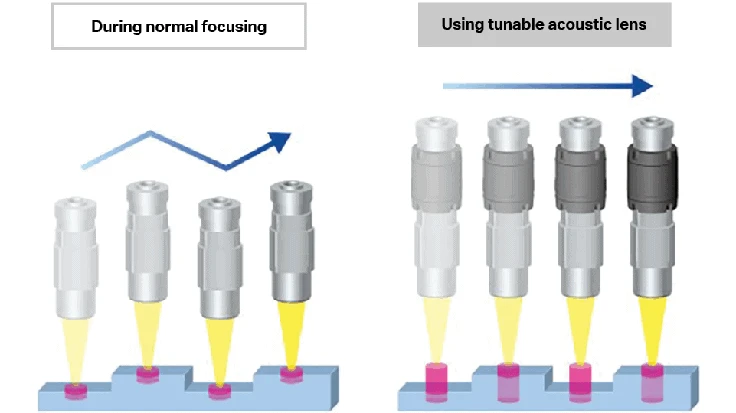
Mitutoyo America Corp.

Humans can focus vision close up or far away, but machines have traditionally struggled with variable-distance focusing, limiting the effectiveness of commercial liquid lens technology found in microscopes, metrology inspection systems, and diagnostic equipment. New technology, however, is giving machines the ability to control lens focal length at extremely high speeds, creating an asset in industries such as the medical field and in scientific, industrial, and commercial applications, where there is great demand to quickly control lens focus to support high-speed inspection.
Traditional non-contact inspection systems require mechanical movement of the lens assembly, slowing overall inspection throughput. Liquid lenses can more readily keep pace with speed demands.
In the last decade there has been a rise in technologies created to tackle speed issues, including those that use a liquid to focus light. In medical applications specifically, liquid lenses are being used for high-throughput inspection because they can overcome limitations around the need for mechanical focusing of the optics. This includes faster, qualitative inspection of medical parts being manufactured.
Liquid lens evolution
Before liquid lenses, mechanical focusing had to be designed into an optical system, which meant having a component raise and lower optics, enabling the user to refocus on different heights of an object. With liquid lenses and extended depth of focus (EDOF) software, a user can expand depth of field and eliminate the need for mechanical refocusing, making inspection simpler and faster.
The first liquid lens technologies, variable focus lenses, came around the start of the new millennium and relied on electrowetting to alter the shape of liquid. Electrowetting uses two fluids of similar density and different refractive indexes (typically water and oil). One fluid acts as a conductor while the other acts as an insulator, and applying voltage can control the shape of the interface.
Lenses that use electrowetting are compact, have low power consumption (tens of mW), provide a relatively large optical power range (15 diopters), and are inexpensive to manufacture. However, drawbacks include aberrations due to the orientation of the optical axis and a relatively low focusing speed. These aberrations restrict lens use in robotics applications because the robotic arm includes several orientations.
In 2010, a variable focus lens was developed that used optical fluid in a chamber with a flat side on one end and an elastic polymer membrane on the other. It altered fluid shape by:
- Pumping fluid in/out of chamber to alter lens curvature
- Changing lens aperture with a device similar to an iris diaphragm
- Mechanically or electrically applying pressure outside of the chamber
Each method creates a physical change in the liquid by physically changing the shape of the membrane.
Compared to electrowetting-based lenses, these lenses are dimensionally larger, yet share disadvantages of low focusing speed and aberrations due to optical axis orientation.
In 2011, a new liquid lens technology, initially developed at Princeton University, was introduced to the market: tunable acoustic gradient (TAG) index-of-refraction lens. Sound shapes light by putting a sound wave through a liquid, changing its density and altering the way the light penetrates. This liquid lens is inherently faster, running at 70kHz, which means it’s changing or sweeping through all focal points every 14 microseconds.

Applications of TAG lenses
TAG lenses offer the benefits of diffraction-limited performance, fast focus variation, lack of mechanically moving parts, and high transmission for near- infrared (NIR) and visible wavelengths, making them suitable for many industrial, scientific, and medical applications. Their diffraction-limited performance paves the way for integration into high-precision and high-accuracy metrology systems used in medical, semiconductor, automotive, and aerospace applications, allowing for significant system enhancements.
TAG lenses, when combined with high-speed embedded image processing, increase the measurement throughput of inspection systems.
This simplifies interfaces and minimizes hardware needed, resulting in faster and more economical inspection solutions. They can also be integrated into high-powered microscopes and other telecentric optical systems. Additionally, controllable image sampling at various heights, synchronized with the TAG lens and image acquisition system, allows for high-speed autofocus and 3D imaging without mechanically moving parts, which is ideal in biomedical and industrial applications.
Combining a TAG lens with high-speed image acquisition and processing also makes high-speed 3D imaging and analysis possible, offering new possibilities in defect detection and measurement of moving parts for inline inspection.
The future of liquid lenses
In terms of future applications for liquid lenses, robotics is on the horizon – specifically in applications where a robotic arm with a liquid lens imaging system allows for greater high-speed optical inspection of medical and other parts. Applications that leverage liquid lenses for higher power laser material processing also have great potential.
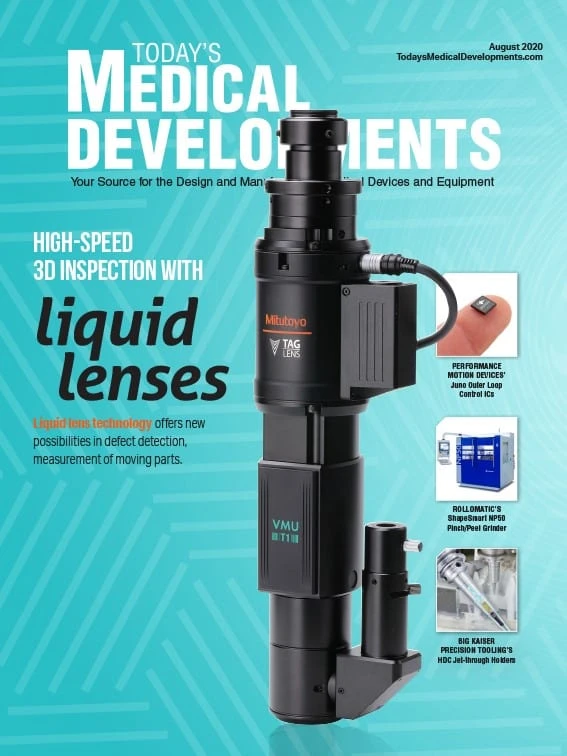
Explore the August 2020 Issue
Check out more from this issue and find your next story to read.
Latest from Today's Medical Developments
- Dassault Systèmes enters next phase of Living Heart Project with AI-powered virtual twins
- Bruker’s X4 POSEIDON advanced X-ray microscope
- #53 - Manufacturing Matters - 2024 Leaders in Manufacturing Roundtable
- Festo Incredible Machine celebrates its premiere at the Hannover Messe
- Join us for insights on one of the hottest topics in manufacturing!
- Turnkey robotic systems are already behind the times
- You can still register for March’s Manufacturing Lunch + Learn!
- HERMES AWARD 2025 – Jury nominates three tech innovations