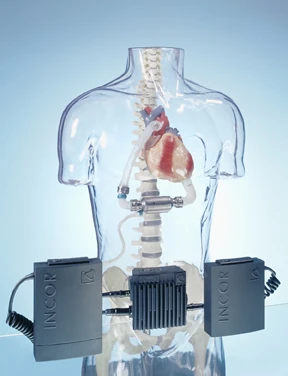
A variety of leak detection methods are commonly used in the manufacturing of medical consumables, medical implants, and medical instruments. At one end of the spectrum are various dry-air testing methods, in which an object is pressurized and isolated from the pressure source, and then monitored to detect any leakage, typically by observing a pressure drop. These dry-air methods can have significant shortcomings, such as limited sensitivity and accuracy, and the inability to determine the location of leaks. At the other end of the spectrum is the use of helium as a tracer gas, with specially designed mass spectrometers. The helium- based method is highly accurate and sensitive enough to detect leaks ten thousand times smaller than the leaks detected by the dry-air testing methods. However, helium testing has proven especially complex and expensive for all but the most demanding medical equipment applications.
The Hydrogen-based Method A relatively new technology, hydrogen leak testing overcomes the shortcomings of the dry-air testing methods, provides high sensitivity and accuracy, and costs significantly less than the helium method.
The hydrogen method employs a robust, self- calibrating and maintenance- free microelectronic probe that is extremely sensitive and 100% selective to hydrogen. The test gas (a non-flammable mix of 5% hydrogen and 95% nitrogen) is injected into the test object, and leakage can be detected in several different ways. The test object can be enclosed in an accumulation chamber, where the presence of hydrogen is measured over a certain time interval to determine the total leakage. Alternatively, a hydrogen probe can scan the object's exterior, either manually or robotically, to pinpoint the location of leaks.
Testing Flexible Components The flexible materials used in many medical devices and consumables present a challenge for dry-air testing methods, because any expansion or contraction of the object will cause changes in the internal air pressure and distort the test results. Attempts are made to control this effect by physically restraining the object to minimize expansion during pressurized leak testing. For example, balloon catheters, collection bags, blood bags, IV bags, and nourishment bags are often sandwiched between two plates to minimize expansion. Unfortunately, these plates cover a significant percentage of the bag's exterior surface, blocking any actual leaks that are in contact with the plates. The hydrogen- based method has the advantage of being unaffected by the elasticity or plasticity of the test object. Unlike the dry- air methods, hydrogen-based testing is not temperature sensitive, so there is no need to delay the test procedure while pressure and temperature are stabilized. Another advantage of the hydrogen method is that the tracer gas is injected with minimal pressure, so there is no risk of deforming or destroying bags and other flexible materials. Moreover, the hydrogen probe pinpoints the location of leaks, unlike dry-air pressure testing which simply measures the total leakage of an entire object.
29 September/October 2005 Today's Medical Developments Testing an Implanted Device For these reasons, the hydrogen method has proved to be an ideal solution for leak testing of the Lap-Band laparoscopic surgical implant for treating obesity. The gastric banding device utilizes a balloon that constricts stomach size. The balloon is connected, via a tube, to a "port" placed under the skin, allowing the balloon to be inflated or deflated with the injection (or extraction) of saline solution during an outpatient procedure. Obviously, the leak integrity of such a device is critical.
The elasticity of the balloon material has no effect on the accuracy of hydrogen- based testing. The hydrogen method is also very effective at testing the integrity of seals where the tubing is connected to the balloon and the port, because a probe can scan these particularly sensitive locations and pinpoint the exact source of any leaks.
Properties of Hydrogen The properties of hydrogen offer a number of benefits for leak testing of medical equipment. Hydrogen is the lightest element in the universe -- 15 times lighter than air. More significantly, its molecular velocity is much higher and viscosity much lower than both air and helium, which means that it spreads easily throughout the test object, penetrates leaks more readily, and vents away significantly faster than any other tracer gas, thereby minimizing the chances of background build-up. Unlike helium, hydrogen does not stick to surfaces, making it an ideal tracer gas when sequential tests are required on different parts of the same object, such as the testing of multiple lumens in a catheter or multiple compartments of an implantable medical device. Hydrogen is the least expensive of all tracer gases. Hydrogen-based testing is also safe and environmentally friendly, meeting the requirements of ISO 14001.
Because hydrogen is a naturally occurring gas that is totally non-toxic, it has no adverse effects on the environment and can be produced anywhere using very simple methods. For leak detection with hydrogen, the recommended tracer gas mixture is 5% hydrogen to 95% nitrogen, which is available in industrial grade from most gas suppliers. This mixture is classified as non-flammable according to Leak Detection. the international standard ISO 10156.
Compatibility of Hydrogen and Dry- Air Pressure Methods By providing high sensitivity and the ability to test elastic objects, the hydrogen method overcomes many of the shortcomings of dry- air pressure methods. Many manufacturers take advantage of the benefits of hydrogen testing to enhance or augment the testing performed by dry-air methods, such as pressure decay testing. Indeed, hydrogen and dry-air methods are compatible approaches that can be deployed interchangeably or in conjunction with each other, depending on the requirements of the manufacturing process and the quality standards. For example, pressure decay is often employed as an integral test for an object as a whole, alongside a hydrogen testing capability that pinpoints the exact location of the leak. Another example of a hybrid approach occurs when an object has multiple compartments, some of which require the higher sensitivity of the hydrogen method, while the less-sensitive pressure decay method is satisfactory for other compartments. Because the testing process, the test apparatus, the training requirements, and the cost of the hydrogen method closely match the characteristics of dry-air pressure methods, it is easy for manufacturers to incorporate hydrogen into their existing dry-air leak testing systems, or replace them with hydrogen systems, in order to achieve higher sensitivity, leak location ability, and improved reliability. Product testing within the medical industry is an indispensable component of the medical manufacturing process. In particular, leak testing has become a vital component for medical equipment manufacturers as quality standards have become increasingly stringent.
Choosing the proper leak detection method is an important and often complicating challenge, as manufacturers should carefully explore the features and benefits of the various leak-testing methods on the market; a failure to make the right choice could potential bear fatal results. TMD Claes Nylander, is president and co-founder of Sensistor Technologies, a company on the cutting edge of leak detection.
Circle 29 31
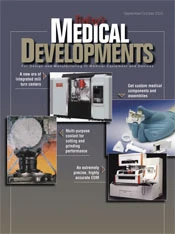
Explore the September 2005 Issue
Check out more from this issue and find your next story to read.
Latest from Today's Medical Developments
- HERMES AWARD 2025 – Jury nominates three tech innovations
- Vision Engineering’s EVO Cam HALO
- How to Reduce First Article Inspection Creation Time by 70% to 90% with DISCUS Software
- FANUC America launches new robot tutorial website for all
- Murata Machinery USA’s MT1065EX twin-spindle, CNC turning center
- #40 - Lunch & Learn with Fagor Automation
- Kistler offers service for piezoelectric force sensors and measuring chains
- Creaform’s Pro version of Scan-to-CAD Application Module