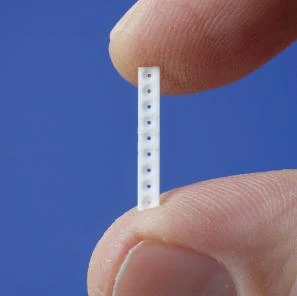
For complex parts requiring extensive and intricate machining, shops rely on the UP32I wire EDM's high accuracy and superior surface finish capabilities. Thanks to its Crystal Machining Circuit (CMC), the machine generates surface finishes down to 3 microin. Ra with no special tooling, jigs, or fixtures.
Surface finishes of up to 0.5 micron Ry are possible for hardened workpieces measuring as much as 31.1326.438.7 in. The machine's roundness capabilities allow it to burn guidepin holes equal to those obtained by jig grinding.
A variety of automaticthreading methods optimize the UP32I's unattended operation. These methods include high speed, smallhole, and normal settings randomly established within the same program based on necessary applications. The manufacturer's automatic wire threading process threads wire in 15 sec. for holes as small as 0.19 in. in diameter.
One set of machine wire guides delivers 2,000 machining hours with wire diameters of 0.003 to 012 in. Guides do not require removal for cleaning, which virtually eliminates vertical aligning.
The UP32I's WireWizard operating system makes highspeed and accurate machining possible. This special control has three main graphical components that maximize throughput programming, setup, and run and fulfill basic application needs. It does so without sacrificing speed, allowing for up to 30% faster processing as compared with other EDM technologies. The system automatically selects optimum machining conditions even for shapes where waterpressure changes occur, like at the edge of a workpiece.
A drop tank lets users setup work from three sides of the UP32i. This enclosed work area, which is isolated from ambient temperature changes, minimizes thermal distortion on the work tank and the machine's upper head.
Covered area temperatures coincide with the machine's dielectric fluid temperature, which is handled in the bed tank by a special control process. This reduces machine temperature changes and adds to accuracy and extended operation.
The UP32I accommodates workpieces weighing up to 1,323 lb and sports a 50nanometer scalefeedback system for micromachining and positioning accuracy. Taperangle capacity is 15 with a 35 option.
Makino
Mason, Ohio
makino.com
Circle 51

Explore the May 2005 Issue
Check out more from this issue and find your next story to read.
Latest from Today's Medical Developments
- Tariffs threaten small business growth, increase costs across industries
- Feed your brain on your lunch break at our upcoming Lunch + Learn!
- Robotics action plan for Europe
- Maximize your First Article Inspection efficiency and accuracy
- UPM Additive rebrands to UPM Advanced
- Master Bond’s LED415DC90Med dual-curable adhesive
- Minalex celebrates 60 years of excellence in miniature aluminum extrusions
- Tormach’s Chip Conveyor Kit for the 1500MX CNC Mill