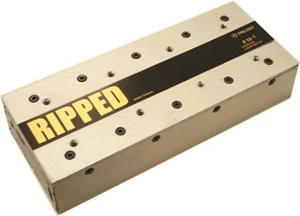
Linear motors complement today's linear motion technologies.
Today's linear motion applications are more demanding than ever before. Faster throughput, more exact positioning, longer life, less maintenance, fewer moving parts—the list is never ending. Motion control companies strive to meet and exceed these requirements by continual technological advancement.
Less than a decade ago, it was a difficult task to find a commercially available linear bearing that could travel 5 meters per second with straightness, load capacity and stiffness. Today, there are many linear bearings with these attributes and they are fairly cost effective
Advancements in linear encoder technology also allow for higher speed operation. Today's linear encoders and other devices are able to meet this challenge, are less noise susceptible and cost less.
So with two of the three primary linear motion elements rising to the high speed/high accuracy challenge, the limiting factor is the drive drain.
Improvements in linear, mechanical drives have also moved forward. Ball screws with higher accuracy and faster leads result in higher throughput. Timing belts have high repeatability and speeds of well over 5 meters per second. Both of these technologies have historically solved motion control applications, and will continue to do so. However, neither of these provide the speed and accuracy combination required by an increasing number of today's motion applications.
More and more we face the high accuracy/high speed application. To solve this, the drive train must be able to respond faster, have less wear and have extremely high resolution capabilities. A device that can provide this does exist—it is the brushless linear motor.
THE LINEAR MOTOR CONCEPT
The idea is simple enough. Take a conventional rotary servo motor and unwrap it. What was the stator is now the forcer and the rotor becomes a coil or magnet rail. With this design, the load is connected directly to the motor. Direct linear motion is achieved without any rotary to linear transmission devices.
Linear motor technology is not new; step motor and brushed linear motor products have been available for quite some time. Brushless technology is becoming increasingly popular as applications take advantage of its technology.
Brushed linear motors had the coils in the linear rail and the magnets in the forcer. Commutation was accomplished by a linear commutation bar that ran the length of the motor with brushes in the forcer. This method was both expensive and limited. The cost of winding multiple feet of linear motor rail was time and material intensive. High speed operation was limited due to commutation bar and brushes.
Linear step motors have both windings and permanent magnets with the forcer. It travels along a rail that has an etched tooth structure. While maintaining the step motor advantage of open loop operation, the technology does have some limitation in speed and available force.
With brushless servo motor technology and the supporting electronics to drive them, the above limitations have been eliminated. The forcer is now a set of windings while the stator is a rail of magnets. Commutation is done electronically either by Hall-effect sensors or sinusoidal. Hall-effect sensors located within the forcer are activated by the magnets on the rail. The amplifier translates these signals into appropriate phase currents. Sine commutation is accomplished using the linear encoder signals back to the controller. A common technique is the use of Hall-effect initially and then switching to sinusoidal commutation. In any case, the speed of commutation is not the limiting factor. The force generated by the same size motor is greater than brush motor technology due to improved magnet materials.
CHOOSING A LINEAR MOTOR
Choosing the right linear motor for an application is not a simple task. Selecting the right technology for the application, force calculations, thermal considerations, bearing loading, commutation methods, etc., must be considered.
Knowing the basic types and the associated advantages and disadvantages will assist in the end solution. Three technologies of brushless motors are discussed. They are: ironcore, aircore (ironless) and slotless.
IRONCORE LINEAR MOTO
Construction.
This motor takes its design from a brushless
rotary motor. The motor consists of a
flat iron rail to which rare earth permanent
magnets are bonded. The forcer is constructed
of laminations and coils wound
around the "teeth" of the laminations.
Thermal sensors are mounted internally to
the windings, sensing temperature. Hall-
effect sensors are either mounted in the
coil area or mounted on the edge of the
motor. These sensors are activated by the
magnets on the rail and are used for commutation
of the windings.
Advantages
Highest force per size: Utilizing laminations
to concentrate the flux field, this type
of motor produces the greatest force per
package size.
Lower cost / lower weight rail: The next type of motor we will examine is the AirCore motor. This design uses two sets of magnet rails. Since the magnets are expensive, these motors are more expensive than the IronCore design. Additionally, the magnet rail is heavy and when working with multi-axis systems, or if the motor is configured so that the rail is moving, the double set of magnets can be a serious performance limitation.
Good heat dissipation: Since the windings are wound around an iron lamination, heat dissipation is excellent. Additionally, cooling tubes can be routed through the laminations. These tubes can then have air or liquid forced through them, improving thermal management.
Disadvantages.
Normal attractive force: Since the forcer
is primarily made of iron, and the gap between
the forcer and the winding is normally
only 0.8mm, there is a very strong
attractive force between the forcer and
the rail. This force can be as much as 10
times the continuous thrust force of the
motor. If a motor has 100 lbs. of continuous
force, it may have as much as 1,000
lbs. of normal force pulling it toward the
magnet rail. This normal force must be
taken into consideration when sizing linear
bearings.
Cogging: Since the forcer is made of iron and it passes over magnets, there is a variation in the thrust force as it passes each magnet. This is referred to as cogging and optimized to minimize cogging by skewing magnets and by other techniques.
AIRCORE LINEAR MOTOR
Construction.
This design is referred to as AirCore or
Ironless. Two magnet rails oppose each
other, north and south. A spacer bar between
them keeps the two sides from
closing together.
The forcer is constructed of coils wound and held together with epoxy. This winding assembly is then topped off with an aluminum bar. This bar is used for mounting the load and also for heat removal. The winding itself has no iron in it, thus the names "AirCore" or "Ironless". As with the IronCore, thermal sensors and hall-effect sensors are mounted to the forcer.
Advantages.
No attractive forces: Because the forcer
contains no iron, no attractive forces exist
between the forcer and the rails. This
means no additional forces on bearings.
The motor is easier to handle and install
without these attractive forces.
No Cogging: With its ironless forcer, this style motor has no cogging. This is ideal in applications requiring extreme velocity control. This type of motor is normally used in conjunction with air bearings due to the air bearing's frictionless, ultra smooth characteristics.
Low-weight forcer: In applications that have very light payloads, low-weight forceres can be a benefit. Higher acceleration/ deceleration may be possible due to this lower weight, which results in higher throughput.
Disadvantages.
Structural stiffness: The forcer is made of coils and epoxy. The force is generated at the coil, meaning that all of the exerted force is on the windings and epoxy. This is a weak structure compared to the IronCore. This weakness limits the maximum sizes and the forces to which these types of motors can be manufactured without additional structural members being added.
Force per package size: Due to the thermal and structural limitations, the force per package size of this type of motor is low. The double rail design takes up additional space.
LINEAR MOTOR PROS AND CONS
Pros:
- High Speeds: The maximum speed of a linear motor is limited only by the bus voltage and the speed of the control electronics. Typical speeds for linear motors are 3 meters per second with 1 micron resolution and over 5 meters per second, 200ips, with coarser resolution.
- High Precision: The accuracy, resolution and repeatability of a linear motor driven device is controlled by the feedback device. With the wide range of linear feedback devices available, resolution and accuracy are primarily limited to budget and to control system bandwidth.
- Fast Response: The response rate of a linear motor driven device can be over 100 times that of a mechanical transmission. This means faster accelerations and settling times, thus more throughput.
- Stiffness: Because there is no mechanical linkage, increasing the stiffness is simply a matter of gain and current. The spring rate of a linear motor driven system can be many times that of a ball screw driven device. However, it must be noted that this is limited by the motors peak force, the current available and the resolution of the feedback.
- Zero Backlash: Without mechanical transmission components, there is no backlash. Resolution considerations do exist. That is, the linear motor must be displaced by one feedback count before it will begin to correct its position.
- Maintenance-free Operation: Because the linear motors of today have no contacting parts, there is no wear.
Cons:
- Cost: Linear motors are expensive. This is due to the relative low volume produced and the price of magnets. Since most linear motor designs mount rare earth magnets to the length of the rail, and the cost of these magnets is high, long travel motors become expensive. However, as the popularity of linear motors continues, volume will rise and cost will decline. This process has begun. Linear feedback must also be considered in the cost of using a linear motor. Rotary motor feedback is relatively inexpensive (<$100 list) and is not length- dependent. Linear motors typically require a linear encoder for feedback. These devices are many times more expensive than their rotary counterparts. A 100mm travel linear encoder lists in the neighborhood of $500, and cost increases with length. With newer reflective type encoder technologies, the manufacturing costs are declining, and with continued increases in the use of these encoders, prices will follow. Most importantly, if system accuracy requires linear encoder feedback, the cost differential between linear and rotary technology is greatly reduced.
- Higher Bandwidth Drives and Controls: Since there is no mechanical reduction between the motor and the load, servo response bandwidth must be faster. This includes higher encoder bandwidth and servo update rates.
- Force Per Package Size: Linear motors are not compact force generators compared to a rotary motor with a transmission offering mechanical advantage. For example, to produce even 65N of continuous force, a linear motor's cross section is approximately 50mm x 40mm. Compare this to the cross section of a 10mm diameter ball screw which produces 100 lbs of thrust, and one can see that linear motors are not brute force devices.
- Heating: In most linear motor applications, the forcer is attached to the load. Any I²R losses are then directly coupled to the load. If an application is sensitive to heat, thermal management techniques need to be applied. Air and water cooling options are popular and common.
- No (minimal) Friction: This may not seem like a problem, but it certainly can be. For instance, a linear motor is traveling at 3 meters/second and loses power. Without some resistance in the system, it does not take long before the motor reaches the end of stroke and mechanical stops.
SLOTLESS LINEAR MOTOR
Construction.
The rail is the same as those used for the IronCore design—simply a flat iron plate with magnets bonded to it. This unique forcer begins with a coil similar to those used in the AirCore. A backiron plate is placed behind the coil. This assembly is placed inside an aluminum housing with an open bottom. The housing is then filled with epoxy, securing the winding and back-iron into the housing. Thermal sensors are internal.
Advantages / Disadvantages.
Since the Slotless design is a hybrid between
the IronCore and the AirCore, the
advantages and disadvantages are really
comparisons between these two types.
Lower cost magnet rail: Since the same type of magnet rail is used as the IronCore (single row), this design also has a low cost magnet rail compared to the AirCore.
Lower weight magnet rail: As a single magnet rail is employed, the weight is less than half that of the AirCore. This means less load and higher throughput in multi-axis systems.
Structurally strong forcer: With the body of the forcer being made of aluminum and the windings being bonded to this housing, the strength of the forcer is much greater than that of the AirCore, thus reducing the possibility of motor fatigue contributed failures.
Light weight forcer: Although not as light as the AirCore, the Slotless design is much lighter than its equivalent IronCore. This results in higher throughput in light load applications.
Lower attractive forces: The Slotless design has a back-iron, causing attractive forces between the forcer and the rail. This attractive force is significantly less than that of the IronCore on the order of five or seven times the continuous force.
Lower cogging: With the larger magnetic gap between the magnet and forcer back-iron, the slotless design has lower cogging. This enables the Slotless design to operate in applications requiring good velocity control.
Heat dissipation: The Slotless design, with the coil resting across the back-iron, which is in direct contact with the aluminum housing, has very good heat transfer and is easy to manage.
Force per package size: The force per package size of this design is between the AirCore and the IronCore. Since the Slotless design has a very good thermal path, it is capable of handling higher currents than the AirCore design and thus generating higher forces.
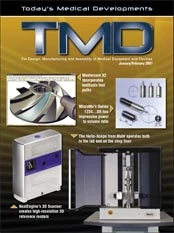
Explore the January February 2007 Issue
Check out more from this issue and find your next story to read.
Latest from Today's Medical Developments
- The role of robotics in precision medical device manufacturing
- Swiss Steel Group’s UGIMA-X machinable stainless-steel sets
- #51 - Manufacturing Matters - The Impact of M&A in MedTech 2024
- Visual Components: 25 years of simulation and programming software innovation
- Zimmer Biomet announces definitive agreement to Acquire Paragon 28
- Discover an innovative technology for EMI/ESD/TVS suppression
- Teleflex to acquire BIOTRONIK’s Vascular Intervention business
- Innovation at Global Industrie 2025