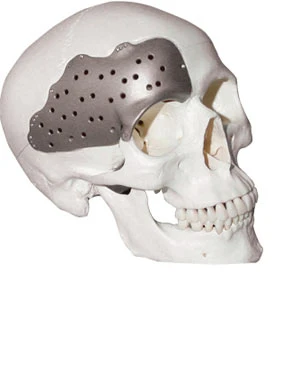
A lot of people can do without a car if need be, but not without the healing process. More money is earned worldwide through the development of critical medical technology than in the entire automotive industry; the healthy growth in this industry owes a lot to machine tools from Germany.
With more than 4 million people currently working in healthcare in Germany, making 240 billion Euros each year, medical technology is even more successful than the auto industry. Therefore, metalworking trade fairs attract visitors from the medical engineering industry. The Institut für Mikrotechnik Mainz (IMM) GmbH was recently at one of these. A glance at the business card of Dipl.-Ing. (TU) Frank Neumann shows his affinity for metalcutting. Neumann is head of the IMM Department for Precision Engineering. "We founded an EDM Competence Center at the end of 2007, established erosive lathing as a new method and brought this onto the market together with Mitsubishi Electric," Neumann explains.
Erosive lathing is used for microstructuring below one micrometer.
This Mainz, Germany-based company claims to have achieved a new world standard for surface roughness of 20µm by means of erosion. This technology is used by customers to manufacture pins for hardness tests, for example pins that determine the Shore hardness of plastics.
The penetration pins used have special tip geometries in the range from 10µm to 150µm, and a maximum contour deviation of ±1µm.
"The manufacturing process for such products has been greatly simplified. We are now working on generally eliminating polishing and grinding in microprocessing," Neumann says.
A device to remove tissue samples directly from the liver was developed as a medical technology highlight by means of lathing, milling and erosion.
A type of "mechanical gun" shoots a hollow, wafer-thin needle into the liver at twice the gravitational acceleration and a force of 800 Newtons, which then removes the sample in a completely sterile and protected manner.
The sample is then placed on an object slide in the device. A brain probe that locates and scleroses diseased parts of the brain using sensor technology is in a different medical evaluation phase.
This technology may be able to heal patients suffering from Parkinson's disease.
The probe measures only 0.5mm x 0.5mm, including the electronics. It is manufactured by cavity sinking and wire EDM as well as microassembly, with accuracy less than 1µm.
MEDICAL GROWTH
Stama Maschinenfabrik GmbH from Schlierbach, Germany, with U.S. headquarters in Itasca, IL, also presented its medical technology. The Managing Director, Dr.-Ing. Achim Feinauer, explains why: "Our motivation is the constantly growing medical market in which Stama has been active for the past 10 years. What actually got us going was complete turnkey machining." The medical technology industry manufactures implants, instruments and device parts from materials that are quite hard to machine, such as titanium, using milling-turning centers and vertical machining centers from the company. This is carried out directly from blank bars by turning and milling in a single operation. In this way, Stama has been able to establish extensive knowledge and experience in all aspects of medical technology.
More than 50 Stama milling-turning centers are currently in use at IMM, primarily in the production of implants and devices. The special team involved in devising manufacturing solutions for medical technology is comprised of specially-trained sales engineers who feel quite at home in the world of medical technology. Feinauer says, "Take a spine implant, as an example, which is produced in a process chain that has to be approved by a government authority. The processes and thus the machines must work very reliably because Stama customers must also manufacture and deliver spine implants within 24 hours if necessary." The turning-milling centers from Stama, according to the company, have been proven to have a high availability of 98%. Users can thank not only the machine tool, but also the programmers and operators for this high figure. "It usually takes six to nine months before the productivity of the machine, with its 12 axes, is fully utilized," Feinauer explains.
But the design engineer of the medical products also plays an important role in the product development process.
He is given a completely new level of freedom in design engineering, thanks to the random combination of turning and milling operations on all six sides, and to the machine's ability to manufacture products in one fixture in a short time with a much higher quality.
Demanding users in medical technology are given two separate travelling columns on a common base frame in the Stama milling-turning center, an MC 726/MT-2C. Each travelling column has a sturdy milling spindle and its own tool magazine with a maximum of 64 positions. They work together with a turning spindle on five axes in the work area. The machine has two independent work areas, each with a milling and turning spindle that allows parallel processing of workpieces to double the productivity of the machine.
Gühring oHG from Albstadt is among the world's leading suppliers of tools for rotational metalcutting. The current range of products covers a total of more than 1,620 different tool types with more than 44,000 different catalog items. These include special surgical tools for hip, knee and foot operations. The tools are generally manufactured directly on the basis of customer designs in a very complex manufacturing process. Johann Wessner, production manager for Special Tools remarks, "These are normally very complex multi-level or graduated tools with several cutting edges and extraction devices."
A CLASS HIGHER
Products of stainless and acid-resistant steels are among the special tools for this expanding industry. The art of these tools is a balancing act between a very high corrosion resistance and a decent temperability. The high tolerances in the micrometer range, which are otherwise decisive in high-precision machining, take a back seat in the medical field. "We can literally operate a tolerance class higher in the range of three to four hundredths of a millimeter," Wessner explains.
Processing of the tools proves more critical because the manufacturer may under no circumstances exceed certain temperatures. This could otherwise lead to a change in the microstructure and deterioration of the corrosion resistance.
Gühring also processes tools by special methods such as high-speed grinding since softer materials tend to form a special type of burr. Demands on finishing are also made by the hygienic design. "The surfaces must be reworked so that they can be easily cleaned and sterilized. The pores must be extremely small," Wessner states.
The new AllGrip tool clamping system from the LMT Company, Bilz Werkzeugfabrik GmbH & Co. KG in Ostfildern, Germany, is suitable for use in medical technology. This shrink-fit chuck reliably holds tapered milling tools at very high speeds, ensuring a very high concentricity of less than 5µm. Prof. Dr.-Ing. Diethard Thomas, head of the LMT Academy at Fette GmbH in Schwarzenbek, Germany observes, "There are some tools whose shafts are in a rougher tolerance class. LMT Bilz has now come up with a shrink-fit chuck for these tools that also ensures a precise concentricity with excellent damping properties." The notches in the shrink-fit chuck make it elastic so that it compensates the irregularities of cheaper milling tools with larger tolerances. The All- Grip system holds tools of a shaft diameter of three millimeters, and also the micro-millers that are popular in medical technology. The demands on micro-milling are high, with pitches of the wafer-thin tools starting from one micrometer.
STAMA AMERICA
Itasca, IL
stama-america.com

Explore the July 2009 Issue
Check out more from this issue and find your next story to read.
Latest from Today's Medical Developments
- Global Industrie - A meeting to understand, anticipate and contribute to the industry of tomorrow
- Wintriss’ Tracker Hardware Solution for ShopFloorConnect Production Tracking Software
- Protolabs expands end-to-end manufacturing capabilities
- Sunnen’s HTE-1600W Tube Hone
- Researchers invent soft, bioelectronic sensor implant
- HEULE’s DL2 tooling
- Application Park shows off diverse robotics applications
- Join our editors for a look at the manufacturing industry in 2025