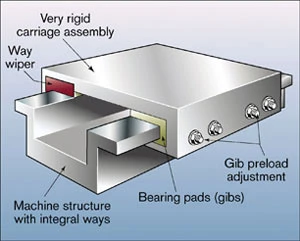
Improved accuracy measurement in linear ball rail system benefits medical applications, such as imaging, radiation treatment and bone density measurements.
In virtually any type of application requiring precision linear motion, linear rails have become the most common form of linear guidance. Increasing load capacities, improved rigidity, reduced friction and lowered noise are all characteristics that make the typical linear rail and runner block system the technology of choice, providing high performance in a compact footprint when moving something from side to side.
A linear guide consists of a recirculating ball or roller bearing mounted on a profiled rail. The recirculating rolling elements allow for very low friction and high efficiency of translated motions. There are no complex lubrication systems required as with sliding friction technologies like traditional boxways, once the standard used in many high-end machine tools.
Rail and block systems typically range in size from 7mm, for very small instruments, to 125mm, for large machine tools or aerospace applications with large loads. They are easy to specify, order, install and maintain. In the medical field, these would be used in applications such as machine beds, liquid handling devices and medical testing and sampling equipment.
As machines become more capable, the demand grows for even greater performance in linear guides. Designers begin to create solutions that were unfathomable with previous technology. For example, a doctor can now look at a human heart using what essentially is a high-end video system instead of surgery. He or she quickly develops a desire for sharper images, with greater detail. This in turn leads medical equipment designers to seek more precision in moving and positioning their imaging systems, which then leads linear guide manufacturers to develop rail and block systems with everincreasing precision. The patient benefits in the form of less invasive diagnostic techniques.
Accuracy in linear guides depends on many factors: the trueness of the rail on which the runner block or bearing travels; the raceways inside the bearing through which the balls or rollers travel; the operating environment; the flatness of the rail mounting surface; and other factors. Among high-performance linear bearings, the most important area of refinement is the smoothness of ball recirculation inside the runner block as it travels along the rail.
Applications at the very high end of the accuracy spectrum, such as gauging, bone density measurement, radiation treatment, microelectronics—even highend metal cutting—can be adversely affected by any roughness in the bearing tracks. This roughness can sometimes be felt even by hand as small pulsations from the balls travel over the rough areas. These pulsations cause pivoting or rotation of the bearing about its axis. For extremely precise applications, this rotation is magnified when transmitted over a distance to a measurement point. Even minute movement of the balls in the recirculation chamber can cause dramatic

Cross roller slide.

Example of load zone, entry zone and exit zone at work.
The lack of recirculating components in the cross roller slide also leads to stroke limitations. Typically, anything over 600mm is simply too long. In addition, cross roller slides lack the load capacity and rigidity of linear guides.
MINIMIZING PITCH, ROLL AND YAW
Typically, accuracy measurements in linear
guides are defined by the height and the width
variation as measured from the middle of the
runner block.
However, measurement of height and width alone do not account for any pivoting of the bearing about the X, Y or Z axes. In other words, although the height or width of the bearing may be extremely accurate when measured from the middle of the runner block, there may be some inaccuracy about the center line of the bearing due to ball pulsation—causing the bearing to slightly rotate about its axis. These movements are known as pitch, roll and yaw.
The solution for minimizing pitch, roll and yaw is to alter the geometry of the recirculation pathways and eliminate roughness at key transition points. Three key transition points in a typical linear bearing are the entry zone, the load zone and the exit zone.

Tolerance chart.
The entry zone is the point just before the ball enters the load zone, where the ball is actually under load. At this point the ball is circulating through the end of the bearing and is rounding some critical radii before it re-enters the load zone.
As it passes these points, the rotation of the ball can be affected by surface roughness and contact angles inside the bearing, creating friction as well as additional unwanted motion.
In the load zone, the ball is rotating, and motion is typically consistent with uniform ball spacing. But as it approaches the exit zone, it goes from a point of load to no-load and is shot out of the load zone into the end of the bearing. This exit zone area is characterized by inconsistent ball spacing and ball-to-ball contact due to balls being shot from the load zone. Interactions in each of these key transition points lead to ball pulsations that can be felt when moving the bearing by hand. It is these ball pulsations which ultimately cause rocking motions that affect the overall smoothness of travel, and therefore affect the resulting precision of a machine measuring bone density, 3D coordinate measurement or other highly accurate medical devices.
HIGH-PRECISION BALL RAIL SOLVES
THE PROBLEM

Axes whose movements are known as pitch, roll and yaw.

Chart showing reduction in pitch, roll and yaw.
This eliminates the rough motion and the rolling of the ball rail system about its axis and creates not only accurate height and width dimensions, but also reliable linear motion about all the axes.

Explore the March 2007 Issue
Check out more from this issue and find your next story to read.
Latest from Today's Medical Developments
- Tariffs threaten small business growth, increase costs across industries
- Feed your brain on your lunch break at our upcoming Lunch + Learn!
- Robotics action plan for Europe
- Maximize your First Article Inspection efficiency and accuracy
- UPM Additive rebrands to UPM Advanced
- Master Bond’s LED415DC90Med dual-curable adhesive
- Minalex celebrates 60 years of excellence in miniature aluminum extrusions
- Tormach’s Chip Conveyor Kit for the 1500MX CNC Mill