee joint replacements, Exactech, Gainesville , FL , produces these joints in an array of sizes to accommodate the wide variation in human anatomy.
According to Exactech's facilities coordinator, Phil Cripe, a hip joint is composed of three to four components. It looks like a ball on a shaft that is tapered at both ends and mates with a one or two-piece hemispherical cup that represents the socket. The highly polished cobalt chrome ball attaches to the shaft using precision tapers.
The knee joint is typically four components made from precision-machined materials as diverse as titanium, cobalt chrome, and high-density polyethylene. Both hip and knee joint forgings require machining processes capable of producing exacting tapers within a 0.0002-in. to 0.0003-in. tolerance.
In order to produce these parts in-house, Exactech began evaluating various machine tools. "Knowing that the hip and knee implants require both turning and milling with precise tolerances, we were looking for the right machine tool with very strong support from the manufacturer," adds Cripe.
According to the company, when comparing machines, it could not find anything competitive with the same capabilities of the Mazak Integrex multi-tasking mill/turn machine.
"As a company, we take technology as far as we can and are creative in using it," comments Cripe. "We felt we had a strong case for integrated processing. So we spent quite a bit of time with applications engineersat Mazak, looking at our product line and the changeovers that we wanted to make on a daily and weekly basis. We found that every cutting operation we wanted was already built into the Integrex. We could produce any type of unique prototype and do it with speed and efficiency."
Upon finding that parts could be machined in one setup on one machine, offering the benefits of reduced labor as well as cost reductions in fixtures and tooling, and an increase in dimensional quality, Exactech purchased two Mazak 200SY Integrex machines. The machines have an advanced turret designed with a 10 hp, 6,000 rpm spindle for live tools to deliver the performance of a machining center. The turret has a 5.5-in. Y-axis movement and a 225° B-axis travel range in increments of 0.001°. These axes increase the machine's cutting capabilities, including crosscut and angular milling, off-center drilling, boring and tapping. With the C-axis capability of the main spindle, precision contouring can also be performed.
With its 10 hp secondary spindle for heavy-duty machining, the Integrex can fully complete a part without operator interruption. It automatically transfers the workpiece from the first spindle to the second spindle to complete both ends of a turned part.
In addition, Renishaw Model 10 probes are used on the Integrexes to check final part tolerances and speed up quality checks. To prove process capability of the probes, Exactech uses a CMM to randomly check parts.
To further improve its capabilities, the company has an Intranet system to download part programs produced from their CAD/CAM systems to the machining centers. The Intranet also links the Mazatrol 640 PC-Fusion-CNC controls of each machine tool together. By using an ordinary PC linked to Mazak's fusion control, Exactech gets information on the status of each machine, such as production status and count, tool-data management, simulator for scheduling, and operation condition monitoring.

Explore the November 2005 Issue
Check out more from this issue and find your next story to read.
Latest from Today's Medical Developments
- HERMES AWARD 2025 – Jury nominates three tech innovations
- Vision Engineering’s EVO Cam HALO
- How to Reduce First Article Inspection Creation Time by 70% to 90% with DISCUS Software
- FANUC America launches new robot tutorial website for all
- Murata Machinery USA’s MT1065EX twin-spindle, CNC turning center
- #40 - Lunch & Learn with Fagor Automation
- Kistler offers service for piezoelectric force sensors and measuring chains
- Creaform’s Pro version of Scan-to-CAD Application Module