Advances in medical technology continue to produce new equipment featuring enhanced capabilities and greater sophistication. As a result, the industry requires motion control solutions that perform consistently and reliably. Many of today's medical devices rely on electric actuators to provide superior motion control in critical, life-saving applications. With their powerful performance, clean operation, and increased efficiency, electric actuators do not suffer the same shortcomings often found in hydraulic and pneumatic actuation technology.
Additionally, electric actuators offer diverse integration capabilities, such as combining the motor and actuator, delivering a more compact package while reducing spacing requirements. In addition, integrating the power controls within the actuator itself results in enhanced mobility, control, and application suitability.
Capable of providing the positioning, speed, and force required in not only simple medical devices but also complex, highly precise procedures, electric actuators are the ideal solution for even the most demanding industry applications. By understanding the benefits electric actuators provide from both a performance and cost standpoint, users can implement this technology in diverse applications throughout the medical industry, improving overall device reliability.
Comparison
With their advancing performance capabilities, electric actuators continue to replace hydraulic and pneumatic actuators in a wide range of medical applications. Fluid-powered actuators, such as hydraulic and pneumatic devices, require oil or air for operation, which often results in leaks. These leaks lead to a significant increase in energy use, and higher labor and maintenance expenses, ultimately increasing costs while reducing efficiency.
Hydraulic actuators require fluid for operation; therefore, when they leak, users often face additional costs for cleanup. Further, depending on the severity of the leak, it may result in damaged or destroyed equipment, requiring time-consuming repairs or costly replacements. With pneumatic actuators, leaks cause pollution concerns, as system air releases into the environment. Fluid leaks can contaminate not only the environment, but the sterile field as well, resulting in health and safety risks to patients and personnel. Therefore, it is particularly important for actuators to provide a clean operation in medical applications.
Unlike fluid-powered actuators, electric actuators rely solely on electricity for operation, eliminating the risk of costly and contaminating leaks, which not only protects vital equipment, but also safeguards products, personnel, and patients. Without the risk of leaks, electric actuators reduce excess energy costs associated with utilizing more power to compensate for wasted energy when hydraulic or pneumatic actuators leak.
In addition to their clean operation, electric actuators utilizing innovative roller screw technology provide even greater performance capabilities, ideal for the most demanding medical applications.
A roller screw is a mechanism that converts rotary torque into linear motion, similar to ball or acme screws. The higher load capacity (more than 100,000 lb) and rigidity of planetary roller screws makes them ideal for applications requiring continuous force, while providing quiet operation. The planetary design of roller screws allows them to operate at higher rotational speeds than other screw technologies, making them an ideal solution for high-speed applications. In addition, these actuators offer inherent positioning repeatability, increased longevity, and quieter operation.
Crucial Components
To maximize suitability with a wide range of medical applications, electric actuators offer complete integration of motion control system elements. By integrating power, control, and actuation mechanisms, electric actuators combine force, velocity, and positioning in a single, compact motion control device to increase performance flexibility and application compatibility.
Actuator size constraints can be problematic, as medical devices require building to precise specifications. To solve this, innovations in motor technology deliver solutions with smaller package sizes but with the same power output as previous motor designs. This allows easier integration without sacrificing performance. Integrating the motor and linear actuators into one package reduces the overall size of the actuator, enabling it to install easily into equipment or other applications with minimal space available.
In addition to a compact design, electric actuators also offer the option of integrating the electric controls and power circuitry within the actuator, providing a complete system solution. In contrast to typical motion control solutions, which require separately mounted controls and power amplifiers, this comprehensive solution eliminates dependency on external components and expensive cables. These actuators operate without a stationary electrical cabinet – allowing the actuator, drive, and control to operate as a stand-alone piece of equipment.
With these integration capabilities, the user can experience enhanced motion control while significantly increasing flexibility. Not only can electric actuators install easily in confined spaces, but they also provide enhanced mobility. For instance, combining all crucial motion control components into the actuator allows mobile medical devices to offer the same capabilities common in stationary applications. Through this type of integration, mobile medical devices operating on battery or DC power, or portable units that are moved from location to location and plugged in, include all the required control elements while minimizing the size and weight of the actuator.
Medical devices are only as reliable as their components. Electric actuators deliver dependable motion control in diverse situations – ranging from simple solutions to critical, lifesaving applications that demand precise positioning, smooth motion, and tightly controlled velocity.
For example, directed radiation therapy, often used as a part of cancer treatment programs, is cutting edge technology that applies radiation to patients in progressive increments, slice-by-slice, delivered to different sections of a tumor. During this treatment, position of the patient must be beneath a precisely fixtured source of radiation. In order to accommodate this, electric actuators manipulate the position of the patient's bed, a critical aspect of the application. The proper positioning of the bed is crucial, as the technology must target only the tumor and protect healthy tissue.
Not only does the actuator provide the positioning necessary in these applications, it also delivers the smooth motion and velocity control necessary for proper radiation application. Featuring high force density, certain electric actuators easily conceal within these types of devices, minimizing space requirements and enabling a piece of equipment, like a patient table, to feature a logical design without excessive size to contain oversized actuators.
In addition to performance and size, electric actuators also minimize the noise associated with operation. Studies show that when patients can hear noise from medical equipment during a procedure, there is a noticeable increase in their anxiety. Due to the proximity of the actuator to the patient, any audible noises produced during operation are easy to hear, creating unnecessary nervousness during medical procedures. Therefore, implementing electric actuators with roller screw technology, which offers significantly less noise than alternative actuators, assures quiet operation, increases patient relaxation and reduces apprehension during this necessary and intricate treatment.
Looking Ahead
Advancements in electric actuation technology continue to expand an already wide range of capabilities – allowing increases in compatibility for diverse industry applications. With high-quality performance, integrated solutions, superior efficiency, and environmentally friendly operation, electric actuators continue to replace fluid-powered technology, providing an optimal solution in motion control.
Exlar Corp. Chanhassen, MN
exlar.com
Products
Brushless, 70W DC Motor
The 70W flat brushless motor delivers a maximum, continuous torque of 130m/Nm at an efficiency of up to 85%. The motor, in its 45mm diameter, is available with Hall sensors, coming in four windings (24V, 30V, 36V, and 48V) and is combinable with more than 54 different planetary and spur gearheads. Designed as internal or external rotor motors, they are often the ideal solution when space is limited. The well planned design means that production is largely automated.
Maxon Motor Usa Fall River, MA
maxonmotorusa.com
High-Pressure, One-Way Valve
A high pressure, normally closed, back check valve that handles 400psi for both forward and backward pressure is now available. Designed for the intermittent injection of fluids while preventing backflow, the one-way valve opens when 1.5psi to 5psi of pressure is applied.
Manufactured with a polycarbonate housing and silicone disk that are gamma-compatible and lipid-resistant, the valve meets patient safety and environmental concerns, and does not contain latex or DEHP.
It is the newest member of an extensive portfolio of valves that are available as stand-alone components or as part of a custom set or device.
The B. Braun OEM Division Bethlehem, PA
bbraunoem.com
Linear Servomotor Replaces Piezo Motors
The 4mm linear shaft motor delivers a small size (10mm x 10mm), a total weight of 9g, and strokes as long as 40mm, making the 4mm linear shaft motor a suitable replacement in piezo-type applications. The 4mm linear shaft motor is quiet due to the absence of friction, since the only mechanical contact section is the linear guide. The coreless construction of the linear shaft motor eliminates cogging. The linear shaft motor's high motor stiffness allows use in high precision positioning applications where a resolution of 0.09µm is achievable. With the linear shaft motor there is virtually no fluctuation in speed.
Specifications for S040D Linear Shaft Motor:
- Continuous stall thrust - 0.5N
- Continuous stall current - 0.4A
- Peak thrust 2N
- Peak current - 1.8A
- Shaft diameter (D) 4mm (0.16")
- Slider length (A) 25mm (0.98")
- Slider width (B) 10mm (0.39")
- Mounting pitch (P x P1) 21.5mm x 4mm
- Mounting screw (M x l) 4-M2
- Gap 0.5mm (0.02")
- Slider weight 0.01kg/F
- Available stroke 20mm, 30mm, and 40mm
- Magnetic pitch (N-S) 9mm (0.354") (N-S)
Electromate Greenville, DE
electromate.com
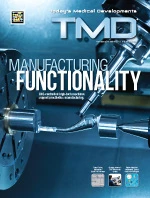
Explore the November December 2011 Issue
Check out more from this issue and find your next story to read.
Latest from Today's Medical Developments
- North American robotics market holds steady in 2024 amid sectoral variability
- Evident’s DSX2000 digital microscope
- Ferrocene becomes first Rust toolchain to achieve IEC 62304 qualification
- Germany expects a major decline in production in 2025
- Learn what you need to comply with CMMC requirements
- VersaBuilt’s CNC automation possibilities
- ROBOTICS AWARD 2025
- There’s still time to register for this week’s manufacturing industry webinar!