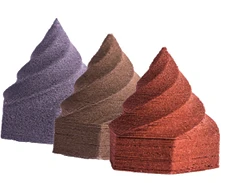
The Virtual Foundry

For polymer and composite additive manufacturing (AM), users have had two primary options – powder-bed systems that use heat to melt powdered material into shape, or filament-based systems that melt the edge of a thin polymer wire and stack the melted layers on top of each other.
With metal AM, systems such as selective laser melting (SLM) laser cusing, and direct metal laser sintering (DMLS) dominate because of a lack of usable filaments. Stoughton, Wisconsin-based The Virtual Foundry (TVF) is changing that, offering metal filaments that can be used on the same equipment designed for polymer AM.
TVF has been working with a range of manufacturers, testing its trademarked printing filament – Filamet – to gage suitability, and expand AM applications while lowering costs. Company executives recently spoke to GIE Media editors about the state of AM and how they are disrupting the market.
Direct metal printing
Unlike traditional metal AM technologies, such as selective laser sintering (SLS) or powder bed fusion (PBF), TVF’s direct-metal printing (DMP) technology does not generate a finished part out of the printer. Filamet – produced in widths of 1.75mm or 2.85mm – is a mixture of plastic pellets (the binder) with a metal powder. It’s similar to a green gear or other powdered-metal (PM) part that must undergo furnace sintering to harden.
As the printed parts heat up, and before sintering fuses the particles together into a solid whole, the binder material evaporates. Because Filamet is encased in the binder, it doesn’t require respirators, solvents, specialty chemicals, or special handling equipment, just heat, making it safer than existing laser-based metal 3D printing solutions.
Technology inventor and company founder Brad Woods says the two-step process of printing then heat-treating hasn’t been as much as a deterrent as he feared when he developed the technology. At the time, he was concerned that industrial users would stick to costly systems that could produce finished parts.
“I expected people who had access to this technology were satisfied, but they weren’t,” Woods says. He adds that aerospace defense giant Lockheed Martin was the first to test the system, “and they were very interested in this even though they had access to all SLS machines, as much as they wanted.”
Even with the furnace step, filament-based printing tends to be faster and requires less specialized training, making AM technologies more accessible to manufacturers who don’t have large numbers of specialists.
Also, because Filamet works in small desktop machines up to the massive filament-based systems that can produce entire car bodies, the technology offers larger build envelopes than otherwise available with metal AM.

Low-volume manufacturing
Most companies experimenting with TVF’s Filamet have been doing so on a small scale – testing individual parts or using the technology as a design tool rather than a production method. Woods says he expects that to be the case for some time.
“At this point, they’re looking for methods to manufacture intricate parts – multiple component parts – and they are unable to make the entire piece subtractively,” Woods says. “In aerospace stators and rotors for example, manufacturers are working to combine elements, consolidate as many features as possible, and 3D-fabricate fins.”

TVF’s President, Tricia Suess, adds that major manufacturers have billions of dollars invested in traditional manufacturing technologies that work well, so AM will be in more of a design/support role for some time.
“The technology is advancing but won’t replace mass production today. That’s not what we’re focused on,” Suess says. “3D printing is shining in engineering and prototype shops.”
Specialty AM applications could also be a growth area. Suess notes that several companies have discussed custom filament materials for low-volume, oddball products that are hard to produce economically.
Industry interest
TVF also has tungsten and copper filaments in its repertoire, with both providing radiation shielding while still in a green state. An early test sample with the tungsten showed great radiation shielding properties while being lightweight, Suess notes. This development had the team thinking about other applications, and by the end of February 2019, TVF signed a joint venture (JV) with Vulcan Global Manufacturing Solutions for tungsten Filamet’s use in radiation shielding for medical and industrial purposes.
“We still have the original test sample and have since printed a collimator – it guides the radiation – but those were for proof of concept,” says Mike Daniels, TVF’s global sales leader. “Since then, we have done proof-of-concept printing of apertures for cancer treatment and held test runs with a local hospital.”


Woods adds that production volumes should increase quickly as manufacturers complete initial tests with new technologies and get more comfortable specifying 3D-printed components in various finished products. Automotive powertrain supplier ZF North America Inc. has test-printed in copper, and other motor vehicle manufacturers are playing with the technology.
“Once they’ve vetted our materials, we can move along as they prove our product on their products,” Woods says. “Being vetted in many areas and seeing a fair amount of prototyping going on means we’re heading in the right direction.”
The Virtual Foundry
https://www.thevirtualfoundry.com

Explore the Additive Manufacturing Guide Issue
Check out more from this issue and find your next story to read.
Latest from Today's Medical Developments
- Birk Manufacturing achieves ISO 13485 recertification
- SW North America's BA 322i twin-spindle CNC
- The role of robotics in precision medical device manufacturing
- Swiss Steel Group’s UGIMA-X machinable stainless-steel sets
- #51 - Manufacturing Matters - The Impact of M&A in MedTech 2024
- Visual Components: 25 years of simulation and programming software innovation
- Zimmer Biomet announces definitive agreement to Acquire Paragon 28
- Discover an innovative technology for EMI/ESD/TVS suppression