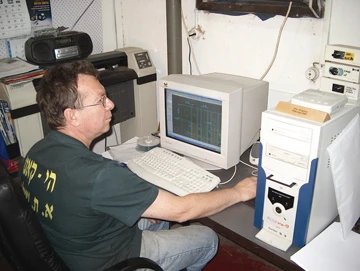
An Israeli CNC shop owner uses state-of-art technology to save a little girl's life.
Just before lunch one Thursday afternoon in December 2004, Daniel Schwartz, owner of a small Israeli CNC metalworking shop -- Hi-Cut Shilat -- took an urgent call from an old friend. She was a senior physician in the intensive care department of large hospital. The doctor wondered if her friend would be willing to quickly design and manufacture some parts to be used to save a little girl's life. Schwartz was soon on his way to confer with the team of doctors scheduled to perform the needed surgery on Sunday.
The patient was a Palestinian girl less than a year old, suffering from a rare condition called Jeune's Syndrome. The girl's ribs were distorted due to the disease. Even worse, they hadn't grown at all in about six months. As a result, the child's lungs could barely expand or contract. She was in severe distress, fighting for each breath, capturing just enough air to stay alive. There was little time left for her.
Only a day earlier, doctors were planning to perform a customary procedure in which a number of ribs would be severed, and then rejoined with a flexible acrylic material. While this would relieve the pressure that her dwarfed rib cage was imposing on her lungs, it would also deprive her ribs of the unitary stiffness that makes normal breathing possible -- an unfortunate but necessary compromise.
On Wednesday, a package arrived from a Children's Hospital in the U.S. It contained a description and sketch of a new surgical procedure that joined alternating severed ribs with metal connecting rods. This approach would eliminate pressure on the lungs while allowing the rib cage to maintain the structural integrity needed for proper breathing. The doctors at the Israeli hospital knew immediately that this offered a far superior alternative. During the Sunday operation, they would use it on the little girl if they could only obtain the all important titanium parts.
Wedding Rings, Full Circle
Why did Danny Schwartz get the call? It was because of an unusual pair of titanium wedding rings he had made for a friend and his fiancé ten years earlier.
Hi-Cut Shilat is a small but high tech shop that makes parts for cameras, electro-optical systems, injection molds, and other devices requiring high precision work. Equipment includes a 4-axis milling machine, two wire cutting machines, four EDM systems, and two die sinking units. The shop also has two Mastercam CAD/CAM software stations from CNC Software Inc., Tolland, CT, used primarily to program the machine tools but also for design work. Schwartz is intimately familiar with all of his equipment. A long-time user of Mastercam, Schwartz is currently using its latest release, Mastercam X. He began using Mastercam about a decade ago because it was the only software at the time that provided a single programming environment for milling, wire cutting, and turning. In those days, Schwartz used his design and machining skills to create rings for his friend's wedding. Each was dovetailed, allowing them to interlock and remain a unit unless skillfully separated. After marriage, the wife went on to medical school and ultimately to the staff at the children's hospital.
Over the years, she had shown her rings to many impressed hospital staffers. When the surgeon who was to perform the operation on Jeune's Syndrome baby realized he would need machined titanium parts, he thought almost immediately of the rings. The person who created those wedding rings would be just the man for the job. Danny Schwarz was summoned by his doctor-friend, the ring's proud owner.
48 Hours
When Schwartz saw sketches of the needed parts, he was confident he could make them. When he was told that there were no drawings or specifications and they had to be delivered before Sunday morning, he was flabbergasted.
Because it was a matter of life or death, Schwartz agreed to take on the job, but with two conditions: He would not be held responsible in any way if the operation failed and a doctor had to be available at all times during the next two days to answer any questions.
With that understood, he left word at his shop that all of the work in progress had to be taken off the machines and the machines were to be cleaned. The three machinists were then instructed to go home and not return for the next two days. This would give Schwartz freedom to use all of his equipment simultaneously to meet the deadline.
Before leaving for his shop, Schwartz and the surgeon used a tailor's tape measure to take a series of measurements on the child and estimate the dimensions of the connecting rods he would be making. Late at night back in his shop, Schwartz took about three hours to design the parts on Mastercam and program the necessary machining operations. For the next day and a half, without sleeping, he went from one machine to another setting them up to cut the titanium connecting rods and screws.
Lamb Bone Prototyping
On Saturday night, shortly after Schwartz had finished making the parts, his doctor friend arrived from the hospital with fresh lamb shank bone. As a test, the bone was cut in two pieces and joined using the newly manufactured titanium screws and connecting rod. If the connection was not secure, Schwartz would have to rework the parts that evening. Fortunately, rework was not necessary and the doctor took the parts and returned to the hospital.
The next morning surgery was successfully performed on one side of the baby's rib cage. Her bones were not firm enough for the titanium screws to hold, so the surgeon had to devise a special suturing technique to fasten the rods in place. Otherwise, the operation was a complete success. Two days later, the team operated on the other side of the little girl's body with equally satisfying results.
Schwartz was deeply gratified that he could meet the job's deadlines and be part of this lifesaving mission. He says, "If a customer asked me today for such a part -- not in an emergency -- the whole job would take three to four weeks. The parts themselves were not complicated but the sequence of manufacturing steps is: making a wire cut in first position, then the second position, moving it to the 4-axis milling machine, drilling them, then doing dimensional and surface finish milling."
What helped most, he says, was his own intimate familiarity with the CAD/CAM software and CNC machinery -- the ability to design and program CNC equipment in one environment without needing to translate and having a single CAD/CAM software engine that spanned all his equipment.
Schwartz says he is proud and grateful to lend his shop and personal skills to such an important purpose. "This is proof," he says, "that one guy with terrific software can design and program and operate four different machines and in one weekend save the life of a human being. Who needs more than that?"
Meet Your Neighbor
About four weeks after the surgery, Schwartz received a call from his doctor- friend. The parents of the young girl did not have their own automobile and had to make all the trips to the hospital using public transportation. That day, she drove them to the bus station.
"So what do you do for a living?" she asked the father.
"I work as a carpenter in a little village you probably never heard of, about halfway between Tel Aviv and Jerusalem," he answered. It's called Shilat."
Schwartz was surprised to learn that the little girl's father is employed at a woodworking shop about 200 meters from Hi-Cut Shilat. "Not long after that, he came in here one morning and it was very exciting," Schwartz said. "Now I see him at least every two or three months."
As for the baby, more than a year has passed and she is doing very well. TMD
CNC Software Inc.
Tolland, CT

Explore the June 2006 Issue
Check out more from this issue and find your next story to read.
Latest from Today's Medical Developments
- Birk Manufacturing achieves ISO 13485 recertification
- SW North America's BA 322i twin-spindle CNC
- The role of robotics in precision medical device manufacturing
- Swiss Steel Group’s UGIMA-X machinable stainless-steel sets
- #51 - Manufacturing Matters - The Impact of M&A in MedTech 2024
- Visual Components: 25 years of simulation and programming software innovation
- Zimmer Biomet announces definitive agreement to Acquire Paragon 28
- Discover an innovative technology for EMI/ESD/TVS suppression