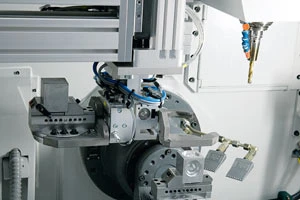
One thing's for sure: Whoever was able to reload his six-shooter faster was the boss in the Wild West. In the field of machine tool manufacturing, fast reloading - also known as retooling - is not at all easy, unless you have good ideas, as well as handling units that move the tools and the workpieces quickly.
Chiron manufactures precision machining centers and one, the FZ 08 CNC, is a compact series-produced machine with up to five axes for complete machining of small workpieces. As a standard feature, customers can use 12, 24 or 40 tools.
A single set of tools is usually not enough to machine complicated workpieces or larger families of parts.
"When we change over from one part to another, we also have to change the tool set. Furthermore, if a large mix of parts is also being produced, we end up with immense changeover costs," explains Matthias Giesler, production manager at Chiron. "Of course, we want to avoid any machine downtime associated with this process." In order to minimize this changeover time, Chiron has come up with a sort of "ammunition depot" for its customers.
In cooperation with Festo, a tool magazine with enough capacity for up to 400 tools was developed for the FZ 08. Not only did Festo supply the handling technology, but al so the ent i r e background magazine with toolholders. The required parts are purchased in accordancewith Chiron's speci f icat ions f rom their suppliers, and the complete tool magazine is delivered to Chiron on rollers. Chiron only needs to connect the magazine pneumatically or electrically, and insert the tools.
TOOL HANDLING
A planar surface gantry forms part of the background magazine that picks the tools and feeds them to the machine for the machining process. The gantry is equipped with a tandem solution in the horizontal plane, consisting of two DGE toothedbelt axes. In order to ensure ideal synchronous operation, the axes are coupled together by a shaft via a T-gearbox. Tools are withdrawn from the magazine in the vertical plane by means of a DGC pneumatic linear drive with intermediate position and gripper system.
The un-machined workpieces are clamped in a fixture. The fixture is located on a pallet that has been encoded with a chip where the machining data is saved. In this way, it is possible to load the entire pallet conveyor system with many different workpieces. The chip is read and the data is transferred to the controller at the transfer station.
Therefore, the machine is capable of flexibly changing over to various workpieces, autonomously, without setup expenses. Plausibility checks confirm that the pallet has been inser ted cor rect ly, and that no collisions occur. After the system gives approval, the gripper lowers the loader handling unit, grips the pallet with the workpiece, and advances it into the machine. It picks up the pallet with a finished part, if one is present, and sets down the pallet with the next blank to be machined.

Parallel gripper HGPL
In order to reduce machine changeover time, the loader handling unit is equipped with a double gripper.
The gripper arm is retracted with the finished part. The manufacturing process continues, and the gripper arm sets the finished part onto the pallet conveyor system.
The primary component of the loader handling unit is the HGPL parallel gripper attached to a DRQD semi-rotary actuator. The gripper's large opening stroke enables it to travel over the workpiece to grip it from below. The loader handling unit is advanced in the horizontal axis by two DGC pneumatic linear drives. One of these functions as a drive, and the other as an additional guide. A DGC pneumatic linear drive lifts and lowers the vertical axis, and an external clamping unit prevents the axis from sinking in the event of a pressure drop.
Festo Corp.
Hauppauge, NY
festo.com
Chiron America Inc.
Charlotte, NC
chironamerica.com

Explore the June 2009 Issue
Check out more from this issue and find your next story to read.
Latest from Today's Medical Developments
- Best of 2024: #5 Article – Accelerating medical device development with freeform injection molding
- Best of 2024: #5 News – Complexity, the enduring enemy of medical cybersecurity
- Best of 2024: #6 Article – Closing the global product information gap
- Best of 2024: #6 News – NUBURU enters medical device market with order Blueacre Technology
- Season's greetings
- Best of 2024: #7 Article – Synchronized machining processes for medtech
- Best of 2024: #7 News – 3D printing could revolutionize treatment for cataracts, other eye conditions
- Best of 2024: #8 Article – Perfecting the CMP process for surgical blades