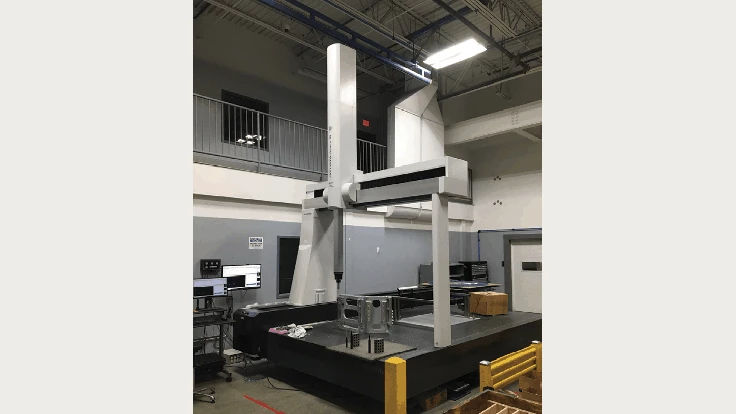
MItutoyo/Schleifring

It’s an 800 lb beast, a massive component with seven uniquely machined features. It arrives at Schleifring Medical Systems’ Elgin, Illinois, shop partially assembled, making it nearly impossible to get inside to measure for accuracy and range.
Operators had to use a crane to manually flip the component in multiple directions to measure all critical features and obtain the required dimensions. Not only did this slow the production process, it posed a significant safety concern for workers. Schleifring sought an alternate solution that would save time, streamline the process, ensure quality, and make production easier for its operators.
Industry partners
Schleifring considered portable measuring arms, laser applications, and bridge-type coordinate measuring machines (CMMs). Due to the part’s tolerancing, the company determined that a portable measuring arm wouldn’t be accurate enough or have the reach to meet requirements. And while laser measuring systems would have increased accuracy compared to portable measuring arms, the high cost of laser applications at the time made this option prohibitive.
In the end, Schleifring opted for a CMM as the best solution. In weighing its options, top criteria considered included:
Size: The CMM needed to fit within company parameters, a large-part manufacturer, not a high-volume manufacturer
Safety: Chosen machine would have to accommodate measurement without moving the part
Location: Machine would need to fit within a specific location inside the facility that would make it easy to service
Mitutoyo America Corp. worked with Eric Baumler and Ryan Losacco, members of the Assurance Technologies Inc. sales team, who already had a longstanding relationship with Schleifring. After comparisons, the company chose to purchase the Mitutoyo Crysta-Apex S2030-16 CMM. The company found that no other machine would be large enough or fast enough to reach required distances or provide the accuracy and repeatability needed per part. An added bonus was that, due to the CMM’s integrated temperature probe, installation, and housing, it didn’t have to be limited to a closed-off, temperature-controlled environment.
Results
Since implementing the CMM, Schleifring part inspection time has fallen from 45-to-60 minutes across two different setups to 25 minutes using one setup (no flipping), reducing inspection time up to 58% and alleviating final inspection bottlenecks.
With the aid of custom fixturing created by the Mitutoyo Custom Solutions Group, it can handle 4,000kg of parts, and operators no longer have to manually adjust an 800 lb product. Operators can perform difficult measurement processes more safely and easily, and parts can be fully assembled and tested for final critical features.
The company also realized an unexpected but welcome benefit: more information available. With the embedded statistical MeasurLink software, operators can easily see high and low points, resulting in a physical representation of where issues exist that was not possible with the old equipment. Another unexpected benefit, at least for Schleifring, is that Mitutoyo is practically in its backyard.
“In terms of getting up to speed on the new machine, as a small company we don’t always have time to devote to learning the nuances, tips, and tricks of operation,” says Cathi Kirchner, Schleifring quality manager. “Being able to have Mitutoyo field service technicians come onsite to answer questions or give little primers has been a great help.”
Advice Schleifring would give other organizations looking to make a switch and invest in a large-capacity CMM, they stress the importance of training. Make sure the CMM manufacturer offers comprehensive training – onsite and virtual – and that employees take advantage of it on an ongoing basis. Also, make sure the CMM can measure anything – small, medium, large parts – so one investment can cover an array of future products.
“The machine takes up a lot of real estate,” Kirchner notes. “Make sure you have room for it somewhere. And be sure to get production buy-in early to make the transition installation as seamless as possible.”
Mitutoyo
https://www.mitutoyo.com
Schleifring Medical Systems
https://www.schleifringmedical.com
Assurance Technologies Inc.
https://www.atiquality.com


Explore the May 2020 Issue
Check out more from this issue and find your next story to read.
Latest from Today's Medical Developments
- How to Reduce First Article Inspection Creation Time by 70% to 90% with DISCUS Software
- FANUC America launches new robot tutorial website for all
- Murata Machinery USA’s MT1065EX twin-spindle, CNC turning center
- #40 - Lunch & Learn with Fagor Automation
- Kistler offers service for piezoelectric force sensors and measuring chains
- Creaform’s Pro version of Scan-to-CAD Application Module
- Humanoid robots to become the next US-China battleground
- Air Turbine Technology’s Air Turbine Spindles 601 Series