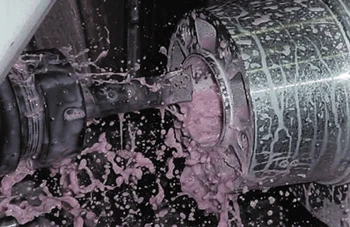
According to Raymond M. Dick, manager of CIMCOOL Technical Service, Milacron, Inc., what should appear obvious sometimes is not: A clean metalworking fluid performs better and lasts longer than a dirty fluid.
"When recharging an individual machine or central system fluid tank," say Dick, "a cleanout of the tank is beneficial so that the fresh charge of metalworking fluid can perform with maximum efficiency. If it is not removed, accumulated shop waste, metal swarf, oil, mold growth, and pockets of bacteria cause deterioration of the fresh mix. Cleanout is an essential step, as it ensures that a metalworking fluid has an even-chance to give maximum performance with a minimum number of problems."
According to Dick, the following ten simple cleanout procedures should be used, whenever possible, while no operations are producing parts.
1) Drain the entire central system or individual tank.
2) Remove all metal swarf and other debris from sumps, return trenches, oil pans, and filtration units.
3) Fill the system or tank with water sufficient to circulate through all lines and machines. Warm water is desirable, but is not absolutely necessary.
4) Add CIMCLEAN 30 cleaner at 1:50 or stronger and circulate from 2 to 8 hrs. During this period of circulation, brush all trenches and filter elements; scrub machines and oil pans.
5) If possible, steam clean areas where suspected accumulation of swarf, oil, or both may not have been removed by the cleaner.
6) When the physical cleaning is complete, drain the CIMCLEAN 30 mix from the system.
7) Refill with enough fresh water to circulate throughout the system or tank so that all traces of cleaner and swarf are removed. Drain all lines and sumps. If the rinse water is exceptionally dirty, rinse a second time.
8) Charge the system or individual tank with the required amount of water.
9) Add fresh metalworking fluid at the recommended concentration.
10) Circulate through the system to ensure proper mixing before production starts.
In precision grinding systems, circulate the fresh charge until it reaches room temperature. Otherwise,
size control problems may be encountered by the first production shift.
Sometimes it is not possible to drain the system because of production demands or a manpower shortage. However, try to incorporate as much of the cleanout procedure as possible during shutdown or during production to achieve good cleanout results.During shutdown. After production stops, add one gallon CIMCLEAN 30 to each 50 gallons of dirty fluid in the machine reservoir or central system. Circulate the mixture for 4 hours or longer through all lines and machine tools. Drain, rinse, and recharge with a fresh fluid mix.
During production. Careful supervision is required for individual machines. During production, add I gallon CIMCLEAN 30 to each 100 gallons of dirty fluid in the machine reservoir or central system. Circulate the mixture for 4 to 8 hours through all lines and machine tools. Drain, rinse, and recharge with a fresh fluid mix. For aluminum applications use CIMCLEAN 40.

Explore the November 2005 Issue
Check out more from this issue and find your next story to read.
Latest from Today's Medical Developments
- HERMES AWARD 2025 – Jury nominates three tech innovations
- Vision Engineering’s EVO Cam HALO
- How to Reduce First Article Inspection Creation Time by 70% to 90% with DISCUS Software
- FANUC America launches new robot tutorial website for all
- Murata Machinery USA’s MT1065EX twin-spindle, CNC turning center
- #40 - Lunch & Learn with Fagor Automation
- Kistler offers service for piezoelectric force sensors and measuring chains
- Creaform’s Pro version of Scan-to-CAD Application Module