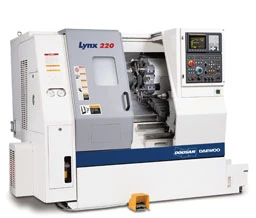
The new Lynx 220 features speed and power in an O.D. turning center. Three models are available, the 220A with a 6.5 in. chuck, the 220C with an 8.25 in. chuck, and a 220LC with an 8.25 in. chuck and elongated bed. All are powered by a 20 Hp motor that allows for heavy cuts through tough metals.
A 30° slant bed maintains a minimal and constant distance from tool tip to guideway, assures maximum rigidity, and eliminates deformation under heavy loads. The one-piece bed is ribbed and its fine-grain Meehanite composition dampens vibration and helps dissipate heat.
The spindle accelerates to its peak 6,000 rpm (Lynx 220A) in 2.3 seconds, with the large contact surface of the cylindrical roller bearings providing high rigidity for heavy loads and mirror finishes. All bearings are permanently lubricated, precision class P4. The 12 station, heavy-duty turret is non-stop and bi-directional, with a quick 0.15 sec. station index time. Its heavy-duty design, with a large 8.27 in. diameter curvic coupling, provides high rigidity, long boring bar overhang ratios, and extended tool life. Rapid traverses are 1,181 ipm on the X axis, and 1,417 ipm on the Z.
An integral tool setter minimizes the need for manual skim cuts, and a four-position touch sensor allows tool setting in any direction. Automatic forced lubrication is provided to all guideways, ball screws, and the tailstock quill. Nonclogging piston distributors minimize way lube consumption and the ½ gallon lubricant reservoir lasts up to 100 hours. Sensors activate a lowlevel alarm and monitor pressure to detect open or broken lube lines, while coolant is delivered through the turret from a 30-gallon tank by a 1.2 Hp multistage centrifugal pump.
The 65 psi of pressure flushes chips from drilled holes, often eliminating the need for time-consuming peck and drill cycles. Furthermore, the coolant tank and chip pan are separate from the machine bed, preventing heat transfer to the machine casting. A waylube separation system removes tramp oils from the coolant reservoir, and deposits it in a separate external tank.
Daewoo Machine Tool Division of Doosan Infracore West Caldwell, NJ infracoremt.com Booth #A-8131

Explore the July August 2006 Issue
Check out more from this issue and find your next story to read.
Latest from Today's Medical Developments
- Kistler offers service for piezoelectric force sensors and measuring chains
- Creaform’s Pro version of Scan-to-CAD Application Module
- Humanoid robots to become the next US-China battleground
- Air Turbine Technology’s Air Turbine Spindles 601 Series
- Copper nanoparticles could reduce infection risk of implanted medical device
- Renishaw's TEMPUS technology, RenAM 500 metal AM system
- #52 - Manufacturing Matters - Fall 2024 Aerospace Industry Outlook with Richard Aboulafia
- Tariffs threaten small business growth, increase costs across industries