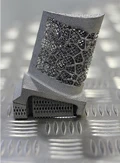
University of Sheffield

Additively manufactured (AM) lattice structures are popular because they’re lighter than solid materials yet equally strong. However, the simple honeycomb shapes favored by designers have an inherent weakness. When such structures are compressed, once the force is sufficient to cause permanent deformation, the lattice can shear along one or more node planes. With nothing to inhibit this shearing, the collapse becomes catastrophic.
Working in collaboration with colleagues from Imperial College London, Professor Iain Todd from the Department of Materials Science and Engineering at the University of Sheffield has been taking a novel approach to address the catastrophic failure issue by looking at the basics of metallurgy.
Lattice designs
Lattice structures, also known as architected materials, typically have a uniform layout with nodes conforming to a regular array with the struts between the nodes, all following common planes. These uniform lattices replicate the structure of a metallic single crystal. The nodes in the AM lattice are equivalent to the atoms in the single crystal and the struts are equivalent to the atomic bonds. In each structure, the atomic planes, or nodes, are all perfectly aligned.

In some applications, such as the high-temperature section of a jet engine, single-crystal materials are ideal because of their ability to withstand deformation at extreme temperatures.
However, Todd explains that the mechanical failure possibility remains if structures undergo deformation – shearing along their planes.
Polycrystalline solution
In polycrystalline materials, atomic plane alignment is random. A crack will slow down or stop when it meets a crystal where the atoms are aligned differently. In addition, it is possible to introduce different materials in phases, precipitates, or inclusions to strengthen the materials; these materials also help inhibit crack propagation.
This fundamental metallurgical understanding inspired the scientists to mimic polycrystalline micro-structures in AM lattices with the aim of developing robust, damage-tolerant architected materials.
Through computer modelling of atomic structures – scaling them up and creating meso-structures based on polycrystalline materials – engineers are transforming the way that materials are designed and coined the term meta-crystals.
Results
Experimental testing of components made from meta-crystals demonstrates they are highly energy absorbent, with the polycrystal-like material withstanding almost 7x the energy before failure compared to the materials that mimic the single-crystal structure.
While the basic metallurgical concepts are inspiring the development of architected materials, researchers see opportunities to study complex metallurgical phenomena.
“This approach to materials development has potentially far-reaching implications for the AM sector. The fusion of physical metallurgy with architected meta-materials will allow engineers to create damage-tolerant architectured materials with desired strength and toughness, while also improving the performance of architectured materials in response to external loads,” Todd says. “And while these materials can be used as stand-alone structures, they can also be infiltrated with other materials to create composites for a wide variety of applications.”
Dr. Minh-Son Pham of Imperial College London adds, “This meta-crystal approach could be combined with recent advances in multi-material 3D printing to open up a new frontier of research in developing new advanced materials that are lightweight and mechanically robust, with the potential to advance future low-carbon technologies.”
Imperial College London
https://www.imperial.ac.uk
University of Sheffield
https://www.sheffield.ac.uk

Explore the Additive Manufacturing Guide Issue
Check out more from this issue and find your next story to read.
Latest from Today's Medical Developments
- Birk Manufacturing achieves ISO 13485 recertification
- SW North America's BA 322i twin-spindle CNC
- The role of robotics in precision medical device manufacturing
- Swiss Steel Group’s UGIMA-X machinable stainless-steel sets
- #51 - Manufacturing Matters - The Impact of M&A in MedTech 2024
- Visual Components: 25 years of simulation and programming software innovation
- Zimmer Biomet announces definitive agreement to Acquire Paragon 28
- Discover an innovative technology for EMI/ESD/TVS suppression