
Turn-Assist 200i & 270i for Nakamura-Tome
The Turn-Assist 200i and 270i from RoboJob is an end-to-end standard automation system for Nakamura-Tome turning centers.
A semi-collaborative system engineered for lathe automation, Turn-Assist can be implemented and run by operators of any skill level. With a simple tablet-style human machine interface (HMI) and standard Ethernet IP interface, shops can change from one part to another within minutes.
“By pairing the Turn-Assist from RoboJob with Nakamura-Tome, we have created a unique automation solution for high-mix/low-volume and/or mid-volume with frequent changeovers on round workpieces often associated with Nakamura lathes,” says Zach Spencer, Methods’ automation manager. “As Methods provides the machine, the options, the automation system, and the interface, along with the installation, training, and support, customers have the advantage of working with one supplier for the entire technology and experience stack.”
Turn-Assist features an open-floor setup and area sensors to maximize operator safety and accessibility, while a pre-programmable Fanuc robot loads blanks and unloads finished parts from the stocking table. Options allow the robot to process shafts, rotate parts, and interface with a bar-feeder.
The integrated, automatic air blow nozzle on the dual, three-jaw gripper enables the robot to discard chips and coolant away from the workholding, further streamlining operations without manual intervention.
Methods Machine Tools Inc.
https://www.methodsmachine.com

Next-gen vertical honing machines
The SV-3000 series vertical honing system features a Beckhoff-based industrial control with proprietary Sunnen2 software, designed to include EtherCAT industrial communication for fast response time and increased process control.
The control system includes a touch screen and capacity to program custom part load/unload operations, eliminating the need for a second control for automation. Through the touchscreen, operators can make intuitive adjustments of spindle speed, stroke rate, and tool feed during the honing cycle. Tool selection, setup mode, handling, and expansion/retraction of tools are all adjusted via touchscreen. A handwheel may be used for stroke adjustment.
The SV-3000 series incorporates synchronized servo stroke and spindle motors that enable constant crosshatch finishes the length of the bore, eliminating crosshatch angle flattening at stroke-reversal points which is important in cylinder wall applications where optimal piston ring sealing and performance is required. The drive technology includes a load-sensing feed system that maximizes productivity and produces 0.00025mm (0.000010") tolerances on a range of small-diameter parts.
Sunnen solicited input from global customers during the 2-year design and development of the SV-3000 series. The software was re-written using the latest programming languages and technologies and all programming was done by Sunnen software engineers who understand the honing process, with no code outsourcing. The intuitive nature of the control means new operators can be trained to process complex or difficult-to-hone parts, reducing setup time. In addition, the latest ergonomic and safety features have been incorporated. Guarding is designed to provide access to critical areas for machine maintenance, while a rear-mounted electrical enclosure and removable side panels allow improved access to the spindle and column from all sides. A centrally mounted operator station can be positioned to suit the operator’s preference and/or shop-floor space.
The SV-3000 uses OPC, an industrial communication standard that enables data exchange between multi-vendor devices and control applications without any proprietary restrictions, allowing real-time remote process monitoring, an important consideration for the implementation of Industry 4.0. Sunnen Products Co.
https://www.sunnen.com
Laser solutions for marking, traceability
Datamark FL series laser markers offer precise, repeatable, non-contact marking of metals, alloys, and most plastics. Available with Q-switched and MOPA fiber laser sources from 20W to 50W, these systems are capable of high-contrast annealed heat marks with no surface disruption and crisp engraving of basic text and complex patterns at depths exceeding 0.004".
The markers can be mounted in open Class 4 workstations or Class 1 safety enclosures, with a programmable Z-axis, optional rotary D-axis, and integrated barcode reading and verifying technology. They easily integrate into robotic cells, production lines, and other engineered solutions to support modern manufacturing environments.
Every system ships with the Datasoft Pro Windows software suite, supporting easy logo import, serialization, date coding, Data Matrix and QR codes, UID and UDI syntax, and arc marking. With an icon-based, what you see is what you get (WYSIWYG) interface, the software puts the tools to meet your marking requirements at your fingertips.
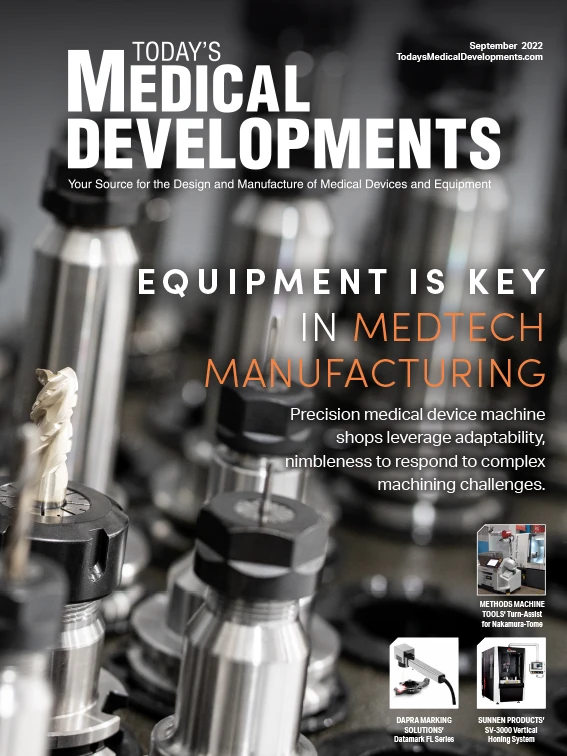
Explore the September 2022 Issue
Check out more from this issue and find your next story to read.
Latest from Today's Medical Developments
- Kistler offers service for piezoelectric force sensors and measuring chains
- Creaform’s Pro version of Scan-to-CAD Application Module
- Humanoid robots to become the next US-China battleground
- Air Turbine Technology’s Air Turbine Spindles 601 Series
- Copper nanoparticles could reduce infection risk of implanted medical device
- Renishaw's TEMPUS technology, RenAM 500 metal AM system
- #52 - Manufacturing Matters - Fall 2024 Aerospace Industry Outlook with Richard Aboulafia
- Tariffs threaten small business growth, increase costs across industries