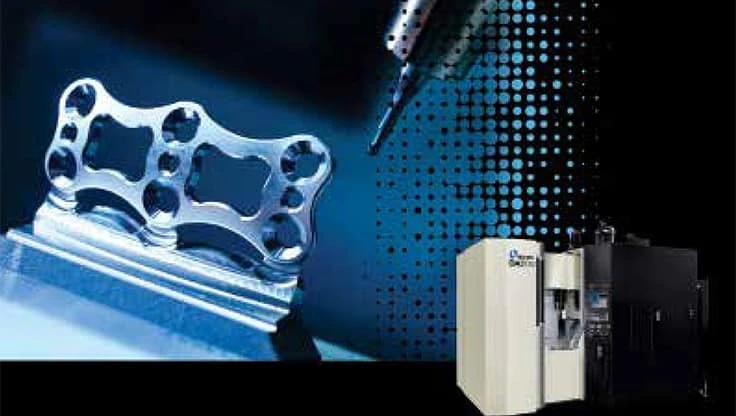
Makino

1. What is involved with operating a 5-Axis machine versus a 3-Axis machine?
It is common for there to be some anxiety over the implementation of 5-Axis equipment in a shop. However, thanks to machine control options built for 5-axis, the general operation of the machine does not differ much from 3-axis operation. Troubleshooting, however, can be different due to 5-axis options and more complex than 3-axis mainly due to the intricacy of the part and the fact that you have more machine components in motion.
2. What are some of the challenges with production on 5-Axis machines in medical manufacturing?
A common challenge is using a “4 UP” fixture, which is a 5-axis work-holding that puts four parts in the work area. Processing and operator intervention can be complex without adding engineering on the program side. These parts tend to be intricate, so it is paramount to simplify the human interaction with the process and programs to make them as user-friendly and as safe as possible.
Maintaining/checking the center of rotation is another challenge. The center of rotation is critical to the accuracy of parts machined on a 5-Axis machine. There are automated ways of checking the centers of rotation such as with Makino CRAM. Makino CRAM (Center of Rotation Axis Measurement) is a one-touch function that uses the probe and supplied artifact to accurately measure and maintain the centers of rotation.
3. What can be done to maximize cut time and safety on our 5-Axis machines?
One solution is being able to simulate the G-code program and process offline. This can provide a seamless way to make sure “everything works” before taking a machine out of production for the first part runoff.
Makino 5-Axis machine tools have verification software running on the control as a last line of defense. This software is called Collision Safe Guard (CSG). CSG gives the user the ability to accept Vericut CAS files to load a 3D-rendered project complete with fixtures, cut stock and tool library. This can help to ensure maximum safety and up time of the machine.
4. What tooling should be used?
You are only as good as the weakest link in your process. High-end machines with sub-par tooling and holders will result in a deficiency of tool life, cycle time, part quality and attainable accuracies. I always recommend premium tools and tool holding that will enable the best flexibility and performance of the machine tool.
Metric solid carbide tooling manufacturers use mostly 4mm and 6mm shanks for everything 6mm and under. Using metric tooling can make holder/collet selection much easier and require less inventory than imperial holders/collets.
5. How important is engineering support after the purchase?
Engineering support is a vital differentiator between success and failure. Having access to engineers who can provide insight for programming, processing and the above topics will ultimately lessen the time it takes to realize the full potential of your 5-Axis equipment. It’s why Makino and SST have application engineers dedicated to supporting the medical industry.
FOR MORE INFORMATION: https://www.makino.com
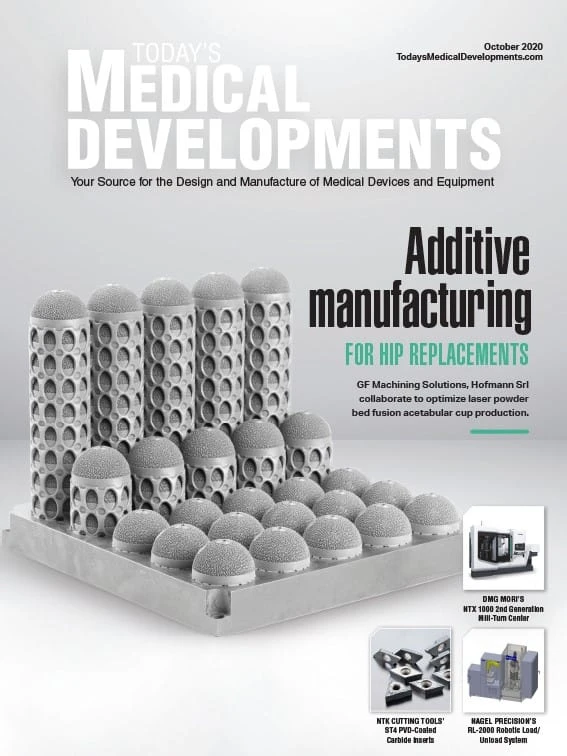
Explore the October 2020 Issue
Check out more from this issue and find your next story to read.
Latest from Today's Medical Developments
- MedTech Innovator welcomes five new industry partners
- First Article Inspection for quality control
- The manufacturing resurgence is here – are you ready?
- Workholding solutions for your business
- ZOLLER events will showcase the company’s cutting-edge innovations
- THINBIT’s MINI GROOVE ‘N TURN Acme threading inserts
- CMMC Roll Out: When Do I Need to Comply? webinar
- Metabolic research uses Siemens gas analyzers to deliver results with 99.9999% resolutions