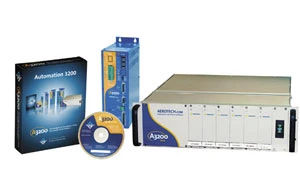
When you examine today's technological advancements, they usually fall into one or more of three categories: more features, faster and/ or smaller. No doubt we are living in a world where rapid technological change is the norm rather than the exception.
Medical devices are not immune to this advancement and, in fact, are pushing the envelope.
As the medical device industry has advanced, it has become extremely important to improve time to market, throughput, and manufacturing tolerances. An interesting example is the manufacture of stents, where manufacturing tolerances have actually reached the submicron level.
In addition, because these devices will be inserted into human arteries, they must be free of grooves and burrs and also must be completely hygienic.
Typical manufacturing requirements of stents include:
- Stents are usually manufactured from stainless steel, nitinol or a cobalt-based alloy.
- Stent design is usually a mesh structure or a coil.
- Stent materials can be as thin as 0.001" (25.4µm).
- Typical diameters of stents are from 0.08" (2mm) to 0.2" (5mm) .
- Complex geometries require accuracy and cutting tolerances of ±0.0001" (2.54µm).
To put some of these numbers into perspective, the diameter of a human hair is approximately 100µm, so the entire wall thickness of the material in a stent is 25% the thickness of a human hair. By reviewing these numbers, it is easy to understand the difficulties of ensuring quality manufacturing. But what is the best method of production to meet these tight tolerances? Due to its unique capabilities, laser processing has become the predominant method of cutting, ablating, and welding materials for stent manufacturing. Compared to other cutting methods, laser processing produces very smooth edges that substantially reduce the finishing process. Another laser processing benefit is the ability to make intricate design cuts with extreme precision and accuracy. These factors allow the system to be more cost-effective to deliver improved throughput.
The ideal laser-machining center will produce the highest quality, be highly repeatable, and will optimize the entire process. When designing the lasermachining center, there are several factors to consider: the laser, motion equipment, the controller and the base structure.
PROCESING CHOICES
Factors to consider when selecting the laser include laser power, bandwidth, wavelength, operating frequency, spot size, pulse duration and beam quality.
The choice of laser, which is usually YAG or fiber, will depend on the type of material being cut, the wall thickness of the tube, and the type and cutting detail that is required.
In general, a stent-cutting machine requires a rotary and a linear axis.
In its simplest form, this can be accomplished by bolting individual components together. It is then necessary to add some material handling capability. However, due to the inherent errors in the individual components themselves and the bolting of the axes together, and the addition of a material handling system, it is not possible to assemble a truly optimized system.

IMPROVED DESIGN
With the push for tighter tolerances and higher throughput, an optimal design that integrates the rotary and linear axes, as well as the collet (material handling) mechanism, provides a better solution. An example of an optimized, integrated system is the VascuLathe series. The rotary axis has been designed to integrate directly onto the linear axis so that it is in-line with the linear motor and bearings.
This design improves overall system stiffness and increases the resonant frequency. The rotary axis also has an integral pneumatic-activated collet mechanism, effectively reducing system complexity and minimizing the total system moving mass. The system also has an optional wetcutting configuration for applications that utilize fluid to minimize the heataffected zone and backwall damage, and to assist in the evacuation of waste material.
The cumulat ive effect of the VascuLathe's optimized design results in throughput improvements from 200% to 500% when compared to t radi t ional component - level manufacturing approaches, while still maintaining submicron tolerances on tight part geometries.
In addition to selecting the proper mechanical stages, it is equally important to choose an appropriate multi-axis motion controller. An example of a feature-rich multi-axis controller that is very good for medical device manufacturing is the Aerotech Automation 3200 (A3200). The A3200 is a software-based controller that offers up to 32 axes of synchronous motion. Key A3200 features used in medical stent manufacturing include contoured motion, PSO laser triggering, circumferential units and multi-block look-ahead.
One feature that is extremely useful is the ability to program in circumferential units. So what does this do and how is it useful? By specifying the diameter of the cylindrical part, a program can be written as if it were in XY space.
The program then translates the XY coordinates onto the cylindrical part and cuts accordingly.
Another feature that is essential for cutting small circles or arcs on a cylindrical part is contoured motion.
Contoured motion refers to motion in which multiple axes are required to work in conjunction with each other. The A3200 is not only capable of providing contoured motion, but also utilizes an advanced feature, "multi-block lookahead," to optimize cutting velocity as a function of part geometry.
While executing a program, the multiblock look-ahead function is constantly reviewing lines of code that execute later in the program. Acceleration induced by arcs and circles in the part are calculated by the look-ahead function and compared to a threshold acceleration value defined by the user.
If the acceleration in an arc is above the allowable threshold, the controller will slow the cutting speed before the part feature is processed to ensure that the acceleration limit is not exceeded.
Once t h e feature has been processed, the programmed cutting velocity resumes. By adjusting the acceleration limit in the program, it is possible to directly control the part accuracy and system throughput.
Reducing the acceleration limit results in lower position errors and longer processing times. Higher acceleration settings result in increased position error and increased system throughput.
Another key feature is the A3200's ability to trigger and control the laser based on position. Position synchronized output (PSO) uses a combination of hardware and software to allow laser triggering to be based on the actual position of the axes.
When used in combination with multiblock look-ahead, the PSO function will ensure consistent laser beam spot overlap as the cutting velocity changes, resulting in improved edge quality and reduced heat-affected zone.
BASE STRUCTURE
The base structure includes the machine base, system base plate and support for the laser optics. If the system is not optimized for stability, significant errors can occur that will affect the quality of the parts produced.
Errors are introduced into the process from high system dynamics transferring energy into the system, affecting the system stability and position tracking error during the process. As the axes move, reactive forces are generated within the system. In order to minimize the effects of system dynamics, a stable base structure design is recommended, which may include components such as a granite base plate, elastomeric isolation and a steel machine base.
The other area of concern is the error that can be created in the differential motion between the part and the laser head. This error is not observable within the control system and thus cannot be corrected through the control loop. The best method for reducing this error is to optimize the stiffness of the structure holding the laser and optics. One recommended method is to provide a solid granite bridge structure to mount the optics and to minimize the length of the unsupported laser head. This design not only provides the necessary support to compensate for the moving axes, but also can support the optics, resulting in improved part quality.
IN SUMARY
As manufacturing of stents and other cylindrical parts continues to require tighter tolerances, it is becoming exceedingly important to consider all aspects of a lasermachining center. The end result of this optimized machining center is a system that saves money by providing improved throughput and better quality parts.
Aerotech Inc.
Pittsburgh, PA
aerotech.com

Explore the May 2009 Issue
Check out more from this issue and find your next story to read.
Latest from Today's Medical Developments
- Methods Machine Tools, Multiaxis, announce AI solution investment
- MGS to showcase global expansion and healthcare CDMO expertise
- Medtronic: 5 healthcare tech trends for 2025
- Norman Noble launches enhanced laser welding capabilities; expands micromachining in Florida
- What you need to know about CMMC requirements
- CO2 footprint of a machine tool
- Ainos unveils AI Nose for robotics
- Keep up with the latest in design and manufacturing through free webinar