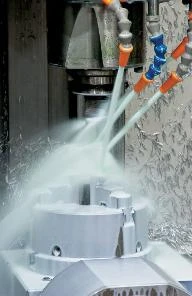
Even in the medical manufacturing industry, every second of production time can make the difference between profit and loss. Every tool change and every time the part has to be handled increases cycle time and can impact accuracy and repeatability. The managers at MarLee Manufacturing, a contract manufacturer of medical parts located in Ontario, California, determined that by outfitting nine of their 17 Fadal VMCs with rotary tables, they could realize an enormous productivity gain and improve repeatability for a nominal investment. In fact, the company was able to reduce cycle time by 80% and more when machining stainless steel and aluminum parts to tolerances of 0.0005.
Since its first rotary table was purchased, mill department supervisors at MarLee have accumulated substantial experience in maximizing productivity. Early on, the managers learned that automating positioning of parts is only one of many such timesaving benefits as fewer tool changes and workpiece handling. This enables tighter tolerances, better repeatability without slowing production.
A good example of the cycle timesavings realized by MarLee is a medical instrument bracket for an Xaxis encoder, which is machined from an aluminum casting. The part required one setup and nine part handlings before it was setup on a rotary table. The cycle time was 70minutes. When the part was setup on a rotary table, only one part handling was required. This has reduced cycle time from 70 to 10 minutes.
We machine more surface area in less time with the rotary table, says Todd Nutter, mill department supervisor. Weve eliminated operator errors, such as missed operations and inconsistent finishes. Were achieving tighter tolerances and better repeatability with less scrap.
MarLees VMC is setup with a fixture on one side of the table and a rotary table on the other side. First, the Xaxis encoder bracket casting is mounted in the fixture for machining on the backside of the part and for drilling two blind mounting holes. Using a vice, the casting is mounted to the rotary table and one side is machined to complete a step and groove operation. The rotary table rotates the part to the opposite side, which is machined and another step and groove operation completed. The same tool is used on all sides of the part before the next tool is loaded, eliminating nine changes per tool.
Aaxis mapping, sometimes called CAM Wrapping, is a feature of the Fadal control that makes it easier and faster to program grooves and screw holes. It accomplishes this by enabling the control to wrap a flat XY program around a cylinder. All the Yaxis motion is translated into Aaxis motion. The Aaxis rotates a predetermined amount according to the Yaxis distance traveled in the original flat XY program. It translates both linear and circular interpolated moves and rapid pointtopoint moves. Aaxis mapping reduces programming time, even when compared to offline CAM programming systems.
According to Andre Rouzon, mill department supervisor, not all rotary tables are alike. For example, rotary tables move at different speeds. Those with faster RPMs move parts into position much faster, which minimizes the time spent cutting air. Another consideration is accuracy, which is measured in arc/seconds (1/3600th of a degree). The ability to easily program a rotary table either with offline CAM software or with the machines control provides flexibility. Control features, such as
Aaxis mapping and engraving are hidden timesavers, which may not be apparent until actually used. The single most important capability of the rotary table is the ability to automatically position the work piece so that multiple sides of a part can be machined with only one manual handling of the part, reducing errors and increasing accuracy.
Pallet changers provide process flexibility. Pallet changers are often linked to high volume runs. However, pallet changers dramatically reduce teardown and setup time. Multiple pallets can be set up with rotary tables, dedicated fixtures and vices. When a critically time job comes through, rather than tear down a complete setup, the pallet can be exchanged. This allows high productivity rates to be maintained. Pallet changers enable machining operations in kits, batches and progressives. The objective is to keep the tool on the work piece as much as possible, stopping to change pallets. A Fadal pallet changer is factory set to change in 16 seconds and can be reset by the operator to as low as 10 seconds.
Fadal rotary tables used in conjunction with Fadal controls deliver fullyinterpolated 4axis machining or indexing. Additionally, Fadal rotary tables provide a cabling system that enables them to be automatically shuttled in and out of the VMC without attaching and detaching cabling. This allows unattended pallet changes for lightsout operations. Another technique for increasing productivity can be achieved by mounting a tombstone on a rotary table, enabling parts to be mounted on each side of the tombstone.
Knowing your tools is the key to productivity. And knowing how to use a rotary table can provide a substantial increase in productivity through positioning and 4axis machining of parts. Extra setups and handling, special fixtures and tool changes are eliminated. Cycle time and handling for any part that requires machining on more than one side can be reduced from 10 to 30 percent or more with the use of a rotary table. All you need to do is make the proper application.

Explore the May 2005 Issue
Check out more from this issue and find your next story to read.
Latest from Today's Medical Developments
- Tariffs threaten small business growth, increase costs across industries
- Feed your brain on your lunch break at our upcoming Lunch + Learn!
- Robotics action plan for Europe
- Maximize your First Article Inspection efficiency and accuracy
- UPM Additive rebrands to UPM Advanced
- Master Bond’s LED415DC90Med dual-curable adhesive
- Minalex celebrates 60 years of excellence in miniature aluminum extrusions
- Tormach’s Chip Conveyor Kit for the 1500MX CNC Mill