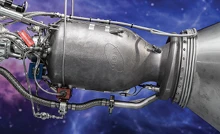
Photo courtesy of SLM Solutions and Orbex

Orbex has introduced the environmentally-friendly Prime, the largest metal rocket engine 3D-printed in a single piece on SLM Solutions’ SLM800. Founded in 2015, the UK-based spaceflight company develops small satellite launch vehicles and introduced Prime at the grand opening of its headquarters in Forres, Scotland. The Prime launcher uses 100% renewable fuel, cutting carbon emissions by 90% and a zero-shock staging and payload separation for zero orbital debris. Its design was optimized for selective laser melting (SLM) production, resulting in a structure 30% lighter and 20% more efficient than any other launch vehicle in its category.
Orbex aerospace engineers partnered closely with the applications engineering team at SLM Solutions’ Lübeck, Germany headquarters to ensure success when transferring the design into selective laser melting production. Applications Specialist Lukas Pankiewicz headed the consulting team inside SLM Solutions, developing parameters optimized for this geometry. Working with the design team at Orbex, Pankiewicz consulted on design features and orientation options to help ensure a successful part build with the required material properties and dimensional accuracy.
“Our aim during the process was to fulfill the quality expectations of the Orbex team, keep the functionality of the part, and make it suitable for additive manufacturing (AM),” Pankiewicz says. “Every single support structure used in data preparation has been customized to obtain the best quality in every section of the engine, taking post-processing into consideration as well.”
The SLM800 large-format metal AM system features a 260mm x 500mm powder bed that can build parts 800mm tall, allowing the Prime engine to be built of a special nickel alloy in one piece. The SLM800’s SLMHUB unpacking system integrates contactless powder handling and automated build chamber conveyors to transfer the finished part to an unpacking station to remove powder through vibration and rotation. Pankiewicz incorporated into the build a powder removal strategy with delivery channels to remove as much powder as possible while reducing material loss.

After production, SLM Solutions’ metallography lab analyzed reference samples built together with the engine to prove porosity level and distribution met quality acceptance criteria. The rapid iteration times inherent to the SLM process allowed Orbex to save 90% in turnaround time and more than 50% in costs compared to traditional CNC machining.
“This has always been what SLM Solutions is about,” says Dr. Axel Schulz, SLM Solutions’ chief sales officer. “Members of our team helped invent selective laser melting technology. We’ve always wanted that technology to succeed. SLM Solutions consulted Orbex on how to make the technology best work for them and transferred that knowledge to ensure successful implementation as they ramp up to production.”
SLM Solutions
https://slm-solutions.com
Orbex
https://orbex.space

Explore the Additive Manufacturing Guide Issue
Check out more from this issue and find your next story to read.
Latest from Today's Medical Developments
- Birk Manufacturing achieves ISO 13485 recertification
- SW North America's BA 322i twin-spindle CNC
- The role of robotics in precision medical device manufacturing
- Swiss Steel Group’s UGIMA-X machinable stainless-steel sets
- #51 - Manufacturing Matters - The Impact of M&A in MedTech 2024
- Visual Components: 25 years of simulation and programming software innovation
- Zimmer Biomet announces definitive agreement to Acquire Paragon 28
- Discover an innovative technology for EMI/ESD/TVS suppression