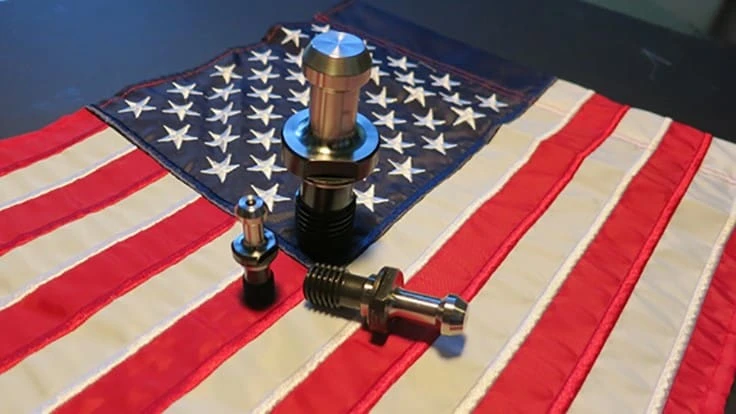
JM Performance Products
COVID-19 has exposed how many domestic brands rely significantly upon China for fulfilling some, part, or nearly all of their supply chain.
The Reshoring Initiative (RI) founder and president Harry Moser and JM Performance Products (JMPP) president John Stoneback participate in a Q&A on how the crisis has affected the reshoring effort.
Reshoring pre-and-post COVID-19 considerations

Moser: The annual rate of jobs coming from offshore increased from 6,000 in 2010 to 180,000 in 2017. The cumulative jobs brought back represent about 5% of total U.S. manufacturing employment as of Dec. 31, 2019. The annual rate moderated in 2018-19, mainly because of President Donald Trump’s tariffs, which caused business uncertainty.
Multi-step, multi-country manufacturing was under stress even before the COVID-19 pandemic, which has severely disrupted the global logistics network. Our understanding of trade wars during this crisis now reveals the supply chain weakness – we simply don’t make enough components on our own shores.

Stoneback: As manufacturing reshores and jobs open up, the need for skilled operators will increase. Manufacturers will be faced with elevated costs as they hire skilled workers, invest in training, or define new methods so that lesser skilled employees are able to handle the production requirements.
Companies that examine their operations at the machine shop level and take action to correct problems at the very base will be able to forego the highly skilled individual, instead opting to employ a less skilled individual who will not need to make on-the-fly adjustments.
How is the COVID-19 crisis different than others like 9/11 or the 2008 recession in terms of reshoring and manufacturing?
Moser: On the international market, import and export regulations can always be a hurdle for finding the right suppliers. This was especially true for US businesses after 9/11. The extra time and money spent on certifying a supplier for regulations like the Customs Trade Partnership Against Terrorism (C-TPAT) is another trade-off that management must consider when diversifying their supply chain.
The financial crisis of 2008 drove OEMs to essentially not buy anything. On-hand plus pipeline inventory from Chinese suppliers might total 3 to 6 months usage – if you get it locally, it’s 3 to 6 weeks. Additionally, big companies are more resistant to recession and can handle the problem of low sales much better. China pays in advance and the U.S. pays 60 to 90 days after shipment, so there’s more control during a disaster.
Developing domestic partnerships is the new reshoring. Customers, in most cases, are willing to pay a premium for on-time, as-promised delivery commitments. The goal is to convince companies to do the math and decide what to reshore now.
Stoneback: This crisis has made the entire country aware of our supply chain issues. Many consumers were blissfully unaware that our nation is dependent upon China and other Eastern countries for so many commodities such as pharmaceuticals, textiles, medical devices, and even food. Our lack of preparedness and inability to secure life-saving equipment and supplies opened many eyes. In past crises, the supply chain was not as critically impacted. The general population is now calling for reform, and it is up to North American manufacturers to reduce the risks of a broken supply.
Can COVID-19 be a positive/progressive factor for reshoring?
Moser: This can become a real opportunity to drive publicity about reshoring. It reminds me of an infamous quote from former Chicago mayor and chief of staff Rahm Emanuel to President Barack Obama during the 2008 financial collapse: “Never allow a crisis to go to waste…start planning for the future.”
Stoneback: This situation provides the catalyst for manufacturers to reexamine how they buy and how they manufacture. There is an imminent demand emanating from the consumer level to make changes. A new understanding that the least expensive supply or manufacturing options may ultimately bare the highest risks will add a new dimension to cost analysis. There will hopefully be a migration at the consumer level from purchasing the least expensive articles to purchasing fewer items, but those that are domestically manufactured and better quality.
Which markets/industries are most susceptible to COVID-19 and would benefit most from reshoring?
Moser: Shortages of medical products due to 90% to 95% dependence on imports make medical and pharmaceutical markets the top priority targets which bridge over to OEMs for components. Medical supplies accounted for roughly $53 billion worth of U.S. imports last year. Reshoring production for half of those supplies could generate an additional 302,000 jobs and add $534 billion to the GDP.
When the COVID-19 pandemic ends, America’s global supply chain must be replaced with local and national sourcing, but it won’t just be in health care. Other leading industries of focus include transportation equipment, appliances, plastic and rubber products, fabricated metal products, electronics, and apparel.
Stoneback: The mold making industry in this country undeniably took a heavy hit due to off-shoring production. Reshoring would allow for higher quality, longer life, and faster response to opportunities. Having the ability to reduce costs in mold production, along with the reduction of transportation costs, would put mold makers in a stronger, more sustainable competitive position.
What opportunities/pitfalls does this represent for domestic manufacturers?
Moser: COVID-19 is a valuable wake-up call as it reveals our weaknesses and what we can, and need, to do. There’s substantial interest from the administration to build up US manufacturing, so we need to push for more funding for proactive organizations and programs that are in place that can help in the process of reshoring. Notably, Manufacturing Extension Partnerships (MEP) and the Coronavirus Aid, Relief, and Economic Security (CARES) Act are vital programs that can help manufacturers select the US now in focusing on reshoring.
How can domestic manufacturers offset costs vs. offshoring post COVID-19?
Moser: The key is to calculate and measure costs correctly. Take a look at key reshoring factors like duty freight, the cost of inventory, travel, etc., and how that impacts total costs and factor that in. Then, you can also factor in reshoring savings like Trump tariffs as well as cost savings from state-side technology production efficiencies like JMPP’s HTRKs that can drive those numbers higher.
Stoneback: Fewer interruptions to the process yields high production and lower costs. Reduction in secondary or additional processes not only positively impacts the cost per unit, but also impacts the cost associated with handling the product multiple times. Any reduction in production cost impacts the manufacturer’s competitive edge.
How does COVID-19 affect the global supply chain landscape?
Moser: Having relegated the supply chain to China for most of the past decade, some companies started taking steps last year to divest their over-reliance on Chinese parts, prompted by the trade war. Some companies shifted low-cost parts acquisition to Vietnam and others to Mexico.
Trade as a percentage of world Gross Domestic Product (GDP) over the last 3-4 years was slowing and already plateauing before COVID-19. Companies were beginning to realize that depending on other countries wasn’t the economic or ‘green’ solution long term. So, the focus was trending towards localization/regionalization even before the global pandemic.
According to our Reshoring Initiative study, manufacturing jobs via reshoring by U.S. companies and through foreign direct investment (FDI) grew to 180,000 in 2017, the fastest rate in history. That’s up 50% from 2016 and 2,800% from 2010. This must continue in the post COVID-19 economic landscape, and the US should leverage more outsourcing from Mexico versus China if the US isn’t an option.
Will this crisis shift/influence the higher cost vs. lower risk equation of reshoring?
Moser: When people reshore, they accept a higher US cost, but reduction in overhead (inventory, travel, international property, etc.). The bottom line is to reshore the products where the savings on overhead and risk is greater than the increase in manufacturing cost.
Stoneback: Effectively reducing the manufacturing costs, along with reduction in overhead costs, will ultimately lower the higher costs people have to accept.
Latest from Today's Medical Developments
- Children’s National, FDA collaborate to advance pediatric device regulatory tools
- LK Metrology’s eco-friendliness CMMs
- Two patents for microfluidic valves
- AMADA WELD TECH’s blue diode laser technology
- Post-IMTS decline in manufacturing technology orders blunted
- ARS Automation’s FlexiBowl 200
- LMA Consulting urges businesses to restructure supply chains now
- Walter’s WEP01C indexable inserts