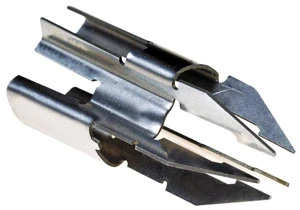
"If they need it quick, they call on us," notes Dave Brown, Vice President of Lyons Tool and Die Company. "Difficult parts with short lead times are our specialty." His manufacturing facility in Meriden, CT is often called upon to participate in the development of components or assemblies that others choose to steer clear of.
"Our par ticipation often begins with the review of a design concept proposed by the customer," adds Brown." Our engineering group reviews the application and makes recommendations that may reduce cost, improve manufacturability, or improve the performance of the device or assembly."
Lyons serves manufacturers in diverse industries from medical to aerospace. The manufacturer's capabilities include peecision metal stamping, rapid prototyping, CNC machining of complex parts, production wire EDM, component assembly, and overall project management. The FDA-registered company also has class 10,000 cleanrooms for the packaging and assembling of medical devices and implants.

Produced in quantityfrom metal sheets, thiscomponent is profiledon a FANUC wire EDMmachine.
Lyons produces a wide range of tooling for its internal stamping operations, including progressive dies (steel and carbide), coining dies, compound dies, progressive eyelet dies, progressive compound dies and secondary dies, as well as a variety of tooling for its rapid prototyping department. Stampings are done not only in metals such as stainless steel, titanium, aluminum, beryllium, brass, copper, bronze and carbon steels, but also in engineered plastics and composites including Kapton, Mylar, Teflon and other insulating materials.
In 2005, Lyons purchased a new FANUC 1iC 12-in. wire EDM machine — its third FANUC EDM — through Young Machine Tool, the local dealer for Methods EDM, which is a division of Methods Machine Tools Inc. Lyons uses its three machines (often around the clock) to make precision tooling components for its stamping operations, to produce prototype components for its growing customer base, and to perform secondary operations on production parts such as stainless steel tubing.
For one customer, an OEM medical device provider, Lyons turns out up to 50,000 parts every year, utilizing the FANUCs in a precision secondary operation to create a specialized cutting edge. "The part is a blade for a disposable surgical device," Brown explains. "The customer informed us that the cutting edge was meeting or exceeding the requirements for the device, from both a functional standpoint and a cost standpoint."
With exceptionally fast cutting speeds, an extremely reliable auto wire feed system, and a power ful CNC, FANUC wire EDMs are available in five models with Z-axis heights to 16 in. They provide exceptional accuracy and surface finishes and come standard with anti-electrolysis power supplies, digital servo systems, nano interpolation, linear glass scales, high-pressure flushing, chiller units, quickchange cartridge filtration systems, and remote monitoring capabilities.

In addition to medical devices, Lyons provides contractmanufacturing of precision components for various industries.
Noncutting time is minimized and productivity is increased by FANUC's Auto Wire Feed (AWF) System, which anneals, cuts, moves to a new location, threads and begins discharging (spark-to-spark) in just 10 seconds. It can thread 0.01 in. diameter wire through a start hole as small as 0.015 in. while the workpiece is submerged. A 35-pound wire spool allows the completion of complicated jobs with longer run times.
"The new machine is everything we wanted," says Brown. "These FANUC wire machines help make Lyons one of the fastest prototyping houses in the country. We're very impressed with their quality and ability to hold very tight tolerances. We pride ourselves on being able to make very difficult parts, and the FANUC wire EDM is one of the precision tools we use to produce these parts. Often a customer comes to us with a part that, in production, will require tooling costing anywhere from $10,000 to $500,000. Prior to making this investment, customers often call upon us to produce prototype parts utilizing our FANUC wire EDMs and other rapid-prototyping equipment. We can make a dozen parts in days as opposed to weeks, depending on the complexity of the job. These parts allow the customer to test the component or device without a huge initial investment. And then when they finally do decide to invest in production tooling, they know that the component meets the functional requirements of the assembly."
For one medical device customer, Lyons produced a short run of just 5,000 parts on the EDMs. Each machine was loaded with specially configured stacks of material, then set to run unattended through the night. Upon completion of the EDM operation, Lyons' prototype technicians put a complex series of bends into each part prior to providing the customer with the finished components.
Lyons has significantly expanded its capabilities through alliances with trusted subcontractors. The company can now manage a project from conception to finished parts. Subcontracted services include plating, coating, casting, laser/electron beam welding, laser cutting, plastic injection molding and metal injection molding.
Although performance was the main reason Lyons chose to buy its first FANUC EDM about seven years ago, it was not the only reason. "Frankly, we felt it was the best value for the price," Brown recalls. "Also, the service we get from Methods has been consistently good, and that was definitely a factor in our decision to stick with FANUC for our next two EDMs. Training from Methods has been very effective. FANUC continues to improve the various features of the machines. The installation of the new machine went extremely well."
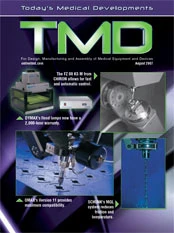
Explore the August 2007 Issue
Check out more from this issue and find your next story to read.
Latest from Today's Medical Developments
- LK Metrology acquires Nikon Metrology’s laser scanning and Focus software assets
- Flexxbotics’ robot compatibility with LMI Technologies 3D scanning, inspection products
- IMTS 2024 Booth Tour: Behringer Saws
- UNITED GRINDING Group to acquire GF Machining Solutions
- Mitutoyo America’s Metlogix M3 with the Quick Image Vision System
- IMTS 2024 Booth Tour: Belmont Equipment & Technologies
- Krell Technologies launches Photonics Outreach Program
- Hurco’s TM8MYi lathe