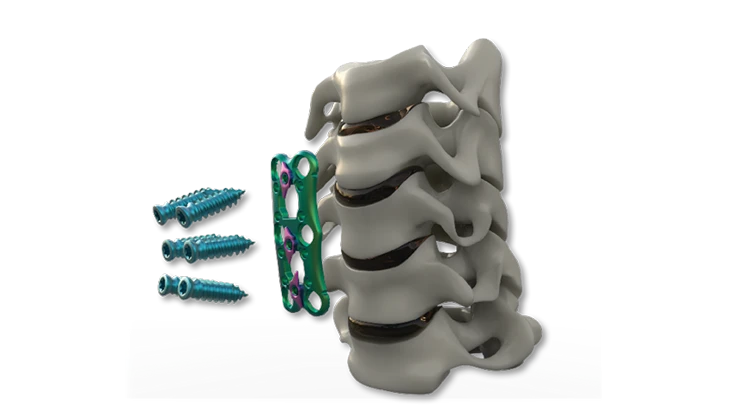
Nexxt Spine

Whether 3D-printed or machined from titanium blanks or polyether ether ketone (PEEK) blocks, spinal implants demand precision. And, with demand increasing from an aging U.S. population, high productivity is key. Noblesville, Indiana-based Nexxt Spine LLC’s leaders say working with trusted manufacturing partners has supported its expansion into advanced implant designs and new production technologies.
“We’ve grown 30% every year since 2009,” says Nexxt President Andy Elsbury. He adds that the company produces about 800 PEEK spinal implants per year, but recent growth has been for titanium 3D-printed Matrixx implants. “That is where we are growing faster than 30%.”
For more than a decade, Nexxt has machined its Honour and Struxxure implant lines from PEEK rods and titanium blanks using Haas machining centers. The company recently added a Haas drill-tap center to machine features into its Matrixx products, and Elsbury says fast growth in that product line will likely lead to new machine purchases soon.


PEEK, Titanium machining
The high percentage of Nexxt’s orders are still from the Struxxure line of anterior cervical plate system implants that must be completely machined from blanks. Nexxt Programmer Beau Riser says the company uses various Haas machining centers to machine fixed plates, variable plates, and spacers for its implants.
“These cervical plates are implanted from the front,” Riser says, pointing to his neck. “Surgeons actually move your esophagus over and then implant them, and then your esophagus goes back over the top of it. You’ve got a plate sitting on your vertebrae and your esophagus is basically sitting up against that. If those screws back out at all, any time you swallow it’s going to feel like you’ve got something in the back of your throat.”
The implants use fixed or variable plates and fixed or variable screws. Fixed plates allow the screws to only go in one direction at one spot, while variable plates allow some movement around the screw head. Different surgeries require different approaches, but most implants have a mix of fixed and variable spots, all of which need to be machined to surgical-grade tolerances.
“This one plate can be used with a fixed screw, variable screw, or both. That’s why ours is, in my opinion, the best,” Riser adds. “We have sold thousands upon thousands of these things, and we’re getting very good feedback from the doctors. It’s working well for the patients.” Nexxt machinists can make two pieces simultaneously on their Haas CNC equipment, programmed with Mastercam software. Careful material handling policies mean PEEK parts use metal fixtures and titanium parts use plastic ones. All pieces are machined dry (PEEK can absorb some lubricating fluids), and employees wear gloves, so the parts don’t contact human skin until they enter the patient.
“The shortest cycle time is about half an hour,” Riser explains, adding that he uses about 15 tools for each part. “I do everything in one operation. I flip it over and do the bottom. The longest one is more than two hours.”
About a year ago, Nexxt added a Haas DM-2 drill-mill vertical machining center (VMC) to increase capacity for the machined titanium implants. “I love that thing,” Riser says, praising its speed and rigidity. “It has the new Haas Next-Gen CNC control, I’m getting used to, and I like it. We made a plate on the Haas VM-3 (mold-making VMC milling machine), and then I took the exact program, added nothing, took nothing away, put it on the Haas DM-2 and it went from 7 minutes to 5 minutes.”

Additive Titanium
Introduced in late 2017, Nexxt’s Matrixx 3D-printed titanium implant is its fastest growing product line. Since launch, more than 2,000 units have been surgically implanted into patients.
“It’s made out of titanium which the body likes better than plastic,” Elsbury explains. “It is porous, so we have 300µm, 500µm, and 700µm sized pores. The surface finish is micro-roughened to help the bone fuse.”
Nexxt 3D prints the implants in-house, typically printing several implants on a common plate then removing them using electrical-discharge machining (EDM) wire-cutting machines. Nexxt then sends them out to suppliers for heat treatment. Once parts return, machinists add taps and other surface features in the shop using the Haas DM-2.
With demand growing, Elsbury expects the additively manufactured parts to surpass the shop’s machined products lineup eventually, but he adds that the medical community has a learning curve to become more comfortable with printed parts.
“The medical community has been using PEEK for 20 years. You’re not going to change that overnight. The surgeons now will put in two or three Matrixx implants, wait a month, [put in] two or three implants, wait a month, put in two or three implants, because they’re waiting to see how these patients do with the implant,” Elsbury explains. “After about a four-month period, where they’ve seen how these patients are all progressing, then they will switch all of their implants from PEEK to Matrixx.”
The printed parts are also simpler mechanically. Instead of machining spacers and plates, the Matrixx implants only need spacers. Screws go into the bone through tapped holes in the implant, eliminating the need for plates. The porous, roughened surface of the implant is designed to promote bone growth, leading to faster recovery times for patients, Elsbury adds.



To help buyers become more comfortable with the technology, Riser says Nexxt conducts tests beyond Food and Drug Administration (FDA) requirements. For example, on each 3D-printing plate, the company prints dog-bone shaped parts using the same lattice structure as the implants. Those dog bones then go through heat treatment and come back to Nexxt with the implants. Employees test the dog bones on a test bench, pulling them until they snap to know the mechanical strength of that batch of implants.
Haas Automation Inc.
https://www.haascnc.com
CNC Software Inc. (Mastercam)
https://www.mastercam.com
Nexxt Spine LLC
http://nexxtspine.com

Explore the April 2019 Issue
Check out more from this issue and find your next story to read.
Latest from Today's Medical Developments
- Midwest DISCOVER MORE WITH MAZAK
- Reshoring survey to provide insight for US industrial policy
- NB Corporation of America's ball splines
- Zimmer Biomet to acquire Paragon 28
- Industrie 4.0 award for Paul Horn GmbH
- CMMC requirements and your business
- Stryker exiting spinal implant business
- Perfecting the manufacture of microscopically thin films for tech, medical applications