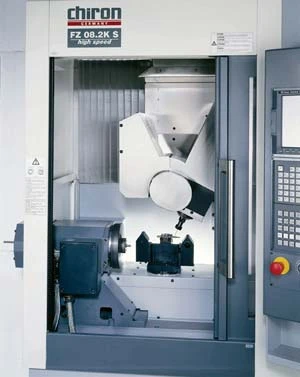
Sometimes designing a new device is the easiest part. Machining it can be the real challenge.
Recently Lares Research of Chico, Calif. found itself presented with a real challenge in looking to keep production of its adjustable spray coupler assembly in house rather than outsourcing it. "For us, it was less about economic and supplier issues and more about wanting to produce the complete assembly in house to maintain control," says the company's manufacturing manager. Charles Elton. The 50-year-old company manufactures air-driven high-speed dental hand pieces -- popularly thought of as a dentist's drill -- and dental laser systems for gum surgery and tooth cutting. Lares annually sells 20,000 units directly to dentists in the U.S. and through dealers in 48 other countries. It also produces private label brands for companies in the U.S. and France. When attached to its hand piece, the coupler Lares developed delivers drive air and exhaust passages, cooling water, atomization air and a lighting system. The challenge was how to make the coupler body efficiently and accurately. All of its functions are housed in a coupler body that's approximately 2-in. long by 0.625- in. in diameter at its widest end. The wide end has six small holes at different angles that step down to even smaller offset holes down the entire length. At first in order to produce the coupler, Lares machined a turned stainless steel blank on a 4-axis CNC milling machine in eight different setups. Understating the problem, Elton notes, "It's a complex part to say the least. Refixturing several times was necessary to get all the holes in the right position. We'd put multiple parts on each of the eight fixtures at one time to be somewhat efficient and smart. Some features of the part were impossible to measure without destroying the part to access the feature. Errors were often discovered after processing was complete resulting in 50% scrap." For the manufacturer, scrap was costing $36,000 a year. Although the company was able to improve manufacturing somewhat by putting all eight fixtures on two machines running simultaneously, there still were problems. There remained issues with tolerances between fixtures and in some instances Lares was drilling to a depth of 26X the diameter in a 0.052" diameter hole that only had about 0.003" location tolerance from another hole. Success brought stress. Lares introduced the new hand piece and it was an immediate triumph with orders from dentists and a private label company ordering 500 units. The manufacturer realized that it couldn't satisfy its customer's orders using the old machining process. "We had to make that coupler body more effectively," says Elton. "We had to maintain our on-time deliveries. We needed a solution yesterday." Along with his colleauge, Manufacturing Engineering Manager, Larry McCulloch, Elton traveled the country going to trade shows seeking a solution to the manufacturing problems. They did find a 5-axis milling machine with a 2-axis tilting rotary table able to do one part at a time in one setup, but it just wasn't fast enough. Speed and price were problems too with a palletized system. Eventually they found a Chiron America CNC machining center, the FZ08 Magnum with an NC swivel head for full 5-axis machining. With a swiveling range from –20° to +115°, the machine takes only 0.5 sec. to swivel from 0 to 90°. In addition, the FZ08 was able to produce milled surfaces and holes at every angular position, including outer and inner contours, at a rapid feed rate of almost 3,000 ipm. Tool changes took just 0.8 sec., which is a Chiron standard. And, the FZ08's compact footprint was the right size for the Lares shop floor. The optional barfeed mechanism on the FZ08 was ideal for the manufacturer since it could produce the coupler completely in one setup. That posed a problem since the bar feed model had a 14- week delivery schedule. The Lares factory was still slowly producing the couplers, although almost a third of them were no good. Chiron's West Coast distributor, Spinetti Machinery, did offer a solution. immediately available but it didn't have a bar feeder. The units could be made if the manufacturer would continue to blank the parts on its turning center. Lares leased the machine and it was on the factory floor within weeks. Although the machine was fast enough without the bar feed, Lares did run into some limitations. Although a 40-tool magazine is optional, the model Lares received didn't have the larger magazine. "We needed a 40-tool magazine and our machine had 24," explains McCulloch. "Our programmer suggested design changes to reduce the tool count. The changes made the 24-tool magazine viable." The FZ08's cycle time of 10 minutes was several seconds less than time studies conducted by Chiron. Additionally, Lares has found places where even more time could be saved by reconfiguring some programming sequences and the tool arrangement. The overall quality of the coupler body, particularly the holes, is at a much higher standard than previously achieved. In addition, McCulloch points out that, "Using a highspeed spindle with high-pressure through-coolant, in combination with a very rigid machine, has reduced the deburring operation significantly." A major benefit for Lares is the ability to maintain its reputation for delivering high quality products in a timely fashion to its customers. Chiron America, Inc. Charlotte, NC chironamerica.com

Explore the September October 2006 Issue
Check out more from this issue and find your next story to read.
Latest from Today's Medical Developments
- HERMES AWARD 2025 – Jury nominates three tech innovations
- Vision Engineering’s EVO Cam HALO
- How to Reduce First Article Inspection Creation Time by 70% to 90% with DISCUS Software
- FANUC America launches new robot tutorial website for all
- Murata Machinery USA’s MT1065EX twin-spindle, CNC turning center
- #40 - Lunch & Learn with Fagor Automation
- Kistler offers service for piezoelectric force sensors and measuring chains
- Creaform’s Pro version of Scan-to-CAD Application Module