Economical, efficient magazine bar feeder

The Scout 320 magazine bar feeder is for feeding round, square, and hexagonal stock of various diameters, up to 12ft lengths, into CNC lathes. Heavy-gauge structural steel ensures rigidity and long-term durability, and a two-pusher system reduces the length of the unit by as much as 4ft. A short pusher pre-feeds the bar then retracts while a second full-length pusher lowers into position to continue the feeding process. A toothed belt accurately, smoothly, and quietly propels the double-pusher system.
A standard synchronization device for Swiss-style lathes employs an electro-magnetic coupling, mechanically linking lathe headstock Z-axis travel to the bar feeder’s pusher for synchronous movement and no loss of connection between the bar stock and pusher collet.
Dual anti-vibration devices stabilize the bar stock at two critical points between the guide channel and lathe spindle maximizing rpm potential. The adjustable roller design offers support and easy set-up of all bar diameters, eliminating multiple bearing blocks.
The Scout 320 features a 3mm-to-20mm bar diameter capacity with hydrodynamic quick-change polyurethane guide channels. An extruded aluminum case surrounds the polyurethane guide channels, increasing strength and stability. The channel is flooded with oil, creating a hydrodynamic effect supporting the rotating bar and offering the ability to run at higher rotations per minute with reduced noise and vibration. Profiling of the top guide channel accommodates various bar stock sizes. The U-shaped bottom guide-channel sections slide out of the base, so when changing channel size users insert a new section tighten a screw, and the Scout is ready to run a different diameter.
The Scout 320 features a remote control pendant with a Mitsubishi control and servo drive. Functions include manual and automatic operation, manual load/unload of bar stock for set-up and/or changeover, movement of bar pusher, and emergency stop. Programming parameters are set through F functions. Alarms are well defined and displayed on the operator control panel.
Edge Technologies
Generate, manage machining process

The NCdoc add-in component of NCSimul Machine simulation software enables users to automatically document all elements of a machining process. This reduces errors and enhances communication within a manufacturing organization.
Using data from the final version of the CNC machining program, as verified by NCSimul Machine, NCdoc generates a full machining report with data sheets for tooling and setup characteristics, details of the machining process, operational instructions and checklist information, and dimensional inspection checks including nominal values and associated tolerances.
Real-time documentation enables in-process checks. Clear presentation and easy access to accurate dimensional and operational information minimizes the possibility of errors resulting from misinterpretation or outdated data. Through the NCSimul Player Synchro feature, operators and other personnel can access instructional and other data sheets at the machine in synchronization with the current machining cycle.
Users can edit documents in one click, and a smart wizard for data sheet editing features automated input and collection of machining simulation data including 3D representations, cycle times, and cutting conditions.
SPRING Technologies
Expanded gear milling cutters

Standardized gear-milling cutters for DIN 3972 gear teeth that fall into the reference profile 1 category now cover modules 0.5 to 4. Between modules 0.5 and 3, AS45-grade carbide circular milling cutters from the 613 to 636 ranges are seated by an axial screw through the face side and available with a variety of diameters. Six teeth around the circumference ensure productivity, even when faced with high-strength materials.
Between modules 3.25 and 4, single-row and two-row cutter heads use standardized two-edged S279 indexable inserts. The axial screw connection for the indexable inserts enables high numbers of teeth and a narrow pitch. The indexable inserts are precision ground around the circumference and on the face. In cases where fewer teeth are present on the gear wheel, a two-row cutting division is used; this also applies to wider tooth profiles. Because of the cutting division, the two-row version of the indexable inserts exerts less cutting pressure on the tool, the workpiece, and the machine, improving results.
Horn USA Inc.
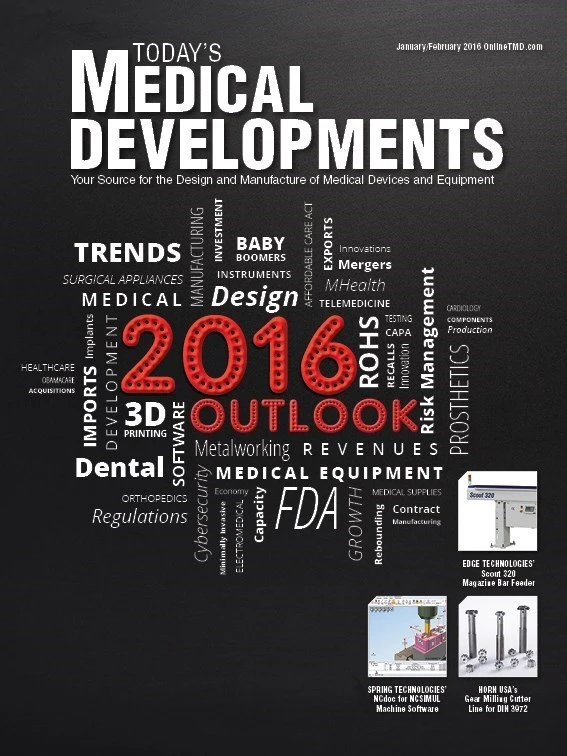
Explore the January February 2016 Issue
Check out more from this issue and find your next story to read.
Latest from Today's Medical Developments
- Best of 2024: #5 Article – Accelerating medical device development with freeform injection molding
- Best of 2024: #5 News – Complexity, the enduring enemy of medical cybersecurity
- Best of 2024: #6 Article – Closing the global product information gap
- Best of 2024: #6 News – NUBURU enters medical device market with order Blueacre Technology
- Season's greetings
- Best of 2024: #7 Article – Synchronized machining processes for medtech
- Best of 2024: #7 News – 3D printing could revolutionize treatment for cataracts, other eye conditions
- Best of 2024: #8 Article – Perfecting the CMP process for surgical blades