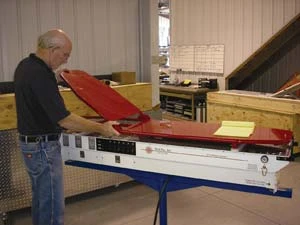
After serving in the Air Force in Vietnam, then joining an aircraft manufacturer as director of maintenance, Ralph Braaten next started his own company. Today, Med-Pac Inc. Lake Park, MN manufactures customized life-support systems for aircraft. Success for Braaten comes with the designs of his units. He is committed to meeting the challenges inherent in providing life saving equipment where it's needed when it's needed. It could range from a trauma victim picked up at the site of an accident, to transportation of a terminal patient, a burn victim, or a number of other types of emergency transfers. However, getting started in the business was no walk in the park as Braaten explains. "All U.S. built aircraft are built under a type of certification. I needed to go through engineering data and drawings to get FAA approval, which is called an STC (Supplemental Type Certificate). This allowed my part to be used on aircraft. Then, I had to apply with another division of the FAA, the MIDO (Manufacture Inspection District Office) that controls all the manufacturing in the aircraft industry. They needed to issue a PMA (Parts Manufacturing Approval). It's impossible to get a PMA without having an STC. Once I received all the necessary approvals, I could build aircraft parts for other vendors and have them approved under my PMA. They could then purchase PMA parts directly from me." Additionally, the Federal Aviation Administration (FAA) mandates that products like Med-Pac's must meet or exceed 12 to 12.5 G force. Braaten's units have been tested to 16 G. The unit takes up little space in the aircraft. It measures 72-in. long x 16-in. wide on its top deck, and is only 9-in. high. The unit contains a 3,300-liter cylinder, an air compressor, suction and inverter that runs on DC current but it may be changed to 115 or 220 AC. Braaten says that 75% of the material used in the manufacturing and fabrication process is aluminum, with the remainder constructed of steel. While most work is aluminum fabrication, "each unit has roughly 15 hours of machine work," explains Braaten. "However, there are some designs that have required as much as 30 hours of milling. Then there's at least five hours of turning for each unit. We definitely use every machine in the shop." Even though there are no standard Med-Pac parts, each of Braaten's parts are built to his design data and machined to his design criteria. All manufacturing takes place in his shop, with the exception of powder coat painting and fabric material for stretcher cushions. In addition to aviation, Med-Pac is garnering business from other markets like the marine, automotive, farm implement, and heavy steel fabrication. In order to do so successfully, Braaten uses MFG.connect buyers with suppliers of manufacturing services. The website company's proprietary technology supports the request for quote (RFQ) process, supplier discovery, engineering data exchange, revision control, collaboration, due diligence, analytics and supplier management. As Braaten explains, "We've got the capacity for CNC milling, turning, CNC plasma cutting, Tig welding, CNC shearing and CNC pressbrake work, so we started looking around at what else is out there". "By joining and using the e-business network for the manufacturing industry, word spread nationwide about the kind of work we do here," says Braaten. "Our customer base has doubled because of MFG.com, and the requests are coming in faster and faster. In fact, we are in the process of adding 6,000 sq ft to the existing 4,500 sq ft original facility to meet the demand." TMD

Explore the September October 2006 Issue
Check out more from this issue and find your next story to read.
Latest from Today's Medical Developments
- HERMES AWARD 2025 – Jury nominates three tech innovations
- Vision Engineering’s EVO Cam HALO
- How to Reduce First Article Inspection Creation Time by 70% to 90% with DISCUS Software
- FANUC America launches new robot tutorial website for all
- Murata Machinery USA’s MT1065EX twin-spindle, CNC turning center
- #40 - Lunch & Learn with Fagor Automation
- Kistler offers service for piezoelectric force sensors and measuring chains
- Creaform’s Pro version of Scan-to-CAD Application Module