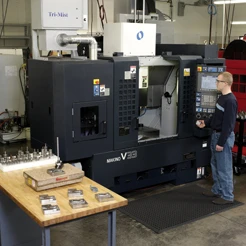
Since 1978, Mold-Tech has been building plastic injection molds for the medical, automotive, packaging, electronics and consumer industries. They also design and build custom tooling and automation for the molding industry. "Mold-Tech is continuously changing; we are always trying to make a better process for our clients," says Jon Lee, vice-president of Mold-Tech. "We keep advancing, so we always stay ahead." In 1999, Mold- Tech became ISO 9001 certified, which, according to Lee, has helped with improving processes, and getting standards and procedures established for consistency.
Acquiring the latest technology has helped Mold-Tech to expand the company. They are working out of a new 12,000 square-foot facility, with double the manufacturing and engineering space of their old plant. And, they are poised to accommodate future growth.
Recently, Mold-Tech was looking to add even more capability. They turned to Makino to help them achieve their goals, knowing the past success with Makino machines. "Mold-Tech's general manager Pete Parks and I went to our Makino distributor, Productivity, Inc.," says Lee. "We visited with some of the Makino application engineers- showing them our part, and Makino immediately did test cuts for us on their V33 high-speed, CNC vertical machining center." Mold-Tech had the V33 installed on their floor and started cutting parts in less than two days.
This wasn't the first Makino machine that Mold-Tech had purchased; they also own an EDNC43 and an EDGE2, both Ram EDM machines, and a Makino SNC64 high-speed graphite milling machine. "Purchasing the first Makino EDNC43 Ram EDM machine in 1994 was one of the most important decisions we've made," says Lee. "Before that, we had other brands of machines in our shop. We ran three of them with three operators. But, we got rid of those three machines and three operators and replaced them with one Makino EDNC43 Ram EDM machine and one part-time operator— and we did double the work."
Many of the parts Mold-Tech cuts on the V33 have been micro-devices for the medical industry. The company wanted to achieve better surface finishes on their molds, eliminating the need for polishing details that were too small for bench work, while improving overall cycle times. "We are eliminating the EDMing and the polishing. We are cutting right to finish sizes, with accuracies to two-ten thousandths or less. Parts come out that do not need polishing," says Lee. The improved finishes translate into shorter lead times, making Mold-Tech more competitive.
"The biggest thing that the V33 has done for Mold-Tech is open up a whole new realm of possibilities—they're doing things that before, they had not been able to do. "I know now that I can go in and machine certain parts, whereas before I would have to plan on making electrodes and burning them; now I can machine something to four-thousandths radius. I don't have to make electrodes. Furthermore, I can machine without polishing," states Lee. Eliminating processes has had a big impact on the company, reducing costs and lead times. In the past, typical lead times were 8-12 weeks. Mold-Tech has been able to cut that down to 6-8 weeks.
To ensure success, Lee says that Mold- Tech has several criteria they follow when purchasing equipment: 1) What is the capability of the specific machine tool—is it going to be able to do what we want? 2) How quickly can we see return on investment? 3) Who is selling the machine—what kind of support are we going to get if things don't work right? "In general, it was easy for us to see the return on investment with the V33 because it did exactly what we wanted it to do. It allowed us to change our processes and reduce time on the job," says Lee.
"Within the last year or so, we feel that the cutting tools, software and machine tooling have all come together and we've been able to go where we wanted to, says Lee. "We feel, at this point, we are only scratching the surface of the Makino machining capabilities. We are still learning how far we can take it."
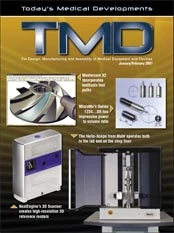
Explore the January February 2007 Issue
Check out more from this issue and find your next story to read.
Latest from Today's Medical Developments
- The role of robotics in precision medical device manufacturing
- Swiss Steel Group’s UGIMA-X machinable stainless-steel sets
- #51 - Manufacturing Matters - The Impact of M&A in MedTech 2024
- Visual Components: 25 years of simulation and programming software innovation
- Zimmer Biomet announces definitive agreement to Acquire Paragon 28
- Discover an innovative technology for EMI/ESD/TVS suppression
- Teleflex to acquire BIOTRONIK’s Vascular Intervention business
- Innovation at Global Industrie 2025