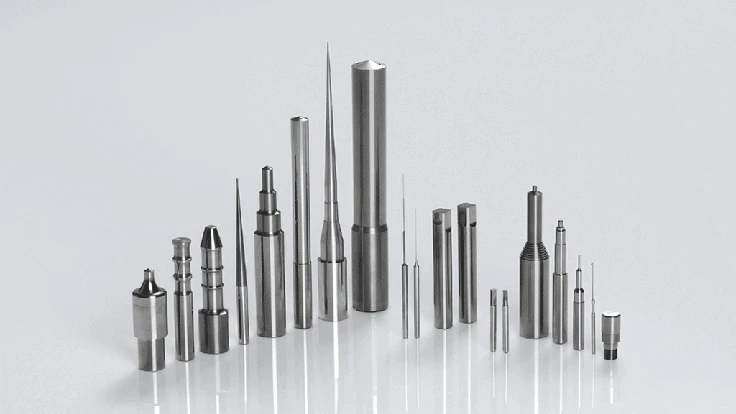
Rollomatic

HDC jet-through holders enable high-precision 5-axis machining with 35,000rpm max. speed and 1/4" to 1/2" clamping range. The holders’ thread feature allows convertible coolant delivery with jet-through coolant or center-through coolant. Jet-through hydraulic chucks are ideal for finishing applications – coolant flows through the end of the tool holder and is angled to direct coolant to the cutting tool tip, greatly improving surface finish and tool life. HDC tool holders use only one hex key wrench to clamp or loosen the cutting tool, making tool changes fast and easy. Every HDC toolholder is guaranteed to 0.00012" TIR at 5x diameter.

Outer loop control integrated circuits
Juno Outer Loop Control integrated circuits (ICs) provide functions for spindle, centrifuge, and precision torque control. Available in a 64-pin TQFP package measuring 12mm x 12mm, Juno incorporates digital logic integration and intelligent algorithm development, making them suitable for controlling pressure, temperature, liquid level, magnetic bearings, chemical reaction rate, and other outer loop quantities for medical, industrial, and military applications.
In a ventilator application, the speed of a brushless DC (BLDC) motor turbine directly affects the measured chamber pressure. A control host sends a stream of pressure commands to the Juno IC, which executes its outer loop function to maintain the desired pressure. Juno monitors system parameters at up to 10kHz.

5-axis pinch/peel grinder
ShapeSmart NP50 pinch/peel grinder supports round and non-round high-accuracy punches and pins. Improvements to the option for pinch grinding non-round parts improves accuracy and speed. The non-round process includes full pinch/peel grinding, ensuring extremely high tolerances, form accuracy, and the lowest total indicator reading (TIR) achievable, particularly important for thin and long parts. Oblong punches, form punches, squares out of center, corner radiuses, and any other shape can be produced with this method. The NP50 optimizes cylindrical grinding of carbide, ceramics, tool steel, and stainless steel with maximum surface finish and concentricity. Rough and finish grinding are performed in one pass, eliminating a separate process and reducing cycle time. The machine uses different grinding wheels running on separate spindles, positioned on independently controlled CNC linear slides.

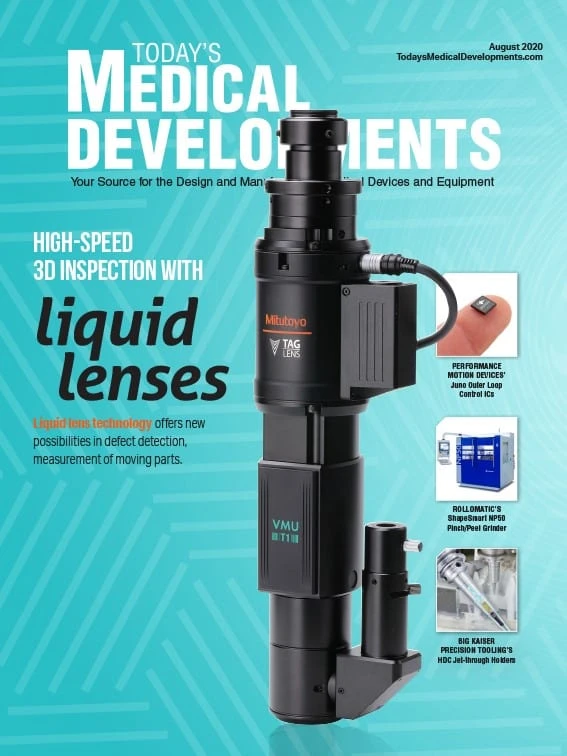
Explore the August 2020 Issue
Check out more from this issue and find your next story to read.
Latest from Today's Medical Developments
- Festo Incredible Machine celebrates its premiere at the Hannover Messe
- Join us for insights on one of the hottest topics in manufacturing!
- Turnkey robotic systems are already behind the times
- You can still register for March’s Manufacturing Lunch + Learn!
- HERMES AWARD 2025 – Jury nominates three tech innovations
- Vision Engineering’s EVO Cam HALO
- How to Reduce First Article Inspection Creation Time by 70% to 90% with DISCUS Software
- FANUC America launches new robot tutorial website for all