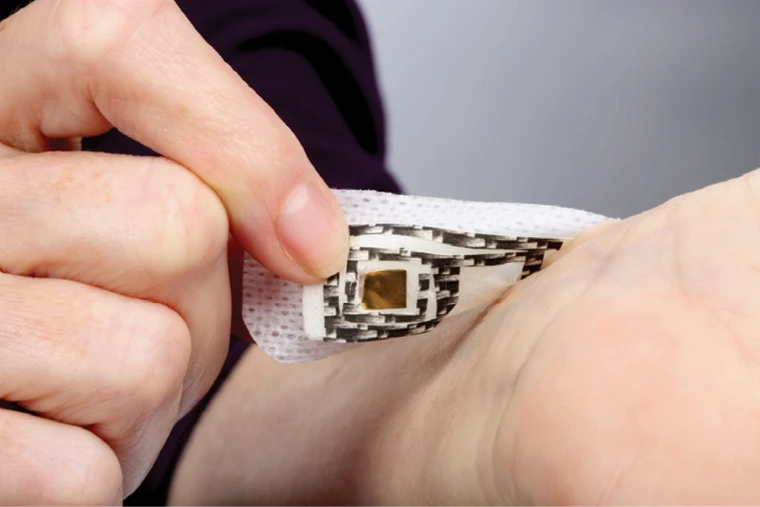
3M

Adhesive plays a critical role in the success of a medical device. Too often, the “tape is tape” mindset causes adhesive selection to happen too late in the device development process – after decisions about device housing material or finishing processes – without considering how an adhesive’s characteristics will impact the device’s functionality and accuracy.
To avoid resulting unforeseen costs and delays, adhesives must be considered at the outset of the design process.
Treating adhesive selection trivially can result in issues including manufacturing problems, device malfunctions, and harm to the user.
Bad: Manufacturing problems
When designing the device, did you also design for manufacturability? As a prototype, your device may look, feel, and function as it should, but if it can’t withstand the speed and friction of manufacturing, inappropriately selected materials will become painfully obvious. Adhesives inappropriately selected can be too soft or incompatible with other materials.
A too-soft adhesive can gum up equipment during production or converting, resulting in unscheduled downtime and unforeseen costs. Accompanying materials, such as liners, or the support film that’s removed before the adhesive is applied to its end-use substrate, can break or fail during production if the properties can’t withstand speed and tension.
Adhesive is a seemingly small component, but it can have an immense impact on manufacturing schedules and budgets. Bring material suppliers into the process early to ensure adhesive and backing combinations are optimized to withstand manufacturing.

Worse: Device malfunctions
Once a device is manufactured, the wrong adhesive can still do its share of damage. The three top concern areas are accuracy, reliability, and material purity.
Accuracy is paramount for devices aiding in health decisions. Stick-to-skin device accuracy depends on the adhesive keeping the device attached for a specified time. Insufficient adhesive – whether it lacks strength, breathability, or moisture resistance – could cause a device to prematurely detach, compromising readings.
Adhesives that bond device components together rely on how well the adhesive keeps specific parts in place. When parts or the device move, performance may be compromised. An extended border around the device – a skirt – can keep the device in its intended location, in addition to improving stability and increasing wear time.
The wrong adhesive can also negatively impact lab-on-a-chip device accuracy. In these applications, remnants from manufacturing, finishing, or other processes can interact with the assay being tested, endangering its integrity. A cleaning step included in manufacturing processes helps prevent this.
Reliability, or a lack thereof, can also have detrimental effects. With an insufficient bonding method, the flex circuit could de-bond from a printed circuit board. Conductive adhesives can replace soldered connections in some instances. They can also make for a quicker, more efficient conductive connection. However, some choices can create directional connections.
Material purity problems can cause adhesives to combine with other materials. One particularly devious category to be aware of is plasticizers; when added to other plastic or rubber materials, plasticizers create softer, more flexible features – a desired attribute in some situations, but one that can create bonding issues when an adhesive must stick to such altered materials. Typically, the initial bond is good. In time, the plasticizer can migrate into the adhesive, softening it. This problem isn’t always seen early in the device’s evaluation because it takes time to develop. When using a plasticizer, engage a knowledgeable adhesive supplier to identify a tolerant solution.
The worst: Harm to the user
Skin is a unique substrate. It’s a living, breathing organ that helps keep us healthy, regulates our temperature, and protects us from infection and other environmental harm. To do those jobs properly, it must be able to move, flex, and expel moisture, regardless of whether a device or adhesive is attached to it. Therefore, skin must be prioritized when designing a device.
Not all adhesives are skin-friendly. Some will attract dirt or lint during wear, while others will leave residue after removal. These situations don’t cause real harm, but the unsightly result is avoidable. Other adhesives can cause serious, potentially damaging outcomes to skin, such as allergic reactions and medical adhesive-related skin injuries (MARSIs).
Allergic reactions are possible if an adhesive is incompletely cured or contains materials that migrate into or onto the skin. Choose a supplier that follows ISO10993 procedures for testing materials to minimize the risk of skin reactions.
MARSIs are commonly caused by choosing the wrong adhesive for an application.
They sound like a minor consequence, but MARSIs range in severity from skin irritations, such as maceration (trapped moisture) or folliculitis (irritated skin follicles), to more serious outcomes, such as skin tears and tension blisters. Skin is our first line of defense against infection. With adhesives having the power to compromise its strength, it’s important to know which adhesives are best suited for stick-to-skin applications.
A user who experiences unnecessary pain caused by a device may not want to use that device again or suggest it to others.

Before you design
To help get your device started on the right path, consider the following questions before beginning the design process.
To what substrate will the device adhere?
Who will be using this device?
Skin as a substrate operates differently than plastic or metal. Choose a compatible adhesive.
Which environment will the device live in?Humidity, or its lack, affects adhesive. One that withstands well in an arid climate may not function as well in a humid one. Consider humidity levels when selecting an adhesive, particularly if moisture will need to move through it.
What’s the device’s intended wear time? Not every adhesive can adhere for the same duration or will do so in the same manner. Some increase in strength throughout time, making them dangerous to use if they need to be removed at prime strength. Choose an adhesive that coincides with the intended wear duration to avoid over-designing a device.
Harder-to-answer, project-specific questions will also need to be addressed, but the above will help get your project headed in the right direction.

Explore the May 2019 Issue
Check out more from this issue and find your next story to read.
Latest from Today's Medical Developments
- HERMES AWARD 2025 – Jury nominates three tech innovations
- Vision Engineering’s EVO Cam HALO
- How to Reduce First Article Inspection Creation Time by 70% to 90% with DISCUS Software
- FANUC America launches new robot tutorial website for all
- Murata Machinery USA’s MT1065EX twin-spindle, CNC turning center
- #40 - Lunch & Learn with Fagor Automation
- Kistler offers service for piezoelectric force sensors and measuring chains
- Creaform’s Pro version of Scan-to-CAD Application Module