
Metal fabricators in the U.S. have had to adapt to the industry's evolving demands, including shorter runs, prototyping and flexible operations.
Fabricators serving the medical device field are no exception. As demand grows for these devices, so does the attention of suppliers, so when medical device customers say they want rapid turnaround on short-run parts, fabrication shops like Salem Metal Fabricators, Inc., Middleton, MA, look for machinery that can do the job.
CUTTING PARTS AND TIME

Salem Metal's LVP 3015 rips through a sheet of metal at the company's production facility in Middleton, MA.
Salem Metal fabricates a long roster of parts for medical device makers, including internal components for defibrillator machines, parts for mobile computer carts for hospitals, and covers and cooling system components for MRI machines.
The 37-year-old company acquired a Mitsubishi 3015 LVP laser machine about four and a half years ago. The 3.5 kW CO2 laser allows the 34-employee job shop to create and deliver parts in a fraction of the time that it took with a turret punch press, Vice President Jason Vining says. These parts, especially because of their medical-related applications, have to be free of the sharp edges and burrs that punching leaves behind. Cutting these parts with the laser also produces cleaner edges than punching could achieve.
A full-service job shop, Salem also uses the LVP for larger-radius parts that cannot be done on the company's turrets without spending a lot of money on tooling. With the laser, "the setup charges and the tooling costs are really reduced," Vining says.
Vining explains that while actual production time is longer on the laser than on the turret, the superior edge quality of parts coming off the LVP more than makes up for the difference, when secondary operations are considered.
Mitsubishi's proprietary Diamond Path technology is partially responsible. Diamond Path uses a U-shaped optical path to maintain a fixed beam length, regardless of the cutting head's position on the table. This creates cleaner, more consistent cuts throughout the cutting cycle.
"There is no zonal cutting on the machine," says Jeff Hahn, senior product manager in Mitsubishi's laser sales engineering department. "It cuts as well on the near point as the far point on the table."
In addition, the LVP's integrated beam optimizer and adaptive optics allow users that cut a variety of material types and thicknesses to get the best speed and cut quality automatically. "It changes the beam size to fit the application," Hahn says.
Salem has found the LVP's flexibility to be invaluable. The company routinely cuts parts from aluminum, 304 and 316 stainless steel, mild steel and Hastalloy in varying thicknesses. Doing these cuts on the LVP—as opposed to stamping them, milling them or cutting them—gives the company greater capacity and faster production.
As for cost of operation, most customers realize that the LVP's speed more than compensates for the lower cost per hour of other technologies such as milling or waterjet cutting, he says. "In general, depending on the quantity we're doing and the thickness, the laser has a lot of advantages," Vining says. "If you put any waterjet against my CO2, my pile of parts is going to be a lot higher at the end of the day. If you're only cutting three pieces, it doesn't much matter, but if it's 500 pieces, there's no comparison."
PROTOTYPING: SPEED WITH QUALITY
The LVP's flexibility allows customers, such as DJ Orthopedics, to create in-house prototypes in minutes instead of hours or days. DJ Orthopedics manufactures non-invasive, sports-related equipment such as braces, supports and immobilizers. The company cuts mostly stainless and aluminum. "Speed to market is the LVP's key benefit," says Tooling Manager Vladimir Archipov. "The laser really allows us to go from long to short production runs, and allows us a lot of flexibility."
DJ Orthopedics uses a variety of technologies to create its parts, depending on the application and the number of parts needed, including lasers, CNC milling machines, progressive stamping presses and plastic injection molding machines. In the past, the company would run its production-volume parts Monday through Thursday and reserve Fridays for its R&D group because of the time demands prototyping put on its equipment. "You would either send it to the tool room and tooling would machine something, or we would rig up a quick stamping system," says Archipov, who has been with the company for about seven years. "This takes a week or so. If we outsourced it, it depended on how backlogged they were."
"It helps out if we're prototyping something and the customer only wants 10 pieces," Salem's Vining says. "We get a lot of prototyping work. It might take an hour to set up a turret with all the tools. Now we can have a prototype in a short amount of time."
FULL-SYSTEM MANUFACTURER
A company's success hinges on its ability to position itself for growth and adapt to changes in the market. Mitsubishi delivers the technology and flexibility to accommodate demands from multiple industries. Because Mitsubishi is a fullsystem manufacturer, as opposed to a system integrator, it can provide a blend of technologies that maximizes the reliability of its lasers.
"The LVP is a very diverse machine in changing over from one application and material type and thickness to another," Mitsubishi Laser's Hahn says. "It's been a very stable machine in production at mospheres."
The LVP can cut mild steel up to 1 in. thick, stainless up to ½ in. and aluminum up to 3/8 in., all for a cost of ownership lower than higher-wattage machines with the same material thickness range.
"We're a job shop serving all industries," Vining says. "We try to make decisions in the best interest of the company—we generally won't choose one machine over another on just cost alone. We do our research and figure out what would be the best machine for the company.
"One of the big factors was the cost of the machine relative to what you're getting in the machine," he says. "Mitsubishi is not compromising the quality of the machine or the efficiency of the machine. Ever since we bought the Mitsubishi, we've been running it 50 to 60 hours a week. The laser is very busy."
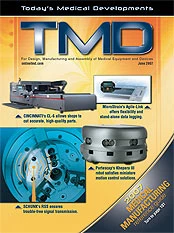
Explore the June 2007 Issue
Check out more from this issue and find your next story to read.
Latest from Today's Medical Developments
- HERMES AWARD 2025 – Jury nominates three tech innovations
- Vision Engineering’s EVO Cam HALO
- How to Reduce First Article Inspection Creation Time by 70% to 90% with DISCUS Software
- FANUC America launches new robot tutorial website for all
- Murata Machinery USA’s MT1065EX twin-spindle, CNC turning center
- #40 - Lunch & Learn with Fagor Automation
- Kistler offers service for piezoelectric force sensors and measuring chains
- Creaform’s Pro version of Scan-to-CAD Application Module