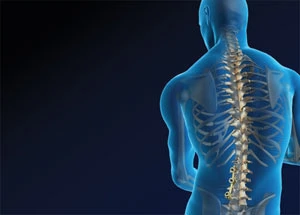
Modern cleaning processes make achieving sterilization and biocompatibility in medical devices quick and efficient.
Whether instruments, implants or accessories are involved, cleaning is an imperative step in the manufacturing process of medical devices. Modern cleaning processes make it possible to quickly, reliably and repeatedly comply with the required degrees of sterilization - all while enhancing value in the manufacturing process.
First, sticky residues from the manufacturing process, such as release agents, machining media, chips and dust, must be removed from medical devices during the cleaning process.
In addition, biocompatibility is required. The cleaning industry offers various processes in order to fulfill these requirements both cost-effectively and ecologically. For example, wet chemical cleaning, cleaning with carbon dioxide, and plasma processes are all options. Different techniques are also frequently combined.
WET CHEMICAL CLEANING
The effectiveness of wet chemical cleaning - for example immersion, spray and ultrasonic cleaning - is determined by interaction amongst the dissolving performance of the cleaning agent and the cleaning system's process technology. The most commonly used cleaning media are aqueous cleaning agents and solvents. Essential criteria for the selection of the ideal cleaning process include the material to be cleaned, type of contamination, part shape, cleanliness requirements with regard to filmlike contamination and particulates, and throughput.
The final choice is frequently corroborated by cleaning tests conducted by equipment or cleaning agent manufacturers.

The CO2 snow jet process is non-abrasive and is suitable for cleaning sensitive and finely-structured surfaces. Image source: acp
Aqueous cleaning agents are based on either an organic or an inorganic builder and tensides. The latter are able to "push" themselves in between the contamination and the material to be cleaned, dislodging nonpolar contamination such as oil and grease, as well as polar contamination such as emulsions, salts and particles. In order to prevent residues left by the cleaning agent or surface spots that could impair quality or biocompatibility, a multi-stage rinsing process is usually required - often with deionized water in the final rinsing stage(s). It is necessary to continuously monitor bath and bath replacement, at regular intervals, for consistently good results.
Solvent systems that are available as chlorinated hydrocarbons (CHC), non-halogenated hydrocarbons, modified alcohols, and polar solvents are distinguishable in regards to the type of material to be cleaned. Grease, oil, particles, etc. can be removed. Corresponding legal regulations regarding emissions limits and work safety apply to the use of solvents; these must be taken into consideration in modern system concepts. In order to achieve the desired cleaning results within the shortest possible period of time, the effectiveness of the cleaning medium is usually enhanced by means of various physical processes that demonstrate effects of varying magnitude, for example spraying, ultrasound and flushing under pressure.
When manufacturing implants, for example, it is advisable to use an intermediate cleaning step after each chip-removing machining process. This reduces the risk of any accumulation of micro-deposits on the parts, which may lead to tolerance deviations during further processing. Beyond this, intermediate cleaning prevents any mixing of lubricants and processing oils on the parts, which often cause cleaning problems.
Last but not least, the quality of downstream mechanical processing is improved by intermediate parts cleaning.
Final cleaning is usually executed by means of a validated process with an aqueous medium, which assures biocompatibility.
ECONOMIC BATCH PROCESSES
Batch processes are often used to clean medical devices in bulk goods baskets, or in workpiece carriers, which have been laid out specifically for the parts to be cleaned. In addition to the technology, the selected chemical and the duration of treatment, the cleaning rack also has a decisive effect on cleanliness and operating costs. It frequently offers potential for optimizing the cleaning process with regard to cleaning results, processing time and costs. Cleaning baskets made of round wire are ideal for assuring quick and reliable contamination removal. They allow for easy, uniform access to the workpieces by the cleaning agent, so that the mechanical washing process can develop its full effectiveness and wash out film-like contamination and particles as efficiently as possible. As opposed to closed containers or baskets made of perforated sheet metal, cleaning baskets made of round wire are also distinguished by significantly better draining characteristics.
Consequently, considerably less contamination and cleaning agent is carried over, resulting in a longer service life for the cleaning bath, and therefore improved cleaning system availability and efficiency.

The surfaces of various medical instruments and devices can be prepared for the respective application, as well as for subsequent bonding, coating or printing processes, through the use of a plasma process. Image source: Diener
PARTS2CLEAN 2009
With which cleaning process can the degree of cleanliness required for medical devices be achieved? Which cleaning agents assure a biocompatible surface? Which processes can be validated in accordance with GMP? Answers to these and other questions covering all aspects of industrial parts cleaning are provided at parts2clean. This leading international trade fair for cleaning within the production process and maintenance will take place at the new Exhibition Centre, directly adjacent to Stuttgart International Airport (Germany), from October 20-22, 2009. parts2clean 2009 allows visitors to gather comprehensive information regarding cleaning systems, alternative cleaning techniques, cleaning agents, quality assurance and inspection procedures, cleaning and transport containers, disposal and reprocessing of process media, handling and automation, services and consulting, as well as research and technical literature. For the first time ever, an international congress will be held as part of parts2clean 2009 in keeping with the maxim "Worldwide Requirements, Technologies and Markets." part2clean.comSUPERCRITICAL CARBON DIOXIDE
When parts are cleaned with supercritical carbon dioxide, the CO2 is used in an aggregation state, in which its physical characteristics lay between the liquid and the gaseous state. While in this state, it demonstrates only minimal viscosity and surface tension. Both of these attributes are important prerequisites for mass transport, making it possible to remove contaminants, such as oil and grease, from even the smallest cracks and pores. Cleaning with supercritical carbon dioxide, which usually takes place within a temperature range of 20°C to 40°C, is even capable of achieving good results with porous structures. Additionally, "biological" parameters are favorably influenced as a result of lower cytotoxicity values than those found in conventional cleaning processes.
Uses for CO2 cleaning in medical engineering include intermediate and final cleaning of implants, instruments and components made of various materials (e.g. metals and plastics). Among other things, a GMP validation package is part of the scope of delivery for manufacturers of systems for cleaning with supercritical CO2.

Cleaning with supercritical carbon dioxide makes it possible to remove grease and oil from parts and porous surfaces. Image source: eCO2
DRY AND RESIDUE-FREE
Liquid carbon dioxide is used as a blasting medium for CO2 snow jet cleaning.
It is expanded through a nozzle and accelerated to ultrasonic speeds with compressed air. A combination of mechanical, thermal and chemical effects enables the CO2 snow jet to gently clean when it strikes the surface in a dry and residue-free fashion.
Its characteristics make CO2 snow jet technology suitable for cleaning and activating almost all materials including metals, plastics, glass and ceramic substrates, even with finely structured surfaces. The jet stream can be well focused, and the process is also capable of treating specific functional areas, for example sealing and bonding surfaces, without subjecting the entire component to the complex processing that is necessary in order to achieve the levels of cleanliness that are only required for the functional surfaces.
The process's in-line capabilities and minimal space requirements allow for easy integration of cleaning into the manufacturing process, ruling out the possibility of renewed component contamination, for example during transport or storage.
MORE THAN JUST CLEAN
Plasma is a gaseous mixture of atoms, molecules, ions and free electrons.
Medical devices made of various materials, for example steel, non-ferrous metals, plastics, glass and ceramics, can be treated either in batch processes or as individual parts with this technology.

An aqueous cleaning process is frequently used for final cleaning of dental and surgical implants. Image source: Amsonic
Depending on the application, various plasma gases can be used so the surface is simultaneously cleaned and activated. This dual function is based on both physical and chemical reactions involved in the process. The atoms released in the plasma "bombard" the surface of the component to be cleaned. This functions like a miniature sand-jet in the nano-range, removing organic contamination that adheres to the surface such as oil and grease. At the same time, free ions and electrons are deposited on and enter into a chemical bond with the surface. As a result, surface tension is adjusted to an ideal value for subsequent bonding, coating or printing processes. Applications for biocompatible plasma in the field of medical engineering include final cleaning of stents, surgical and dental implants, guide wires prior to coating with hydrogel or PTFE, increasing the surface energy of microtiter plates and other diagnostic instruments, silicone breast implants, catheters, and syringes.
NGL Cleaning Technology
ngl-cleaning-technology.com
eCO2 SA
eco2.ch
Metallform
metallform.de/english.html
Amsonic Precision Cleaning
amsonic.com
Diener Electronic North America
plasma-us.com
Plasma Technology
plasmatechnology.de
acp-advanced clean production
acp-micron.com

Explore the June 2009 Issue
Check out more from this issue and find your next story to read.
Latest from Today's Medical Developments
- Unlocking GenAI's potential: Insights from the Supply Chain Horizons 2025 report
- Celebrating 75 years of innovation at Jorgensen Conveyor and Filtration Solutions
- Free webinar to offer expert advice on optimizing machining operations
- How collaboration between companies can elevate manufacturing
- AI meets innovation: Cambridge's device transforms heart screening
- Mazak and Premier Engineering team up for greater agility in Florida
- Struggling with inventory or supply chain pressures? Find answers in our free webinar
- Free webinar: Advanced manufacturing solutions to support the Navy