
The deflection coiling process relies on the theory of elasticity and plasticity to produce helical springs of all types and forms. These fundamental principles make it possible to form wires as small as 0.0008" in diameter made of materials such as platinum, stainless steel, and tungsten into tiny medical device coils with outside diameters as small as 0.006". Due to their broad range of use, medical device coils typically have many stringent attributes pertaining to coil geometry, coil stiffness, and functional tolerances.
The deflection coiling process affords users the ability to produce coils in round and flat wires with variable outside diameters, variable coil pitch spacing, variable coil stiffness, and tight tolerances at nearly unlimited lengths. Kinecoil, Division of Kinefac Corp., provides multi-axis servo-controlled Micro-Coiler equipment, which transforms the theory into practice with superior process control.
Theory
Hooke’s Law states that when a load is applied to a deformable material it first begins to deflect within its elastic range. While in that elastic range, if the load is released, the deflection is nearly recovered. However, if the load is at a level such that the stresses imparted exceed the yielding stress of the material, then plastic deformation and permanent set will occur. This very behavior governs the functional mechanism by which deflection coiling is possible.
When forming a straight wire into a round coil, it is necessary to apply enough load to deflect the wire into an arc, which is slightly smaller than the final coil diameter. Bending the wire into a smaller arc counteracts residual stresses by allowing the material to elastically spring back into the final coil size. This phenomenon occurs when the coiling load is released as the wire leaves the coiling tooling. The Micro-Coiler mimics this behavior by precisely deflecting the wire around an arbor tool that is smaller in diameter than the final coil inside diameter.

Materials
The most popular coiling materials for the medical device industry are 304V and MP35N stainless steels, platinum alloys, palladium alloys, and tungsten. There are many attributes of these materials such as non-galvanic properties, radiopacity, and high strength, which make them suitable for use inside the human body. The tensile strength of these materials before coiling can range from 180,000psi to 200,000psi for platinum alloys, and up to as high as 350,000psi to 400,000psi for stainless steels and tungsten.
Due to the range in tensile strengths, the sizing of the coiling arbor tool is critical because of the differing spring-back behavior between materials. The arbor size required to produce the same coil in a 304V stainless steel versus a platinum alloy will be different. In any forming process where some amount of elastic recovery governs final product size, the quality and consistency of the incoming material and its properties are critical.
Softer materials in the lower tensile ranges can be challenging to coil depending on how well the wire can be supported and controlled during coiling. The Micro-Coiler supports and guides the wire in precision micro-align tooling while applying precise feed-roll pressure to accurately form the wire into coils.
Coiling diameter tolerances
Coil index is a good indicator of coiling difficulty and the manufacturing tolerances that might be achievable. Index is a ratio of coil diameter to wire diameter and is calculated by subtracting the wire diameter from the coil diameter, and dividing by the wire diameter.
Index values as small as three are possible with deflection coiling. The most typical medical device coil index range is between four and seven. Smaller indexes are more difficult to form as they require a tighter bending radius and higher forces to produce. Indexes higher than 10 are easier to form because they require lower coiling forces but become increasingly more difficult to control.
On a Kinecoil 4-axis servo-controlled CNC Micro-Coiler, the typical coil diameter tolerances for coiling indexes between three and five is ±0.0002", and ±0.0003" for indexes between five and 10. Beyond an index of 10, diameter tolerances can be held in the range of ±0.0005". These values assume good quality coiling material.
Stiffness
Coil stiffness is often an important requirement for medical device coils. Delicate veins and arteries could be damaged by a coil that is too stiff. Conversely, a coil not stiff enough could collapse or fold under the same conditions. The coil back-tension and/or spacing between coils (coil pitch) controls the coil stiffness. Adjusting the coil back-tension can result in producing a coil with no visible pitch but with more or less stiffness. For a given coil, the maximum amount of possible back tension is limited by the coil index and material properties.
The Kinecoil Micro-Coiler achieves back-tension and coil pitch spacing by precise servo positioning of a pitch tool and precision lateral adjustment of the coiling point tool. Actuating the pitch tool against or away from the forming coil can induce or reduce back-tension and coil pitch. When the actuation is not enough to induce visible pitch change, the coil stiffness will be affected.
To characterize coil stiffness, a droop test is often used. A coil is cantilevered out horizontally at some raised height until it droops down to touch the original surface. The amount of horizontal distance the coil extends to droop down to the original surface characterizes the coil stiffness.
Pitch spacing, tolerances
Many medical device coils such as guidewires require open pitch spacing for various reasons. Windows are often needed for visual inspections, insertion of other tools or devices, or even post-processing such as welding. The Micro-Coiler achieves coil pitch spacing through the precise servo positioning of the pitch tool and lateral positioning of the coiling point tool.

Pitch spacing tolerances also vary with coil index. On the coiler, the pitch spacing tolerance that can be held for coil indexes between three and five are typically ±0.0002"; ±0.0005" for indexes between five and 10, assuming good quality wire.
There are some challenges to coil pitch spacing, which the coiler is designed to overcome. As pitch is induced between coils, the formed coil diameter in the pitched area can be affected. Coils with varying pitch sections can be a problem without making coil diameter adjustments. The Micro-Coiler can be easily programmed to compensate for any slight diameter changes that may occur in pitched sections.
Coil straightness can also be an issue when there is a significant transition from closed to open pitches or vice versa. The machine can be programmed to improve coil straightness when transitioning between open and closed pitch sections of a coil.
Since coil pitch spacing is often defining a window for visual access, pitch tolerances should be maximized for manufacturing.

Diameters
Deflection coiling makes it possible to have multiple or varying outside diameters within a coil. Variable diameters can have many purposes, including tapered lead-ins for insertion or guiding, or even to significantly change the coil stiffness in one particular area.
The Kinecoil Micro-Coiler servo controlled diameter axis precisely controls coiling point tool position on the fly and can be programmed for a variety of diameter changes within a coil. Coil diameters can be programmed concentric or offset with respect to other diameters on the same coil.
The smallest diameter within a multi or variable diameter coil governs the size of the arbor tool. Significant increases in coil diameter can become an issue using the same arbor, because as the coiling point tool moves further away to increase the coil diameter, the control and stability of the wire diminishes, which can affect achievable tolerances.
Length and tolerances
Coil length is limited by the length of the outboard coil support system. Kinecoil designs and builds custom and standard coil support units of various lengths which can be programmed with a dump function for continuous coil production. Support of the coil is critical as coils increase in length. An improperly supported coil can generate excessive loads or vibrations that can affect coil quality or dimensional variation.
When coils reach the desired payout length from the Micro-Coiler, a servo controlled cutter tool cleanly shears off the coils at the arbor.
Coil length can be achieved by programming a discreet amount of wire-feed length or by allowing the machine to payout coil to a sensor. Coil length variation is typically ±0.010" when using a length sensor.

Speed
The rate at which coils are formed is controlled by the wire feed rate. The feed-roll axis in the Micro-Coiler is servo controlled and programmable for various speeds and precise wire feed.
Coil stiffness, index, material, length, geometry, and support systems all influence the speed at which coils can be made with reasonable control. Stiffer, more stable coils with appropriate support systems are typically run at faster wire feed rates in the range of 300ipm to 1,000ipm or more. Coils which are not as stiff such as those of larger index or of softer materials such as platinum are typically run at slower wire feed rates in the range of 100ipm to 300ipm. Coiling speeds can be adjusted as coil length increases to maintain quality and control. The system can feed wire up to 2,500ipm.
Kinecoil, Division of Kinefac Corp.
About the author: David C. Willens,research and process development mechanical engineer at Kinecoil, Division of Kinefac Corp., can be reached at 508.754.6891 or kinecoil@kinefac.com.
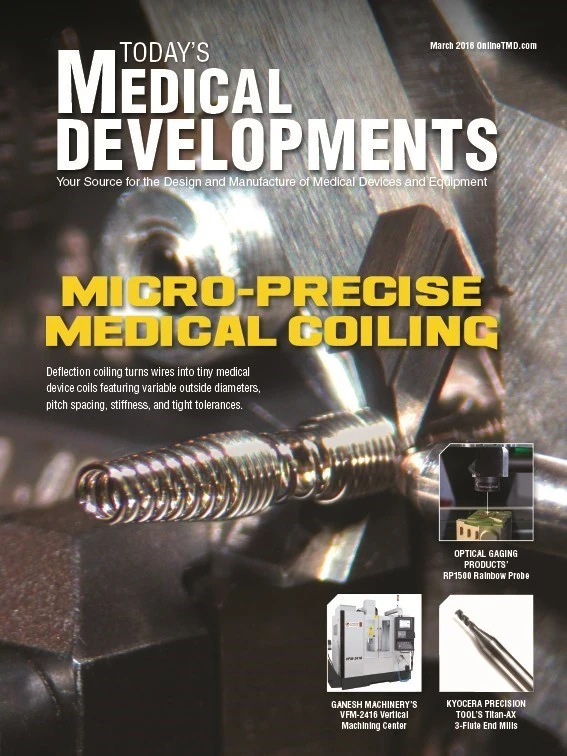
Explore the March 2016 Issue
Check out more from this issue and find your next story to read.
Latest from Today's Medical Developments
- MedTech Innovator welcomes five new industry partners
- First Article Inspection for quality control
- The manufacturing resurgence is here – are you ready?
- Workholding solutions for your business
- ZOLLER events will showcase the company’s cutting-edge innovations
- THINBIT’s MINI GROOVE ‘N TURN Acme threading inserts
- CMMC Roll Out: When Do I Need to Comply? webinar
- Metabolic research uses Siemens gas analyzers to deliver results with 99.9999% resolutions