
High production and labor costs, combined with rapid technological change, often cause manufacturers in developed countries to take their production offshore to lower costs.
Dr. Kathryn Stecke, Ashbel Smith professor of operations management at the University of Texas at Dallas (UT Dallas), recently studied the seru production system that electronics manufacturers use to create an exception to this trend.
Seru is a cellular assembly approach, used by companies including Canon and Sony, for manufacturing in dynamic, high-cost markets, Stecke says.
“Seru is like going back to trade manufacturing, before Henry Ford’s assembly line innovation. A focus is on extremely highly trained workers, emphasizing both speed and quality,” says Stecke, who teaches operations management and flexible manufacturing strategies in the Naveen Jindal School of Management at UT Dallas.
Seru cellular manufacturing allows rapid configuration of cells for assembly, packaging, and testing rather than only fabrication.
Highly skilled and flexible workers provide responsiveness required by changes in demand and fast development of an innovative product. The strategy also prioritizes responsiveness over cost reduction.
The study analyzed Canon’s and Sony’s histories, the factors that led to the development of seru systems and their successful implementations.
The researchers studied nine sites of Sony and Canon; interviewed managers at both companies; participated in industrial seminars and meetings; and reviewed company documents, handbooks, and published research.
Seru is not new, Stecke notes. A 1992 Wall Street Journal article discusses the system, but most of the world outside of Japan has not been aware of this electronics assembly innovation.
“Many companies in Japan, mostly electronics, have applied seru to improve productivity, quality, efficiency, and flexibility,” Stecke says. “Seru is an example of production remaining competitive in a high-cost environment.”
For example, the production of Sony’s PlayStation 2 console was moved from an assembly line of 19 workers in a 700ft2 space to a set of serus staffed by 10 workers in a 484ft2 space. The total cost of production was reduced, and PlayStation 2 volume increased 200%.
The study found that competitiveness and productivity increase when the focus is on using precisely the resources needed to respond to actual customer demand.
“Although seru mostly has been used in electronics, its use can be expanded to other appropriate industries,” Stecke notes. “Non-electronics companies currently using seru production systems include Denso and Yamasaki.”
University of Texas at Dallas
www.utdallas.edu
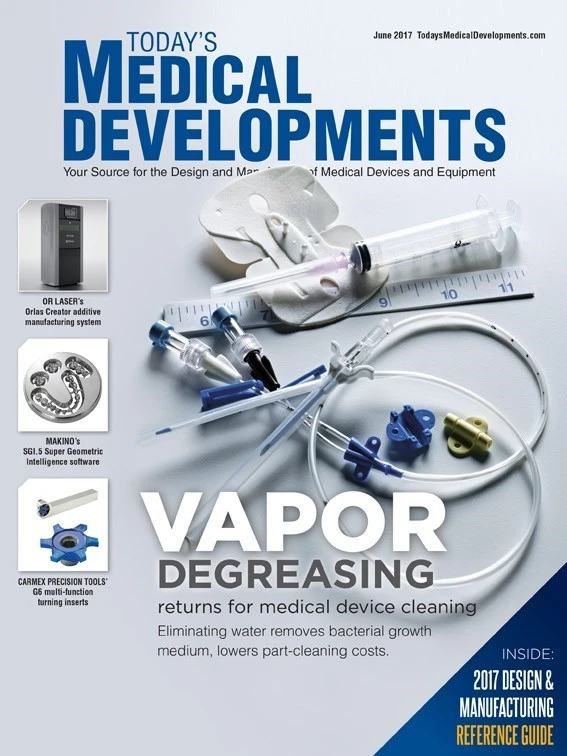
Explore the June 2017 Issue
Check out more from this issue and find your next story to read.
Latest from Today's Medical Developments
- The manufacturing resurgence is here – are you ready?
- Workholding solutions for your business
- ZOLLER events will showcase the company’s cutting-edge innovations
- THINBIT’s MINI GROOVE ‘N TURN Acme threading inserts
- CMMC Roll Out: When Do I Need to Comply? webinar
- Metabolic research uses Siemens gas analyzers to deliver results with 99.9999% resolutions
- Mazak’s SYNCREX 38/9 Swiss-type production turning machine
- Current economic and geopolitical realities demand decisive action