
Rigid, high-efficiency integrated mill-turn center
Combining 5-axis simultaneous machining and turning with up to 12,000rpm, the NTX 1000 2nd Generation efficiently machines complex workpieces with high precision and can be installed with automation solutions.
With a 12.4m² footprint including a chip conveyor, the NTX 1000 2nd Generation’s design ensures a sufficient machining space, enabling simultaneous machining with the tool spindle. The compact tool spindle and turret 2 allow a flexible tool layout that avoids interference with tools and fixtures.
Cooling oil circulates inside the ballscrew, ball nut, and spindle to minimize heat and resist environmental temperature variation, ensuring stable, high-precision machining. Turret 2’s built-in motor turret (BMT) minimizes heat generation and vibration, improves milling precision and performance, and increases production capacity.
The NTX 1000 2nd Generation is compatible with automation solutions with a bar feeder and an in-machine traveling robot to handle workpieces. The operator can control the robot and check the operation status using the NC unit as if it were a part of machine operation. DMG MORI has equipped the app-based control and operating system CELOS using an intuitive and ergonomic touch panel.
DMG MORI
https://us.dmgmori.com

Integrated robotic machine loading system with secondary operations
The Nagel RL-2000 robotic load/unload system can perform secondary operations to support lights-out manufacturing. Ethernet and Profinet communications inside the Fanuc controller eliminate the need for expensive standalone controls. The system can be integrated into new or existing CNC- and PLC-based machines.
Configurable for front- or side-loading, operators open the interlocked safety door to manually unload up to four finished trays and load green trays. Following production, the robot will push trays, mounted on heavy- duty rails that pull out like drawers, back in and pull the next one out. Sensors ensure trays are in place to prevent crashes. The robot can periodically drop a finished part into an SPC chute for off-line inspection. The robot can also be equipped with automatic gripper changers for rapid changeover.
Nagel Precision Inc.
https://www.nagelusa.com

PVD-coated carbide inserts
ST4, a super tough PVD coated carbide grade with a thick CrAlN coating, extends tool life by providing high hardness and oxidation resistance, solving issues related to machining materials such as: 304SS, 17-4PH, and Nitinol. High-speed machining applications with ST4 inserts have proven results with stable machining, excellent surface finishes, and extended tool life.
For front-turning there are the YL, CL, AM3 on positive inserts and UL, ZP on negative inserts. Other inserts support back-turning (BM); grooving (GX); cut-off (CX, TH); and ID turning (FG, F1, F05 direct chip evacuation in blind holes).
NTK Cutting Tools USA
http://www.ntkcuttingtools.com
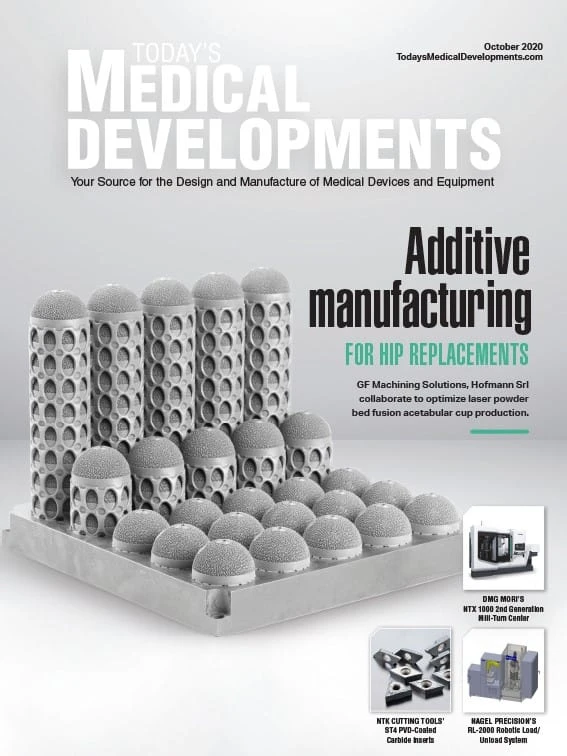
Explore the October 2020 Issue
Check out more from this issue and find your next story to read.
Latest from Today's Medical Developments
- MedTech Innovator welcomes five new industry partners
- First Article Inspection for quality control
- The manufacturing resurgence is here – are you ready?
- Workholding solutions for your business
- ZOLLER events will showcase the company’s cutting-edge innovations
- THINBIT’s MINI GROOVE ‘N TURN Acme threading inserts
- CMMC Roll Out: When Do I Need to Comply? webinar
- Metabolic research uses Siemens gas analyzers to deliver results with 99.9999% resolutions