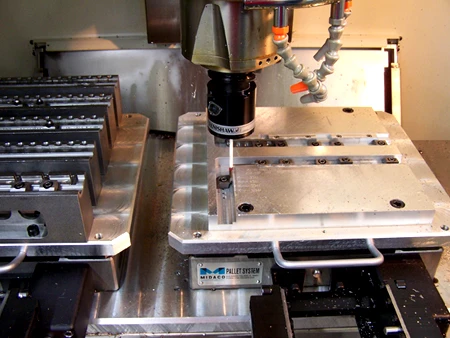
Probing equipment remedies high scrap rates for medical parts manufacturer
Colorado Springs' Tech Machine has relied heavily on the skills of its machine operators to generate quality parts. However, as it continued to win difficult medical work, the scrap rate continued to climb, sometimes reaching the 50% range, mainly because intricate part geometries made fixturing difficult. That's when David Wiggans, Tech Machine's owner, made the commitment to master the technology of probing and build his operation around it.
"If a probing routine takes 30 sec. and saves me from ruining one part in a family fixture, it is well worth it," comments Wiggans. "If you have a 20 min. cycle but must scrap the part, probing routine time is immaterial, because now it will take 40 min. to make a good part.
Wiggans began implementing the probing system two years ago. Now each of the 13 vertical machining centers (VMCs) in the shop operates with a probe program. "The probing system, based on a pallet fixturing system and Renishaw machine tool probes allows us to operate at one-fourth the labor, while producing higher volumes of work, thanks to quicker, more accurate setups," says Wiggans. "Our machines won't cut a chip until the probing system verifies the batched parts are properly fixtured and all necessary offsets are calculated. As a result, the scrap rate has gone down from as high as 50% on some parts to virtually zero on everything."
His first probe, a Renishaw MP12 touch-trigger probe, came with a Fadal VMC he purchased. "We had a vision of implementing probes into our system but we were not familiar with probing routines," explains Wiggans. "At the outset, I didn't believe the numbers coming off the probe. I simply didn't trust the data. So I actually ran a 1,000 cycles, recording all the data in variables. And all the readings were within 0.0001-in," recalls Wiggans. "We ran tests on eight different fixtures. It took 30 sec. to probe the part. On one row of parts, we saved 10 hr. And when we were finished, we had a whole row of good parts."
According to the company, the high-dollar stainless and titanium medical parts have extremely intricate contours and geometries, requiring tolerances to 0.0001-in and super-smooth finish. Probing ensures the machine knows exactly where the part is located on the fixture.
The probes are used to pick up difficult part geometries and adjust offsets, as well as I.D. devices that define parts and pallet fixtures. The probing process begins by having the Renishaw probe identify the multiple-part pallet loaded onto the machine bed. The probe then identifies the part type and size as well as its location in the fixture. With as many as 14 different part numbers running on each fixture, probing identifies the part number and its respective position to the fixture.
"Probing eliminates the use of very expensive, very accurate fixtures, costing from $10,000 to $150,000," says Wiggans. "We get by with inexpensive fixtures because the probe locates everything and compensates for uneven Z-axis depths before machining.
Another major component of the probing system is toolsetting with Renishaw's TS27R contact toolsetting probe. The probe is mounted on the table of each machining center and tools are brought to it for inspection. The toolsetting captures and compensates for variation with tools that may not be ground exactly the same and may have different Z-axis depths. "Using Renishaw toolsetting, tight bore depths are never a problem," states Wiggans.
Probing is also used to detect broken tools. After performing a cutting operation on one part, the tool is delivered to the toolsetter to check for breakage. If the tool is broken, the machine will replace it and move to the next part. Wiggans programs the system to remember which part broke the tool, so that the machine will skip that part on succeeding operations. This ensures that the only lost part is the one that broke the tool.
With the probes inspecting setups and checking tools, plus routine calibration with Renishaw's QC10 ballbar, the machines are virtually uncrashable, according to Wiggans.
"To us, a machine tool without a probing system is like a machine without a spindle – it's just not complete," says Wiggans. "The use of probes makes your machine so much more versatile and productive that you won't know how you did it before probing."
Renishaw Inc.
Hoffman Estates, IL.
renishaw.com
Circle 201
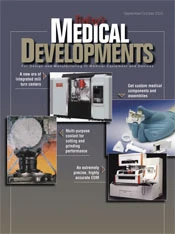
Explore the September 2005 Issue
Check out more from this issue and find your next story to read.
Latest from Today's Medical Developments
- Turnkey robotic systems are already behind the times
- You can still register for March’s Manufacturing Lunch + Learn!
- HERMES AWARD 2025 – Jury nominates three tech innovations
- Vision Engineering’s EVO Cam HALO
- How to Reduce First Article Inspection Creation Time by 70% to 90% with DISCUS Software
- FANUC America launches new robot tutorial website for all
- Murata Machinery USA’s MT1065EX twin-spindle, CNC turning center
- #40 - Lunch & Learn with Fagor Automation