

1. What medical industry trends are driving the adoption of ultra-high molecular weight polyethylene (UHMWPE) fibers/textiles in implantable medical devices?
Innovation in the medical device industry is largely being driven by the desire to make implants smaller. This trend is exemplified by the move to minimally invasive surgical (MIS) techniques such as laparoscopic and robotic surgery, which calls for device designs incorporating more technical raw materials, such as UHMWPE fibers, facilitating the development of smaller implants and patient surgical incisions.
2. How can UHMWPE fibers benefit your end medical device?
With a strength-to-weight ratio 15x stronger than steel by weight and 3x stronger than polyester by volume, UHMWPE fibers allow for the development of smaller medical device components than other fibers that have historically been used. UHMWPE’s superior resistance to chemicals, fatigue, and abrasion, make it a prime candidate when evaluating materials that can extend the expected life of a medical device. This creates the potential for improved patient quality of life by reducing the need for revision surgeries in the future.
3. Why are selecting materials that are certified to be ISO 10993 biocompatible, and free of cytotoxicity, critical to medical devices? Does UHMWPE fiber meet those requirements?
Evaluating materials used for in-body applications (sutures, implants) for ISO 10993 biocompatibility and cytotoxicity is a critical part of the medical device design process because the designing company must ensure their selected materials will not produce a toxic or immune response once installed within the human body. UHMWPE fiber meets the biocompatibility requirements for in-body applications in ISO 10993. UHMWPE fiber’s compliance with the 10993 cytotoxicity requirements depends upon how the fiber was produced, so medical device companies should look for suppliers who provide documentation validating their UHMWPE fiber meets the ISO 10993 cytotoxicity standard.
4. What types of medical devices benefit from using UHMWPE fibers/textiles as components in their design?
Implantable medical devices for orthopedic, soft tissue repair, and cardiovascular applications are well-established examples of where UHMWPE fibers/textiles help to create superior performance. UHMWPE fibers help enhance the design of surgical robotic tendons by allowing for increased range of motion for surgeon’s control of appendages, improving the accuracy of surgical procedures.
5. What should you expect from your UHMWPE fiber supplier?
Medical device companies should seek suppliers who add value, not risk, to their medical device design process. UHMWPE suppliers who add value will:
• Carry an ISO 13485 certification
• Hold Master Device Files (MAFs) with the FDA that validate their fibers ISO 10993 compliant
• Ensure quality practices that call for 100% testing of all finished goods or products
• Manufacture their medical UHMWPE fibers at U.S. based facilities
Working with a UHMWPE fiber manufacturer who is ISO 13485 certified guarantees medical device companies that their supplier’s quality management system (QMS) aligns with its own quality requirements, promoting consistent design, development, and production of the medical device company’s own end products.
For more info: https://lifesciences.honeywell.com
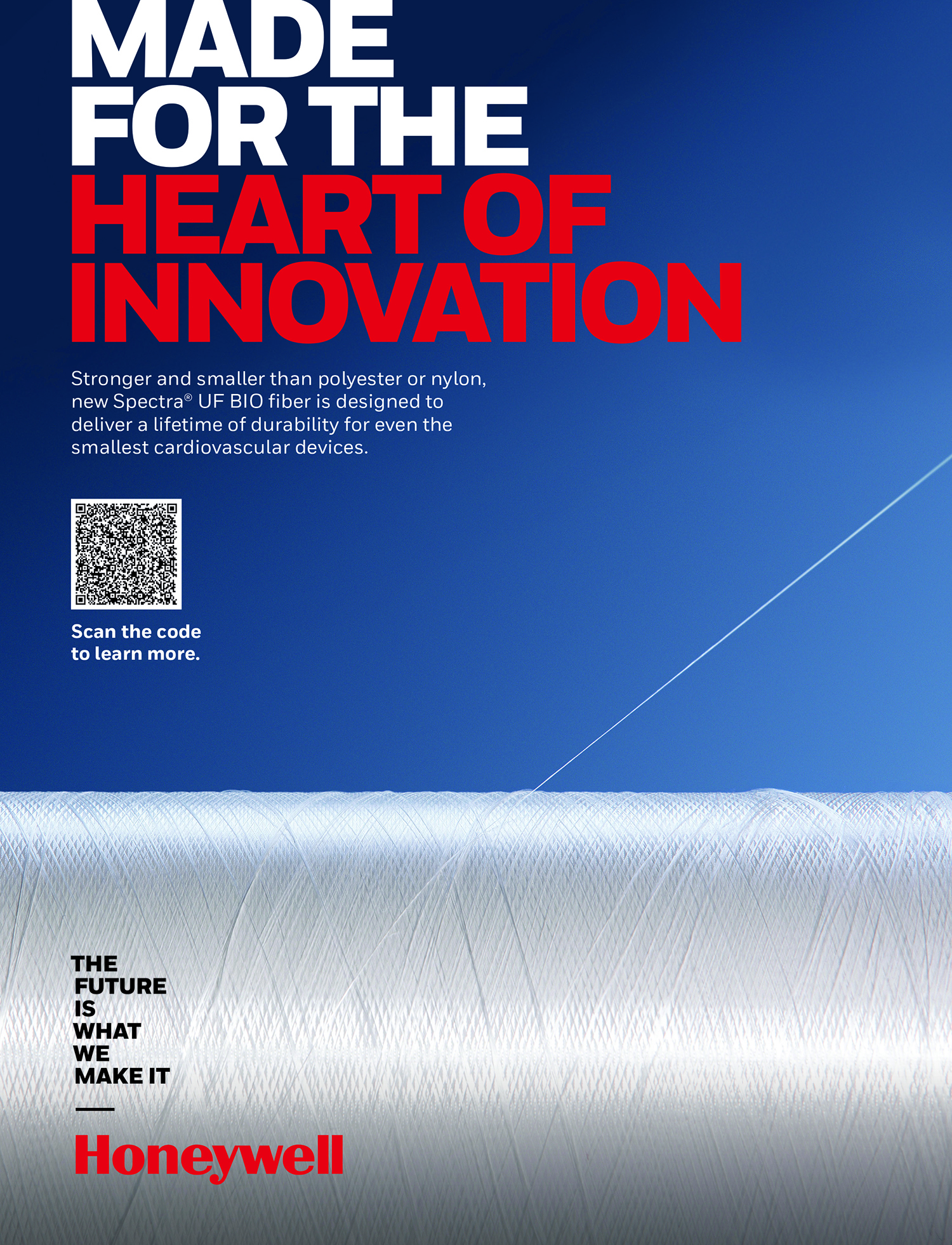

Explore the November December 2023 Issue
Check out more from this issue and find your next story to read.
Latest from Today's Medical Developments
- The Association for Advancing Automation (A3) releases vision for a U.S. national robotics strategy
- Mitutoyo America’s SJ-220 Surftest
- #56 - Manufacturing Matters - How Robotics and Automation are Transforming Manufacturing
- STUDER looks back on a solid 2024 financial year
- HANNOVER MESSE 2025: Tailwind for industry
- Find out the latest developments in tool path strategies for machining
- Building, maintaining the Navy’s next generation of maritime platforms
- Pioneering battery-free cardiac implants