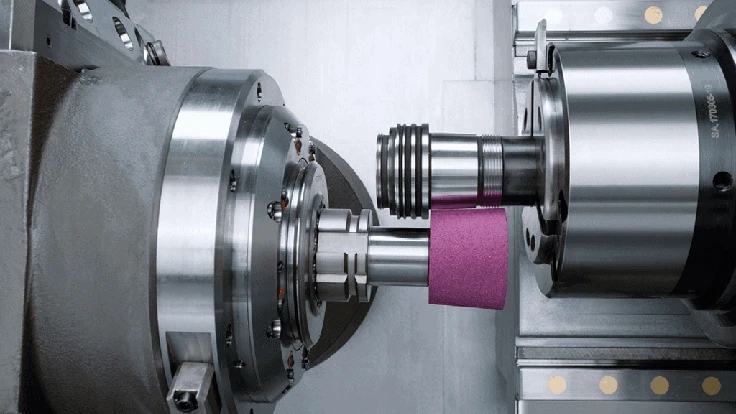
INDEX

1. When should a shop look at incorporating grinding onto a turn-mill center?
The most common barrier to grinding on a turn-mill is that many parts require heat treatment after machining, prior to grinding. The advantages of performing all operations on a single machine are largely negated if you have to remove the part midway through production for a separate process. Medical manufacturers rarely encounter this issue, as components use materials that don’t require heat treatment.
The chief concern for medical components is holding the part – many parts feature complex geometries better suited to custom workholding on a milling center. That said, a considerable percentage of medical parts can be held in a turn-mill and most are suitable candidates for completing grinding operations within the machine. A machine builder’s engineering department can validate a part’s suitability to this approach.
2. What benefits do medical manufacturers achieve by combining operations?
Many medical manufacturers must outsource grinding, so being able to complete production in-house on existing equipment saves on cost, speeds turnaround times, and improves quality control.
For those using dedicated grinding centers in-house, consolidating to a single machine streamlines production by eliminating part flow from machine to machine. Completing parts in a single setup removes the potential for inaccuracy from setting up a part multiple times. Additionally, removing one or more dedicated grinding centers frees up floor space, consumes fewer labor hours, and reduces cost per part.
3. How fast is turn-mill center grinding vs. dedicated grinders?
Cycle times for grinding operations can be reduced up to 50% on a turn-mill. When finishing a part on a separate grinding center, programmers must account for loss of accuracy introduced by moving it between machines. This includes leaving extra material on the part to be removed via grinding to meet required tolerances. If the part is being cut to completion on a single machine, the programmer can maximize material removal via turning and perform far less grinding.
4. What key features does a turn-mill center need to succeed with grinding?
It’s imperative the machine offers rigidity and accuracy to handle grinding. Without the requisite rigidity, you can end up with chatter, making it impossible to achieve the needed surface finish. Likewise, accuracy and thermal control of the machine are required to hold high tolerances. The machine should include a coolant chiller as well as active temperature control of its various components.
5. If a shop decides to move forward with this approach, what additional actions are needed in terms of hardware, training, etc?
Once the decision is made, integration is fairly straightforward. At INDEX, we typically offer customers turnkey solutions, so it’s fairly plug-and-play for machines dedicated to a single part or part family. Shops wishing to move additional parts to the machine on their own only need a basic knowledge of grinding processes, such as which wheels to use, appropriate cutting data, etc. Programming grinding on a turn-mill is no more complicated than programming the primary metal cutting operations.
FOR MORE INFORMATION: https://us.index-traub.com

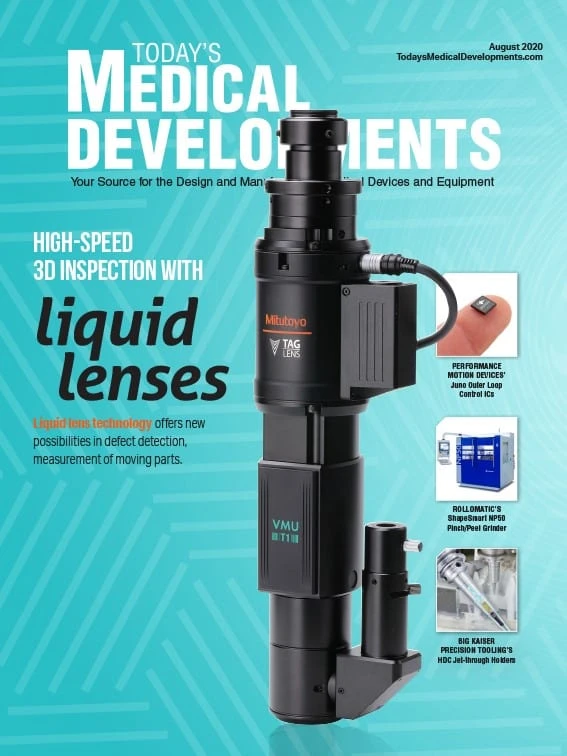
Explore the August 2020 Issue
Check out more from this issue and find your next story to read.
Latest from Today's Medical Developments
- Dassault Systèmes enters next phase of Living Heart Project with AI-powered virtual twins
- Bruker’s X4 POSEIDON advanced X-ray microscope
- #53 - Manufacturing Matters - 2024 Leaders in Manufacturing Roundtable
- Festo Incredible Machine celebrates its premiere at the Hannover Messe
- Join us for insights on one of the hottest topics in manufacturing!
- Turnkey robotic systems are already behind the times
- You can still register for March’s Manufacturing Lunch + Learn!
- HERMES AWARD 2025 – Jury nominates three tech innovations