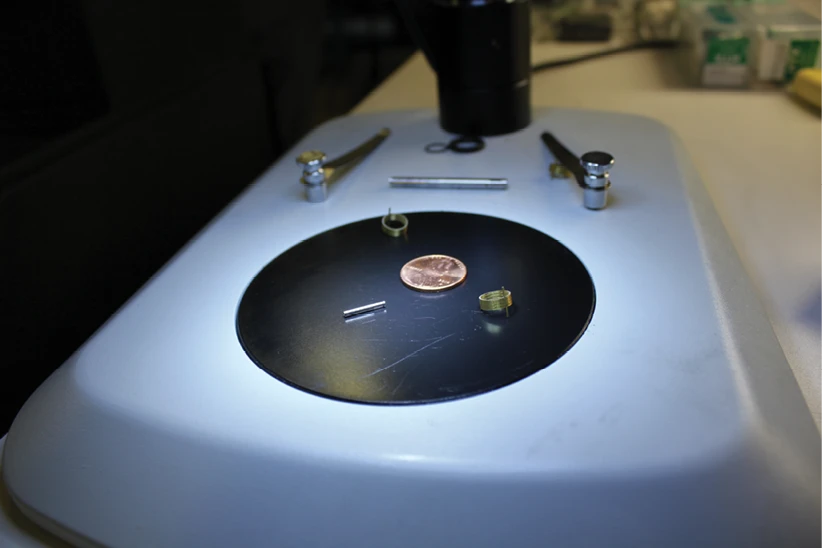

With a combined 88 years of experience in manufacturing and engineering, Pulse Systems’ President and CEO Herb Bellucci and CNC Machining Manager Dave Schell have encountered just about every machining challenge imagineable, but prior solutions don’t necessarily address challenges arising today.
Manufacturing technology is constantly evolving as innovations quickly antiquate today’s optimal processes. That inspired the medical part manufacturer to consider combining laser machining with Swiss turning, making Pulse Systems the first company to buy Tsugami’s B-axis LaserSwiss, and subsequently become the first company to purchase the LaserSwiss SS207-5AX.
The Tsugami 20mm, 7-axis Swiss-style CNC lathe with B-axis and a fully integrated laser cutting system provided Pulse Systems with a new way to manufacture a part for one of its key customers.
“The customer’s metal injection molding (MIM) process was failing to produce a waterjet nozzle that could pass inspection. The part kept failing because it could not withstand the high pressure from the waterjet,” Schell says.
“The waterjet was just eating up the part,” he adds. “Our customer has since replaced that MIM part with a turned part that we make on the LaserSwiss. They’ve been testing it and they’re very pleased with the wear erosion performance, compared to the MIM part.”
In addition to providing an alternative manufacturing option for the MIM part, the LaserSwiss consolidated operations – performing Swiss turning and laser cutting operations with one setup, with all operations programmed and driven from the machine’s Fanuc 31i-B5 control.
The laser’s nozzle stand-off adjustment is CNC controlled, and its frequency, pulse width, focus, and power are adjustable on the fly. Schell says he couldn’t run the waterjet nozzle without the machine’s B-axis, and he now uses the LaserSwiss to machine several small parts.
“There are other ways to run parts, but they’re not as fast or accurate,” Schell notes. “The Tsugami is very responsive.”

Time, material savings
The company also uses the LaserSwiss to manufacture a round, hollow, thin-walled part with puzzle cuts around the diameter. Run from SB 360 brass bar stock, that part previously required two machines for completion.
“We used to drill the ID, turn the OD, then send the part to the laser,” Schell explains. “Then we’d laser cut five parts, and out of a 3" blank we were throwing away 2" of material.”
On the LaserSwiss, the part is finish machined in 90 seconds, with one repeatable and predictable process. In addition to a 25% improvement in cutting times, the LaserSwiss reduces material waste.
“We were throwing away two-thirds of the material with our old process,” says Schell, who also appreciates not having to move the part during processing. “I’m a firm believer in one-and-done. When you move parts from one machine to another, you risk handling damage and you potentially jeopardize precision.”
Other parts run on the LaserSwiss include a stent-like, thin-walled flexible part that was previously manufactured as a two-piece weldment.
“Instead of making two pieces and laser welding them together, we now make it as a single piece in one operation on the Tsugami,” Schell says.


Incorporating disruptive technology
“We make excruciatingly small parts,” Bellucci says. “It’s everything related to sub-millimeter parts typically used in minimally invasive surgeries, catheters, and implants.”
Because these parts often come in contact with the human body, tolerances are tight, and edges must be completely burr free. Although the machine was designed for this type of precision, Pulse Systems just as often uses the machine as a basic roughing tool.
Making preliminary cuts on extremely small, thin-walled parts with an end mill can be time consuming, Schell explains, because you must remove the metal one thin layer at a time, using several passes to avoid damage.
“What we’ve done is used the machine’s laser as a rougher. We blow a laser cut through the wall, and then mill the finish,” Schell says.
The laser can produce the same high-quality surface finish as milling can, but he notes some customers still request a milled finish.
“Everyone wants everything at a lower cost. Cutting time reduces cost, so more and more, we’re using the laser as a rougher,” Schell says.
Pulse Systems also uses the LaserSwiss as an etching tool for another version of the SB360 brass part – a spring-like electrical contact. Machinists laser-etch the part’s windows on the Tsugami, then dip the part in an acid wash where etched material inside the windows cleanly falls out.

Finding work for the LaserSwiss hasn’t been difficult. According to Bellucci, on the laser side of the shop machinists work three shifts, five days a week, and the machine is booked up.
It’s a capital investment Bellucci and Schell are proud of, so it’s the first machine customers see when they visit the company.

“We moved another machine to put this one in front,” Bellucci says. “The LaserSwiss is an important part of where we’re headed as a company.”
Tsugami/Rem Sales
www.remsales.com
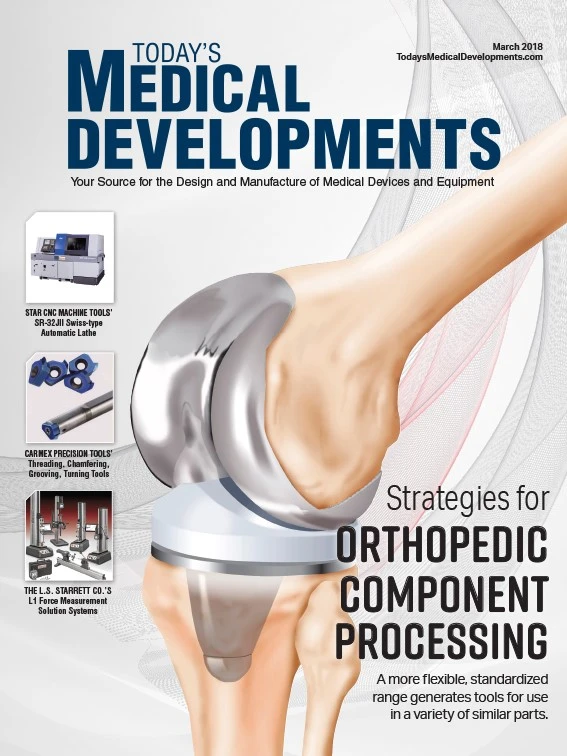
Explore the March 2018 Issue
Check out more from this issue and find your next story to read.
Latest from Today's Medical Developments
- Betacom, Siemens launch 5G network platform to accelerate manufacturing innovation
- Starrett’s AVR400 CNC vision system
- US cutting tools orders decreased 2% from November 2024
- SMW Autoblok's Manual Jack connection kit
- MedTech Innovator welcomes five new industry partners
- First Article Inspection for quality control
- The manufacturing resurgence is here – are you ready?
- Workholding solutions for your business