
Patients suffering from traumatic injuries, birth defects, cancer, and strokes often can’t wait long for cranial or facial reconstruction surgeries, so time is always a factor for Kelyniam Global Inc., a Canton, Connecticut-based manufacturer of custom prosthetics, specifically cranial and maxillo-facial implants. Kelyniam offers 24-hour turnaround on all implants, a necessary capability given the often critical, life-saving, time-sensitive need for such procedures.
The short turnaround time greatly reduces time between trauma and implantation, minimizing scar tissue and bone remodeling and shortening hospital stays.
“The fastest implant we’ve ever done was in less than two-and-a-half hours,” says Tom McDonald, CNC manufacturer at Kelyniam. “The CT scan from the surgeon came in, the engineer designed it, I machined it, and we got it ready to ship.”
Kelyniam’s Food and Drug Administration (FDA) approved integrated fixation system (IFS) tabs save even more time during surgery. Normally, surgeons must apply additional hardware to an implant, such as titanium dog bones, to attach it to the skull. Kelyniam’s IFS is built into the implant, so surgeons can simply screw it in place, saving time and eliminating fixation hardware. All implants are custom-made, so the surgeon can position the tabs wherever needed.
“We’ve heard from some doctors that it’s taken them longer to prepare for a surgery than it does to put our implant in,” McDonald adds.
Machining challenges

Kelyniam manufactures one-piece and multi-piece implants, depending on the patient. Two-piece implants are ideal when surgeons need to install an implant on each side of the head and for large, thick, or curved pieces that would not be implantable as one piece. When doctors place two-piece implants next to each other, a lap joint connects the pieces for more stability. Complex multi-piece implants can be difficult to machine, but Kelyniam embraces the challenge.
“One of the most complex implants we’ve done is a three-piece implant for part of a patient’s skull, eye, and just below the eye,” McDonald says.
In addition to multi-piece implants, orbital pieces present a unique challenge. The implant has to be lined up in a CAD program, and the fourth axis must be turned several times to reach every area on the implant.
“Orbital cases are always very difficult, and they usually require multiple programs to get everything you need,” McDonald explains.
Manufacturing process

With four people working alongside McDonald at the Canton facility, operations run quickly and smoothly. Once a CT scan comes in, the engineer designs the implant using Mimics medical 3D image-based engineering software from Materialise. She then delivers the design’s STL file to the machinist, who loads it into RhinoCAM to create toolpaths and generate the G-code for Kelyniam’s Haas CNC milling machines.
Implants are manufactured in two stages – machining a surgical mold and machining the implant itself. Kelyniam machines parts using two sets of Haas Super Mini Mill vertical machining centers (VMCs), one set for each process. The Mini Mills are easy to maintain, have a user-friendly control system, include integrated fourth-axis rotaries, and a built-in hard drive enables machinists to upload programs.
The first set of VMCs machine the poly-vinyl chloride (PVC) surgical mold that confirms implant fit and function. The machine features a Haas HRT160 rotary, and an attached tailstock holds the workpiece as it is machined on both sides.
The second set of Haas centers – modified for dry machining – machine the implant from polyether ether ketone (PEEK), a lightweight biomaterial that is easier to machine than titanium and other common implant materials. Fourth-axis machining of both sides of the implant eliminates manually flipping the workpiece. With cycle times up to 90 minutes per implant, the ability to machine both sides in a single setup has increased productivity 30%.
“All four of the machines are set up basically the same – same tools, same 4-axis system,” McDonald says. “So you can go from one machine to the other if you need to. And, if there’s ever a situation where one machine breaks down, you can take parts from one machine and bring them over to the other.”
Going the extra mile
Once finished, an implant is usually shipped directly to the surgeon. However, in cases where time is critical, a Kelyniam employee has hand-delivered implants, flying or driving with the device to the location of the surgery. Kelyniam has hand-delivered implants across the country, most frequently to Boston, Massachusetts.
“There have been several times where we’ve made an implant at night and Boston Medical needed it the next morning. So, I’d drive over to the Boston area and deliver the implant,” McDonald says.
Kelyniam’s design engineer, Rebecca Miles, has also made implant delivery trips. In one situation, she took a new implant right off the VMC, jumped on a plane to Houston, Texas, dropped off the device, and flew back in the same day.
“If we needed to do it, we did it, because we can,” McDonald says. “We’re very conscious of our work and take it seriously. And we really like to hear good news from the surgeon at the end.”
Haas Automation Inc.
https://www.haascnc.com
Kelyniam Global Inc.
https://www.kelyniam.com
Materialise NV
https://www.materialise.com
MecSoft Corp. (RhinoCAM)
https://mecsoft.com
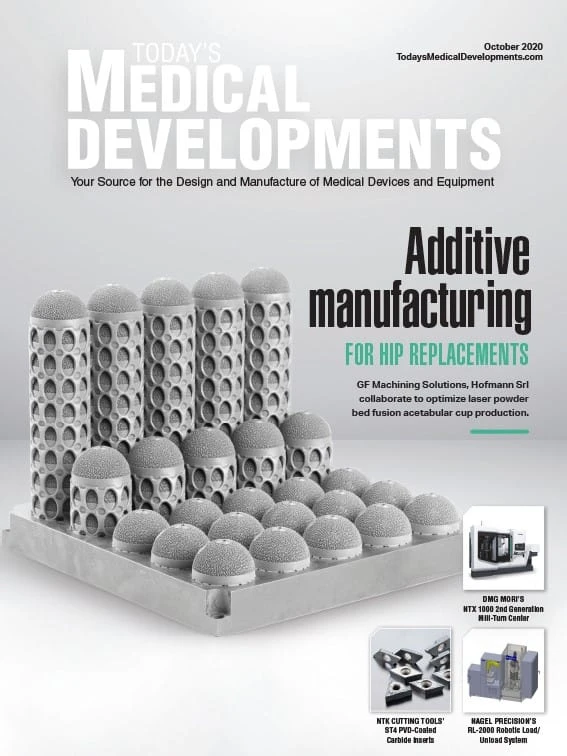
Explore the October 2020 Issue
Check out more from this issue and find your next story to read.
Latest from Today's Medical Developments
- STUDER looks back on a solid 2024 financial year
- HANNOVER MESSE 2025: Tailwind for industry
- Find out the latest developments in tool path strategies for machining
- Building, maintaining the Navy’s next generation of maritime platforms
- Pioneering battery-free cardiac implants
- KBC Tools & Machinery marks its 60th anniversary, Founder’s Day
- Address the challenges of machining high-temperature aerospace components
- Elevate your manufacturing operations with April’s Manufacturing Lunch + Learn