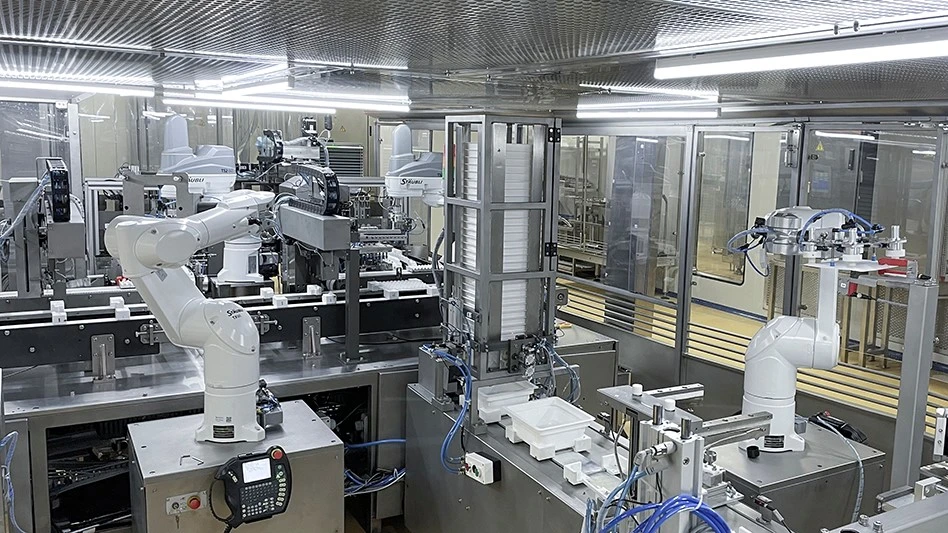
Stäubli / SCHOTT POONAWALLA
Demand for pharma packaging products vastly increased following the COVID crisis, requiring an accelerated production process. This includes faster inspection and packing without negatively impact on quality, a factor of great importance for SCHOTT POONAWALLA, a leading manufacturer of premium pharmaceutical containers made of neutral glass tubing such as vials, syringes, ampoules, and cartridges.
Since the beginning of vaccine rollout for the epidemic, SCHOTT POONAWALLA has provided pharmaceutical glass for primary packaging to fill billions of COVID vaccines worldwide. The Indian pharmaceutical packaging market of 2017 reached €1.76 billion and is expected to rise to €3 billion by the end of 2023. As a provider of high-quality pharma products for manufacturers, the company prepared its facilities for the increase in vaccine sales that was expected to triple last year.
To stay ahead of the anticipated growth in demand, SCHOTT POONAWALLA implemented a fully automated GMP-compliant production line along with a clean and hygienic environment at its plant in Umarsadi, Gujarat for the inspection and packing of pre-filled nested syringes. After comparing the speed of manual inspection and packing to an automated process, SCHOTT POONAWALLA decided to make its Umarsadi plant fully automated.

One step in a six-point process that yields two tubs per minute: Six-axis robots carry out the delicate task of nesting the syringes with high speed and precision.
Implementing Stäubli Robotics cuts time of inspections and packing time in half
Stäubli Robotics contributed to the production line by doubling the speed of inspections and packing at SCHOTT POONAWALLA’s Umarsadi plant. Manual production at the plant equated to the speed of one tub per minute; with Stäubli Robotics automation, it is done with a speed of two tubs per minute. Three types of cleanroom robot models are used to pre-fill syringes and ampoules. Stäubli Robotics Suite lessens programming time as well as modification time in offline activity.
First, SCARA robots pick and place syringes from a conveyor. Next, 6-axis robots perform nesting of the syringes. Afterward, the robots handle and inspect the syringe nest, then place QC-approved nests into the tub. This is followed by packing the nest and tub by placing inner and outer Tyvek on the tub. Lastly, the robots perform heat-sealing on the tub and bag the products.
The surface of these robots has a special coating, and the entire structure is fully sealed. Therefore, they can be cleaned with IPA, an agent for disinfecting the equipment used in the cell, normally 70% diluted. Alcohol is used as a medium of disinfecting the cell; the diluted alcohol also coagulates proteins, but at a slower rate, so that it penetrates all the way through the cell before coagulation can block it. Then the entire cell is coagulated, and the organism dies.
Following a six-point process, the robots provide clean and consistent performance of packaging and inspection of pre-filled syringes, maintaining the quality of the products. SCHOTT POONAWALLA concluded that the Stäubli robots provided consistent day-to-day, batch-to-batch production with a clean and hygienic operation. The fully automated setup with the robots also offers the company the flexibility to produce new variants.
SCHOTT POONAWALLA ensures each batch is processed identically, delivering reliable and reproducible results. By using the Stäubli TX2 and TS2 robots, SCHOTT POONAWALLA achieves great speed and repeatability. The company finds great use for automation to meet the volume of production demanded without compromising quality, as the compact robots comply with hygienic requirements.

Robots handle and inspect syringe nests, placing QC-approved nests into a tub, nearing completion of the packaging process cycle. End user safety is assured.
Stäubli enhances patient safety while performing twice as fast as manual workers
The SCHOTT POONAWALLA Umarsadi Gujarat plant began by implementing manually performed inspection and packing processes. The task was completed at a speed of one tub per minute. When the company tested an automated process using robots, the task was finished at a speed of two tubs per minute. This shows a 50% time reduction.
The company’s reputation for quality-focused products, implementing the latest technologies, has made it one of the first in the world to introduce new products like nested sterile syringes and cartridges, over and above its existing portfolio of sterile nested syringes. With quality as the central point for SCHOTT, the integration of an automated process needed to meet demanding standards to ensure end-user safety. The robots fit GMP standards and contribute to a clean and hygienic environment, the number one reason SCHOTT chose Stäubli. In addition to this, the flexibility offered by the robots to produce new variants of vials, ampoules and pre-filled syringes allows SCHOTT POONAWALLA to meet the changing demands of its customers.
Overall, the robots provide a clean and consistent performance of packaging and inspection of syringes, maintaining the quality of the products and speeding up the process. This allows SCHOTT to remain committed to international quality standards, quality assurance methods, and fully automated inspection systems.
Latest from Today's Medical Developments
- EMO: Made for game changers
- Thomson’s encoder options for stepper motor linear actuator online selection tool
- BD boosts US manufacturing of critical medical devices
- Aerotech’s HexGen HEX150-125HL miniature hexapod
- World-leading medical device supplier via a new merger
- Edge Technologies' FMB Turbo 3-38 RS bar feeder
- Mazak’s new Customer Solutions Center
- maxon's High Efficiency Joint (HEJ) Drive