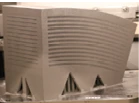

As next-generation of aircraft technology becomes more sophisticated with bigger and more efficient engines, head-up displays, electronics, and other advances, thermal management requirements regarding cooling will become increasingly aggressive. Heat exchangers will need to meet a more advanced level of performance in a more constrained space. This requires novel designs that are only possible to make using additive manufacturing (AM) techniques. Currently AM of heat exchangers is limited by the lack of a prescriptive process to achieve desired fit, form, and function. UTC Additive Manufacturing Center of Expertise (AMCOE) and United Technologies Research Center (UTRC) are developing an additively manufactured, high-performance conformal heat exchanger and a repeatable prescriptive systematic approach to develop additive heat exchangers for such applications.
Solution
The team developed a rigorous, systematic, and unique method of dividing up the heat exchanger geometry into key design features to create optimized process targeted toward those features through a fundamental understanding of powder-bed fusion process. In order to alleviate the technical risks, the team is using physics-based process models for defect prediction and in-process monitoring techniques for defect detection.
Performance-driven, feature-based process and product development approaches were used to achieve the heat exchanger metrics. Recognizing that minimizing pressure drop while maximizing heat transfer would require control of fin and parting sheet thicknesses and surface roughness, the primary focus was on developing the thinnest, smoothest possible defect-free fins and parting sheets. To obtain these key product characteristics, custom laser powder-bed process parameters and scan strategies were employed.

The team’s work not only led to the creation of a heat exchanger that can withstand aggressive performance demands (with no leakage and designed heat transfer), it also resulted in a scalable and more efficient process that addresses yield issues associated with conventional heat exchanger manufacturing process.
Using unique and engineered laser scan strategies, UTC’s AMCOE in partnership with America Makes developed a scalable developmental approach and prescriptive additive manufacturing process for enabling novel heat exchanger designs that can withstand the aggressive demands of modern aircraft technology with reduced leakage, higher heat transfer, and a lower rejection rate.
United Technologies Corp.
http://www.utc.com
This material is based on research sponsored by Air Force Research Laboratory under agreement number FA8650-16-2-7230. The U.S. Government is authorized to reproduce and distribute reprints for Governmental purposes notwithstanding any copyright notation thereon. The views and conclusions contained herein are those of the authors and should not be interpreted as necessarily representing the official policies or endorsements, either expressed or implied, of Air Force Research Laboratory or the U.S. Government.

Explore the Additive Manufacturing Guide Issue
Check out more from this issue and find your next story to read.
Latest from Today's Medical Developments
- Birk Manufacturing achieves ISO 13485 recertification
- SW North America's BA 322i twin-spindle CNC
- The role of robotics in precision medical device manufacturing
- Swiss Steel Group’s UGIMA-X machinable stainless-steel sets
- #51 - Manufacturing Matters - The Impact of M&A in MedTech 2024
- Visual Components: 25 years of simulation and programming software innovation
- Zimmer Biomet announces definitive agreement to Acquire Paragon 28
- Discover an innovative technology for EMI/ESD/TVS suppression