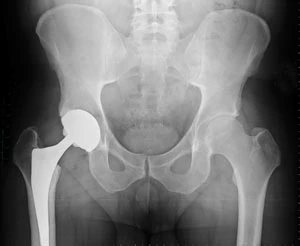
Innovation continues to be an important driver for profitability within the medical devices industry.
Indeed, the largest portions of industry profits come from products introduced in recent years, due mainly to the short lifecycle of three to five years for new medical device products, compared with the 18 to 20 years associated with a new pharmaceutical drug.
Some of the most exciting innovations happening within the industry are in the area of materials and surface coatings.
Materials and surface coatings have long needed to be biocompatible in order to be used in medical device applications, such as orthopedic and vascular implants, dental and drug delivery systems. Increasingly, however, more active material properties such as bioactive, biodegradable, biointegrative and controlled-release are becoming the innovation drivers in medical devices materials technology. There are high expectations that these new developments will aid patient recovery, reduce complications, and eliminate the need for repeat procedures. Therefore, it is expected that these innovations will increase the long-term success rates of medical procedures, and improve the comparative cost-benefits analysis within the healthcare industry.
IS IT BIOCOMPATIBLE?
Biocompat ible impl ies that the materials or devices employed provide the collective ability to perform a function for the host - the person in which the medical device is used - in a specific application, while not having side-effects on the biological system.
The use of biocompatible materials and coatings over the past 60 years is well documented for a range of different applications. For example, metals such as stainless steel and cobalt alloys have been widely used for orthopedic implants in joint prostheses applications because of their mechanical behaviors, including elastic modulus, wear and fatigue.
Orthopedic implant devices are likely to have undergone some surface coating or modification to reduce the effects of corrosion on the body - for example, render them biocompatible - or to reduce the potential of mechanical failure.
DOES IT DISSOLVE?
Biodegradable and bioabsorbable materials and devices used in a medical context are those that dissolve away into the body after a period of time, once their usefulness has reached an end.
Biodegradable polymers can be used in many medical applications.
There are two main types of polymers used, natural-based or syntheticbased.
The synthetic-based polymers have found many more uses as they are less likely to induce toxicity and infections. Furthermore, devices from synthetic polymers can also be produced with a higher predictability of mechanical and physical properties, such as tensile strength, elastic modulus and degradation rates.
Polymers belonging to the polyglicolic acid (PGA) and polylactic acid (PLA) families are being used in an increasing number of biomedical appl icat ions, such as sutures, surgical adhesives and drug delivery.
For example, absorbable sutures manufactured from synthetic polymer material last long enough to allow the body to heal before breaking down and dissolving away within the tissues; therefore, no additional medical procedures are required. These are now used extensively for internal suturing applications.
BIOACTIVE ABILITY
Bioactive means having an effect upon a living organism and, in a medical devices context, this can apply both to materials that are able to interact with living tissues, or to a device from which an active agent or drug is released.
In terms of materials, the most developed bioactive materials have been based on glass and glass-ceramic compounds including bioglass, apatite- wollastonite (A-W) glass-ceramic, and calcium phosphate materials for skeletal repair and reconstruction procedures.
Some of the most promising new areas for biodegradable and bioactive materials are now emerging for applications around tissue engineering.
In this application, biodegradable polymers and bioactive glass and ceramics are being combined into composites materials to produce 3D scaffolding with high porosities suitable for tissue engineering. The ceramic particles add significantly to the degradable polymer, by adding strength and stiffness, and have the bioactive ability to adhere and encourage new bone growth for the implant. As the body regenerates, the tissue implant degrades and dissolves away within the body.
CONTROLLED RELEASE
The biodegradable polymers discussed earlier are attractive as potential drug delivery implants; once implanted they need not be retrieved or further manipulated as they simply degrade as a non-toxic by-product of the procedure. The degradation and erosion of the polymeric can also be used to control the release of drugs at a desirable rate. Research into controlled release has become more important as some of the more novel drugs being developed are more potent and less soluble then traditional drugs.
CONCLUSIONS
Some of the most exciting innovations within the medical device industry are in the area of materials and surface coatings. Increasingly more active material properties, such as bioactive, biodegradability, bio-integration and controlled release are becoming the innovation drivers in medical devices materials technology. There are high expectations that these new developments will aid patient recovery, reduce complications, and eliminate the need for repeat procedures within the healthcare industry.
CERAM
Staffordshire, United Kingdom
ceram.co.uk

Explore the July 2009 Issue
Check out more from this issue and find your next story to read.
Latest from Today's Medical Developments
- Global Industrie - A meeting to understand, anticipate and contribute to the industry of tomorrow
- Wintriss’ Tracker Hardware Solution for ShopFloorConnect Production Tracking Software
- Protolabs expands end-to-end manufacturing capabilities
- Sunnen’s HTE-1600W Tube Hone
- Researchers invent soft, bioelectronic sensor implant
- HEULE’s DL2 tooling
- Application Park shows off diverse robotics applications
- Join our editors for a look at the manufacturing industry in 2025